ECS-F1EE475K Programmable Timers and Oscillators Core Functional Technology1. Programmability:2. Precision Timing:3. Low Power Consumption:4. Wide Frequency Range:5. Temperature Stability:6. Integration with Microcontrollers:1. Consumer Electronics:2. Industrial Automation:3. Telecommunications:4. Medical Devices:5. Automotive Applications:6. IoT Devices: Application Development Cases ConclusionThe ECS-F1EE475K programmable timers and oscillators offer a versatile and effective solution for a wide array of applications. Their programmability, precision, low power consumption, and temperature stability make them ideal for use in consumer electronics, industrial automation, telecommunications, medical devices, automotive applications, and IoT devices. By harnessing these features, developers can create innovative solutions that meet the evolving demands of modern technology, driving advancements across various sectors.
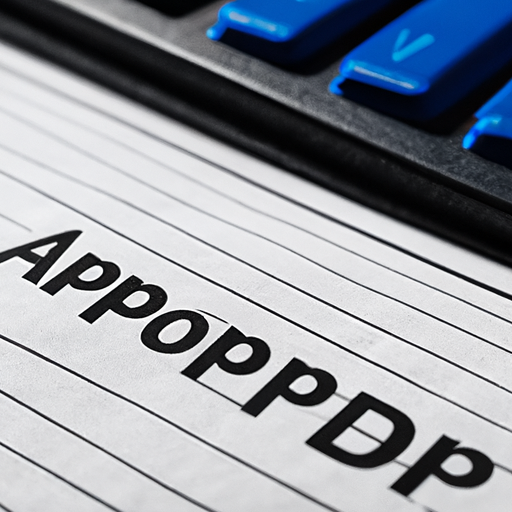
Application Development in Delay Lines for CFR-25JB-52-180R: Key Technologies and Success StoriesDelay lines are essential components in RF and microwave applications, playing a pivotal role in communication, radar, and signal processing systems. The CFR-25JB-52-180R is a specific delay line that exemplifies the advancements in this field. Below is an overview of the key technologies and notable success stories associated with the application development of delay lines, particularly focusing on the CFR-25JB-52-180R.
Key Technologies in Delay Lines1. Transmission Line Theory 2. Microstrip and Stripline Technologies 3. Digital Signal Processing (DSP) 4. Integrated Circuit (IC) Technology 5. Optical Delay Lines 6. Programmable Delay Lines 1. Telecommunications 2. Radar Systems 3. Consumer Electronics 4. Automotive Applications 5. Research and Development Success Stories ConclusionThe development and application of delay lines, such as the CFR-25JB-52-180R, are integral to many modern technologies. As systems become more complex and the demand for high-speed communication increases, the role of delay lines will continue to grow. Innovations in materials, design, and integration will likely lead to even more successful applications in the future, further enhancing the capabilities of RF and microwave systems. The ongoing evolution of delay line technology promises to support advancements across various industries, from telecommunications to automotive safety.
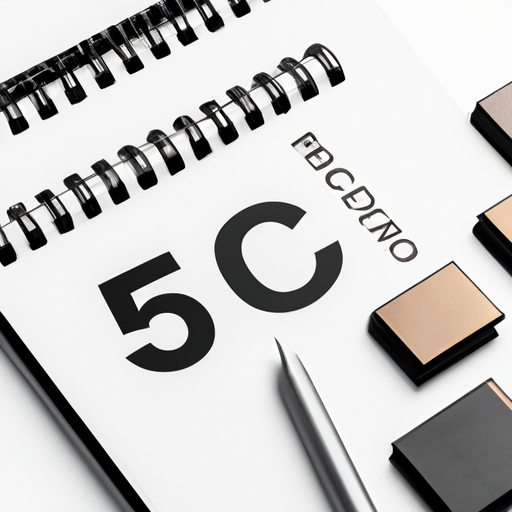
Application Development in Specialized ICs for CFR-50JB-52-180K: Key Technologies and Success StoriesWhile the CFR-50JB-52-180K is a specific type of resistor, the principles of application development in specialized integrated circuits (ICs) can be broadly applied across various electronic components, including resistors, capacitors, and ICs. Below, we explore key technologies and notable success stories in this field.
Key Technologies1. Application-Specific Integrated Circuits (ASICs)2. Field-Programmable Gate Arrays (FPGAs)3. Mixed-Signal ICs4. Power Management ICs (PMICs)5. Embedded Systems6. Simulation and Modeling Tools7. Advanced Packaging Technologies1. Consumer Electronics2. Automotive Industry3. Telecommunications4. Medical Devices5. Industrial Automation Success Stories ConclusionThe development of specialized ICs, including those that may interface with components like the CFR-50JB-52-180K resistor, is a dynamic and evolving field. Leveraging advanced technologies, these ICs meet the specific needs of various industries, driving innovation and efficiency. Success stories across consumer electronics, automotive, telecommunications, medical devices, and industrial automation underscore the importance of tailored solutions in shaping the future of electronic applications. As technology continues to advance, the role of specialized ICs will be pivotal in addressing the challenges and opportunities of tomorrow's electronic landscape.
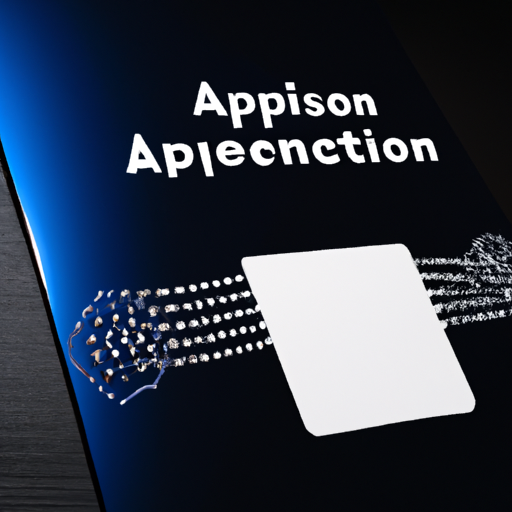
Application Development in Laser Drivers for ECS-F1EE106K: Key Technologies and Success StoriesDeveloping applications for laser drivers, particularly for a specific model like the ECS-F1EE106K, involves a combination of key technologies and methodologies. Here’s an overview of the essential components, technologies, and some success stories in this domain.
Key Technologies1. Laser Diode Technology2. Current Regulation3. Thermal Management4. Modulation Techniques5. Digital Signal Processing (DSP)6. Microcontroller Integration7. Communication Protocols8. Power Supply Design1. Telecommunications2. Medical Applications3. Industrial Laser Systems4. Consumer Electronics5. Research and Development Success Stories ConclusionThe development of applications for laser drivers like the ECS-F1EE106K involves a multidisciplinary approach, combining knowledge of electronics, optics, and software. By leveraging key technologies and learning from successful implementations across various industries, developers can create innovative solutions that meet the demands of modern applications. As laser technology continues to evolve, the potential for new applications and improvements in existing systems remains vast, positioning the ECS-F1EE106K as a pivotal component in the future of laser-driven technologies.
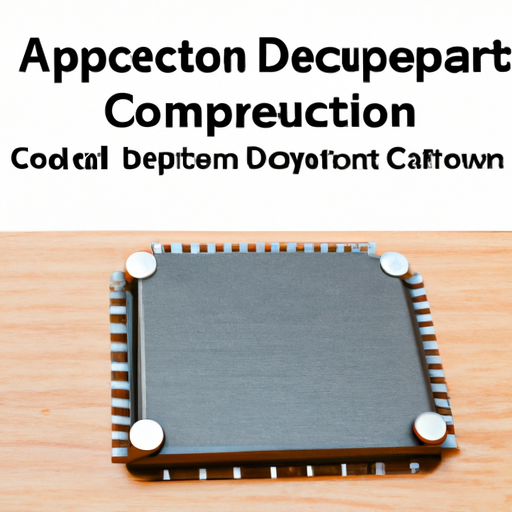
Application Development in Solid-State Thermostats: CFR-50JB-52-16KThe development of solid-state thermostats, such as the CFR-50JB-52-16K, represents a significant advancement in HVAC control technology. By leveraging cutting-edge technologies and methodologies, manufacturers can enhance performance, reliability, and user experience. Below is a detailed overview of key technologies and notable success stories in the realm of solid-state thermostat development.
Key Technologies1. Microcontroller Units (MCUs)2. Sensor Technology3. Wireless Communication4. User Interface (UI)5. Machine Learning and AI6. Energy Management Systems7. Solid-State Components8. Cloud Computing1. Nest Learning Thermostat2. Ecobee SmartThermostat3. Honeywell Home T94. Emerson Sensi Touch5. Tado Smart AC Control Success Stories ConclusionThe development of solid-state thermostats like the CFR-50JB-52-16K is driven by advancements in microcontrollers, sensor technology, and connectivity. The success stories of leading brands highlight the potential for innovation in this field, emphasizing the importance of user experience, energy efficiency, and integration with smart home ecosystems. As technology continues to evolve, we can anticipate even more sophisticated features and capabilities in future thermostat designs, paving the way for smarter, more efficient home climate control solutions.
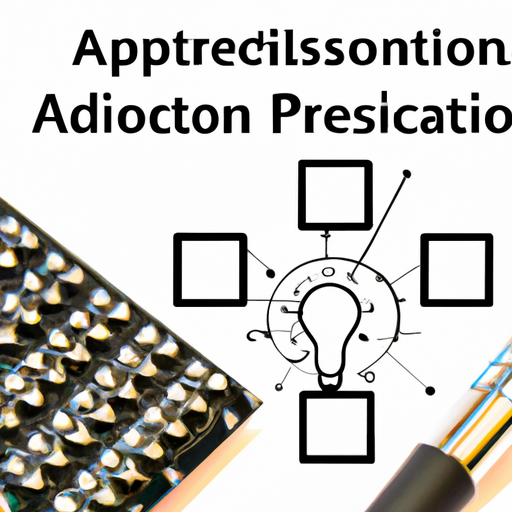
Application Development in the Photoelectric Industrial Sector for CFR-25JB-52-160RThe photoelectric industrial sector is rapidly evolving, with devices like the CFR-25JB-52-160R at the forefront of innovation. This development is characterized by the integration of advanced technologies that enhance the functionality, reliability, and efficiency of photoelectric sensors. Below, we delve deeper into the key technologies and notable success stories that illustrate the impact of these advancements.
Key Technologies1. Photoelectric Sensors2. Machine Learning and AI3. IoT Integration4. Robust Communication Protocols5. Environmental Adaptability1. Automotive Manufacturing2. Food and Beverage Industry3. Logistics and Warehousing4. Pharmaceutical Manufacturing5. Smart Agriculture Success Stories ConclusionThe application development in the photoelectric industrial sector, particularly for devices like the CFR-25JB-52-160R, is marked by significant technological advancements. The integration of photoelectric sensors with machine learning, IoT, and robust communication protocols has transformed various industries, leading to improved efficiency, reduced costs, and enhanced product quality. As the sector continues to innovate, the potential for further advancements in photoelectric technology remains vast, promising even greater benefits for industrial applications in the future.
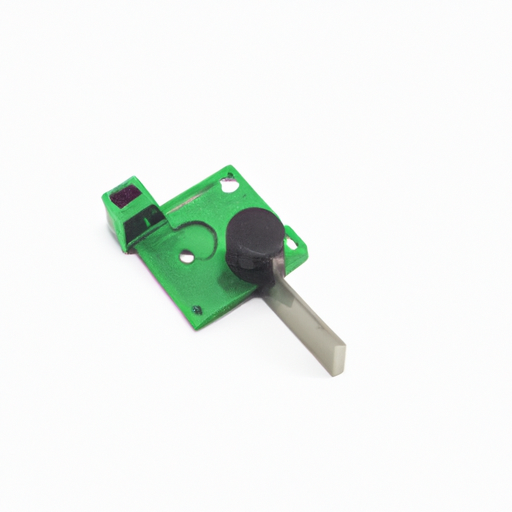
Overview of CFR-25JB-52-160K Specialized SensorsThe CFR-25JB-52-160K is a specialized sensor known for its precision and reliability in various applications. This sensor exemplifies the advancements in sensor technology, making it suitable for a wide range of industries. Below is a detailed overview of its core functional technologies and potential application development cases.
Core Functional Technologies of CFR-25JB-52-160K1. High Precision and Accuracy2. Robust Environmental Tolerance3. Compact Design4. Wireless Connectivity5. Integrated Data Processing6. Multi-Parameter Measurement1. Industrial Automation2. Environmental Monitoring3. Healthcare Monitoring4. Precision Agriculture5. Automotive Safety Systems6. Smart Building Technologies Application Development Cases ConclusionThe CFR-25JB-52-160K specialized sensor represents a significant advancement in sensor technology, offering high precision, environmental resilience, and versatile applications across various industries. Its capabilities make it an essential component in industrial automation, healthcare, environmental monitoring, smart agriculture, automotive safety, and building automation. As technology continues to evolve, the potential applications for specialized sensors like the CFR-25JB-52-160K will expand, driving innovation and efficiency across multiple sectors. For further insights and specific case studies, industry publications, technical journals, and manufacturer resources are recommended for in-depth exploration.
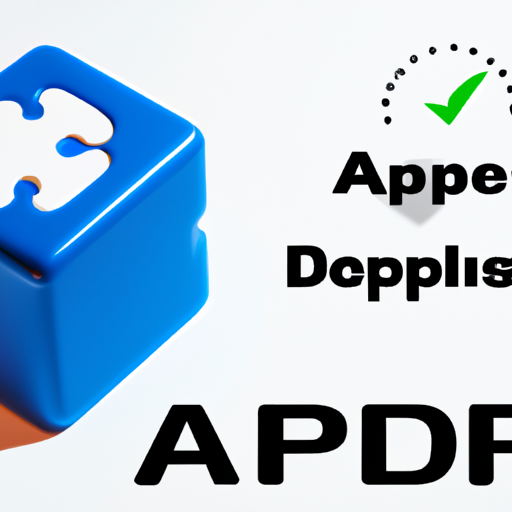
Application Development in Capacitive Touch Sensors: CFR-50JB-52-160KDeveloping applications that utilize capacitive touch sensors, such as the CFR-50JB-52-160K, involves a blend of advanced technologies and methodologies. Capacitive touch sensors are favored for their responsiveness, durability, and multi-touch capabilities. Below is a detailed overview of the key technologies involved in capacitive touch sensor application development, along with notable success stories across various industries.
Key Technologies1. Capacitive Sensing Technology2. Microcontroller Integration3. User Interface (UI) Design4. Power Management5. Environmental Considerations6. Prototyping and Testing1. Consumer Electronics2. Home Automation3. Automotive Applications4. Industrial Applications5. Healthcare Devices Success Stories ConclusionThe development of applications using capacitive touch sensors like the CFR-50JB-52-160K involves a combination of advanced sensing technology, microcontroller integration, thoughtful UI design, and rigorous testing. The success stories across various industries highlight the versatility and effectiveness of capacitive touch technology in enhancing user interaction and experience. As technology continues to evolve, we can expect even more innovative applications and improvements in capacitive touch sensing, paving the way for smarter, more intuitive devices.
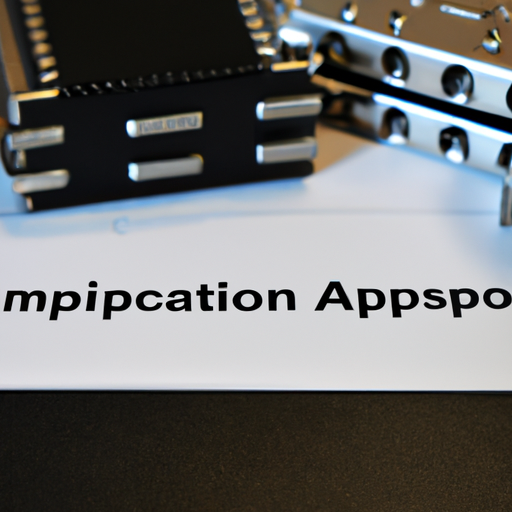
Application Development in Sensor and Transducer Amplifiers for CFR-50JB-52-160R: Key Technologies and Success StoriesThe development of applications utilizing sensor and transducer amplifiers, such as the CFR-50JB-52-160R, is a rapidly evolving field that integrates various technologies to enhance performance and functionality. Below is a detailed overview of the key technologies involved and notable success stories that illustrate their practical applications.
Key Technologies1. Signal Conditioning2. Analog-to-Digital Conversion (ADC)3. Microcontroller Integration4. Wireless Communication5. Power Management6. Calibration and Compensation7. Machine Learning and Data Analytics1. Industrial Automation2. Environmental Monitoring3. Healthcare Applications4. Smart Agriculture5. Automotive Sensors Success Stories ConclusionThe application development in sensor and transducer amplifiers, particularly with models like the CFR-50JB-52-160R, showcases a dynamic intersection of technology and innovation. The integration of advanced signal processing, microcontroller technology, and wireless communication has led to significant advancements across various industries. The success stories highlight the transformative impact of these technologies in enhancing operational efficiency, safety, and data-driven decision-making. As technology continues to advance, the potential for innovative applications in this domain will only grow, paving the way for smarter, more connected systems.
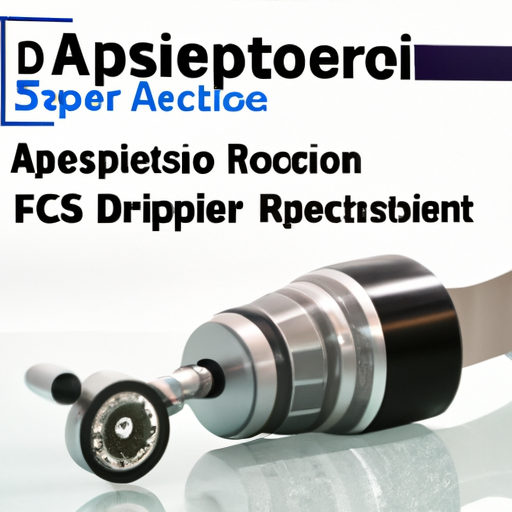
Application Development in Gyroscopes for CFR-25JB-52-15R: Key Technologies and Success StoriesThe development of gyroscopic applications in aviation, particularly in compliance with standards like CFR-25JB-52-15R, is crucial for ensuring the safety, reliability, and performance of aircraft systems. This regulation outlines the requirements for gyroscopic instruments, emphasizing their importance in navigation and control. Below are the key technologies and notable success stories in this field.
Key Technologies1. Micro-Electro-Mechanical Systems (MEMS) Gyroscopes2. Fiber Optic Gyroscopes (FOG)3. Ring Laser Gyroscopes (RLG)4. Kalman Filtering5. Sensor Fusion6. Software Development Kits (SDKs)1. Boeing 787 Dreamliner2. Airbus A3503. Autonomous Drones4. Spacecraft Navigation5. Augmented Reality (AR) Applications Success Stories ConclusionThe development of gyroscopic applications in compliance with standards like CFR-25JB-52-15R has led to significant advancements in aviation technology. The integration of various gyroscopic technologies, sophisticated algorithms, and sensor fusion techniques has resulted in safer, more efficient, and more reliable aircraft systems. As technology continues to evolve, we can expect further innovations in gyroscopic applications, enhancing the capabilities of modern aviation and contributing to the overall safety and efficiency of air travel.
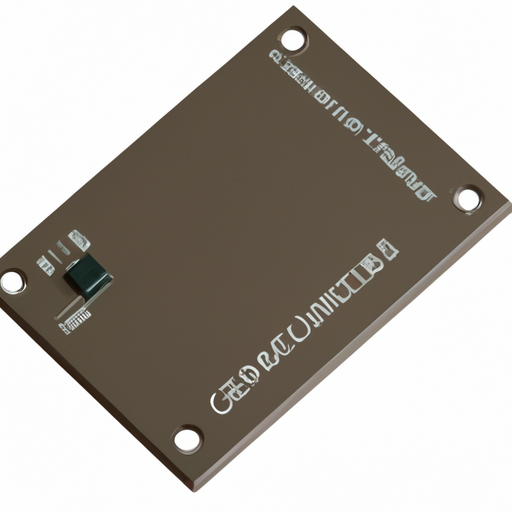
Overview of Linear and Compass Integrated Circuits (ICs)The CFR-25JB-52-15K component may not be widely recognized, but it serves as a reminder of the broader categories of Linear and Compass Integrated Circuits (ICs). These ICs are foundational in various applications, leveraging their core functional technologies to enhance performance and efficiency across multiple sectors.
Core Functional Technologies of Linear and Compass ICs 1. Linear ICs
- **Operational Amplifiers (Op-Amps)**: Essential for amplifying weak signals, Op-Amps are used in filters, oscillators, and signal conditioning circuits. They are critical in audio processing, instrumentation, and control systems.
- **Voltage Regulators**: These devices ensure a constant output voltage, which is vital for powering sensitive electronic components. They are used in power supply circuits to maintain stable operation despite fluctuations in input voltage.- Analog-to-Digital Converters (ADCs): ADCs convert analog signals (like temperature or light) into digital data, enabling microcontrollers to process real-world signals. They are widely used in data acquisition systems and digital signal processing. - Digital-to-Analog Converters (DACs): DACs perform the reverse function of ADCs, converting digital signals back into analog form. This is crucial in applications such as audio playback and control systems.
2. Compass ICs
- **Magnetometers**: These sensors detect magnetic fields and are integral to compass functionality. They provide directional data for navigation systems in smartphones, drones, and automotive applications.- Inertial Measurement Units (IMUs): IMUs combine accelerometers, gyroscopes, and magnetometers to track motion and orientation. They are essential in robotics, drones, and augmented reality applications.
- Sensor Fusion Algorithms: These algorithms integrate data from multiple sensors (like accelerometers and magnetometers) to enhance accuracy and reliability in navigation and motion tracking.
Application Development Cases 1. Consumer Electronics
- **Smartphones and Tablets**: Compass ICs enable navigation and orientation features, while linear ICs manage audio output and power efficiency. Applications include GPS navigation, augmented reality, and gaming.- Wearable Devices: Fitness trackers and smartwatches utilize compass ICs for navigation and activity tracking. Linear ICs help optimize battery life and manage sensor data.
2. Automotive Applications
- **Navigation Systems**: Compass ICs provide critical directional information for GPS systems, enhancing route accuracy and user experience.- Stability Control Systems: Linear ICs are used in systems that monitor vehicle dynamics, improving safety and performance through real-time adjustments.
3. Robotics and Drones
- **Autonomous Navigation**: Robots and drones rely on compass ICs for orientation and navigation, while linear ICs control motors and process sensor data for obstacle detection and avoidance.- Obstacle Avoidance: Linear ICs are integral in sensor systems that detect obstacles, enabling real-time decision-making and enhancing operational safety.
4. Industrial Automation
- **Positioning Systems**: Compass ICs are used in automated guided vehicles (AGVs) for precise navigation in complex environments like warehouses.- Process Control: Linear ICs are employed in control systems to ensure accurate measurements and reliable operation in manufacturing processes.
5. IoT Applications
- **Smart Home Devices**: Compass ICs can enhance smart home systems by providing orientation data, while linear ICs manage sensor data and control actuators for automation.- Environmental Monitoring: Linear ICs are used in sensors that monitor environmental conditions (like temperature and humidity), while compass ICs assist in geographic data collection for environmental studies.
ConclusionLinear and compass ICs are integral to modern technology, enabling a wide range of applications from consumer electronics to industrial automation. Their ability to process analog signals and provide accurate directional information is crucial in enhancing device functionality and user experience. As technology continues to evolve, the development and integration of these ICs will remain a focal point for innovation in various fields.
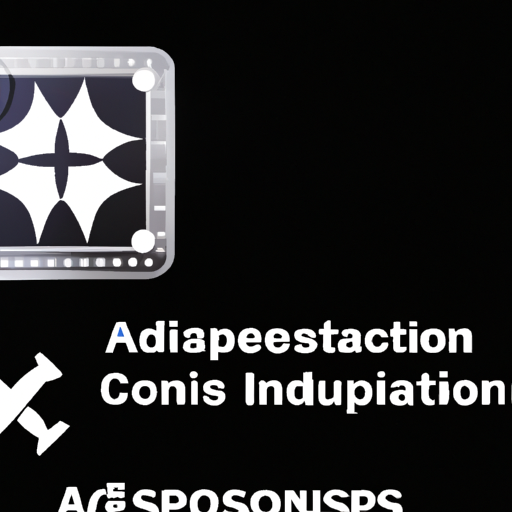
Application Development in Compass and Magnetic Field Modules for CFR-50JB-52-15KThe integration of Compass and Magnetic Field modules, particularly in the context of CFR-50JB-52-15K, represents a significant advancement in various fields, including navigation, robotics, and wearable technology. This document outlines key technologies and success stories that illustrate the potential of these modules.
Key Technologies1. Magnetic Field Sensors2. Microcontrollers and Embedded Systems3. Data Fusion Algorithms4. Wireless Communication5. Machine Learning6. User Interface Development1. Smart Navigation Systems2. Wearable Technology3. Industrial Applications4. Robotics5. Geophysical Surveys6. Smartphone Applications Success Stories ConclusionThe integration of Compass and Magnetic Field modules in application development for CFR-50JB-52-15K offers vast opportunities across multiple industries. By leveraging advanced sensor technologies, data processing techniques, and user-friendly interfaces, developers can create innovative solutions that enhance navigation, monitoring, and user interaction. The success stories presented highlight the versatility and significant impact of these technologies in real-world applications, paving the way for future advancements in this field.
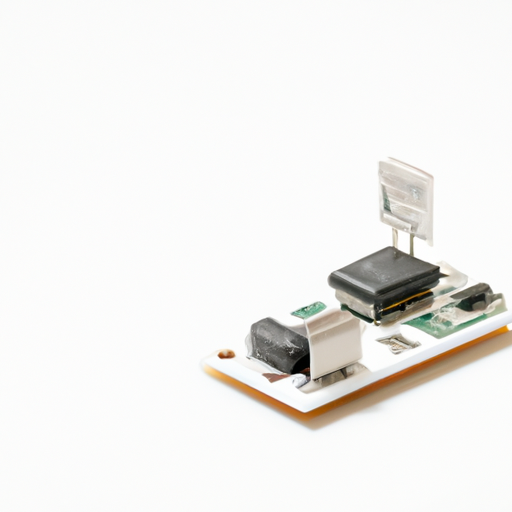
Overview of CFR-50JB-52-15R Position, Proximity, Speed Sensor ModuleThe CFR-50JB-52-15R is a specific model of a position, proximity, and speed sensor module that exemplifies the core functional technologies in this domain. Below is a detailed overview of the core functional technologies and application development cases relevant to such sensor modules.
Core Functional Technologies1. Position Sensors2. Proximity Sensors3. Speed Sensors1. Industrial Automation2. Automotive Industry3. Consumer Electronics4. Smart Home Devices5. Healthcare6. Aerospace and Defense Application Development Cases ConclusionThe CFR-50JB-52-15R position, proximity, and speed sensor module represents a versatile solution applicable across various industries. Its integration into automation, automotive, consumer electronics, smart home devices, healthcare, and aerospace applications highlights the importance of accurate and reliable sensor technology. As industries continue to evolve, the role of such sensor modules will expand, particularly with advancements in IoT and AI, leading to smarter and more efficient systems. For further insights, industry journals, technical publications, and manufacturer resources can provide in-depth case studies and technological advancements.
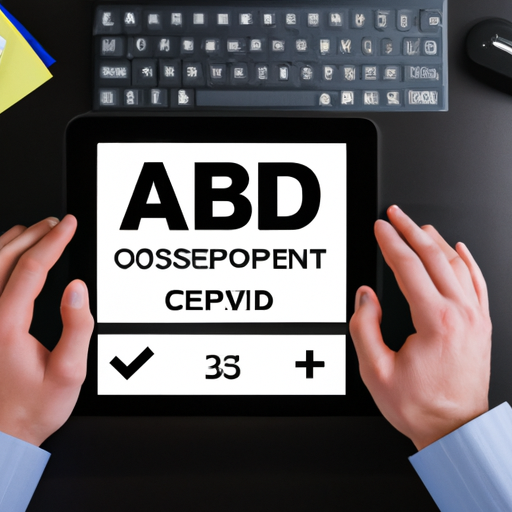
Application Development in Multifunction for CFR-25JB-52-150R: Key Technologies and Success StoriesThe CFR-25JB-52-150R, as a multifunction device, likely serves a variety of applications across sectors such as industrial automation, telecommunications, and more. While specific details about this model are not available, we can explore the key technologies that underpin multifunction devices and highlight success stories that illustrate their impact.
Key Technologies in Multifunction Application Development1. Embedded Systems2. Internet of Things (IoT)3. Machine Learning and AI4. User Interface (UI) and User Experience (UX) Design5. Cloud Computing6. Security Technologies7. Modular Design1. Smart Home Devices2. Industrial Automation3. Healthcare Solutions4. Telecommunications5. Automotive Applications Success Stories ConclusionThe development of multifunction applications for devices like the CFR-25JB-52-150R involves a strategic blend of advanced technologies, user-centric design, and innovative solutions tailored to meet diverse user needs. The success stories across various industries highlight the transformative potential of these devices, showcasing their ability to enhance operational efficiency, improve user experiences, and drive innovation. As technology continues to advance, the capabilities and applications of multifunction devices are expected to expand, further revolutionizing how industries operate and interact with technology.