What are the Product Standards for Color Ring Resistors?
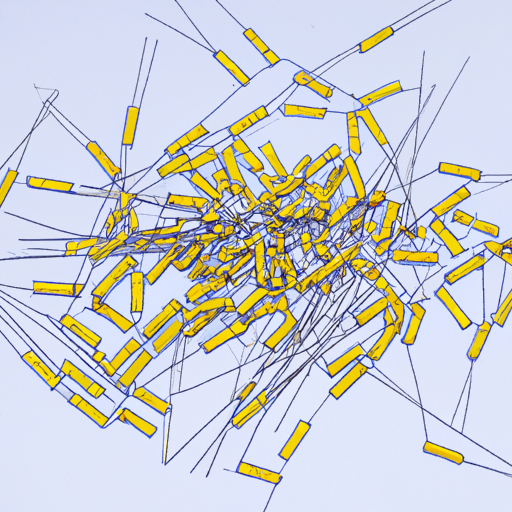
I. Introduction
Color ring resistors are ubiquitous components in electronic circuits, serving a fundamental role in controlling current flow. These resistors are characterized by their distinctive color bands, which indicate their resistance values and tolerances. As the electronics industry continues to evolve, the importance of product standards for color ring resistors cannot be overstated. Standards ensure that these components meet specific performance criteria, enhancing reliability and safety in electronic devices. This article will explore the various product standards for color ring resistors, delving into their significance, the color coding system, international and national standards, manufacturing processes, performance criteria, and future trends in resistor technology.
II. Understanding Resistors
A. Basic Principles of Resistance
At the heart of electronics lies the concept of resistance, which is defined as the opposition to the flow of electric current. According to Ohm's Law, the relationship between voltage (V), current (I), and resistance (R) is expressed as V = I × R. This fundamental principle underpins the operation of resistors, which are classified into various types, including fixed, variable, and specialty resistors.
B. Role of Resistors in Electronic Circuits
Resistors play a crucial role in electronic circuits by controlling current flow, dividing voltages, and protecting sensitive components from excessive current. They are essential in applications ranging from simple circuits to complex systems, ensuring that devices operate within their specified parameters.
C. Introduction to Color Coding in Resistors
Color coding is a standardized method used to indicate the resistance value and tolerance of resistors. Each color corresponds to a specific number, allowing users to quickly identify the resistor's specifications without needing to measure it directly.
III. Color Coding System
A. Explanation of the Color Code
The color code for resistors consists of a series of colored bands printed on the resistor's body. Each color represents a digit or a multiplier, with the first two or three bands indicating the significant digits of the resistance value, the next band representing the multiplier, and the final band denoting tolerance.
B. Standard Color Code for 4-band, 5-band, and 6-band Resistors
4-band Resistors: The first two bands represent significant digits, the third band is the multiplier, and the fourth band indicates tolerance.
5-band Resistors: The first three bands represent significant digits, the fourth band is the multiplier, and the fifth band indicates tolerance.
6-band Resistors: In addition to the previous bands, the sixth band often represents the temperature coefficient.
C. Tolerance and Temperature Coefficient Bands
Tolerance indicates how much the actual resistance can vary from the stated value, typically expressed as a percentage. The temperature coefficient band indicates how much the resistance changes with temperature, which is crucial for applications where temperature fluctuations are expected.
IV. Product Standards for Color Ring Resistors
A. International Standards
1. IEC (International Electrotechnical Commission) Standards
The IEC sets international standards for electrical and electronic devices, including resistors. These standards ensure that components are safe, reliable, and compatible across different regions.
2. ANSI (American National Standards Institute) Standards
ANSI standards complement IEC guidelines, providing additional specifications for resistors used in the United States. Compliance with ANSI standards is essential for manufacturers targeting the North American market.
B. National Standards
1. JIS (Japanese Industrial Standards)
In Japan, JIS standards govern the manufacturing and testing of resistors, ensuring that they meet specific quality and performance criteria.
2. DIN (Deutsches Institut für Normung) Standards
Germany's DIN standards provide guidelines for resistor manufacturing, focusing on quality assurance and performance metrics.
C. Compliance and Certification Processes
1. Importance of Compliance
Compliance with established standards is crucial for manufacturers, as it ensures that their products are safe and reliable. Non-compliance can lead to product recalls, legal issues, and damage to a company's reputation.
2. Testing and Quality Assurance
Manufacturers must implement rigorous testing and quality assurance processes to verify that their resistors meet the required standards. This includes electrical testing, environmental testing, and reliability assessments.
V. Manufacturing Standards
A. Material Specifications
1. Types of Materials Used in Resistors
Resistors can be made from various materials, including carbon, metal film, and wire-wound materials. The choice of material affects the resistor's performance, including its stability, tolerance, and temperature coefficient.
2. Impact of Material Choice on Performance
Different materials offer distinct advantages and disadvantages. For example, metal film resistors provide better accuracy and stability than carbon resistors, making them suitable for precision applications.
B. Production Processes
1. Automated vs. Manual Production
The production of resistors can be automated or manual, with automated processes typically offering higher consistency and efficiency. However, manual production may be necessary for specialized or low-volume applications.
2. Quality Control Measures in Manufacturing
Quality control is essential in resistor manufacturing to ensure that each component meets the required specifications. This includes regular inspections, testing, and adherence to established manufacturing protocols.
C. Environmental Considerations
1. RoHS (Restriction of Hazardous Substances) Compliance
Manufacturers must comply with RoHS regulations, which restrict the use of hazardous substances in electronic components. This ensures that resistors are safe for both consumers and the environment.
2. WEEE (Waste Electrical and Electronic Equipment) Directives
WEEE directives govern the disposal and recycling of electronic waste, encouraging manufacturers to design products that are easier to recycle and less harmful to the environment.
VI. Performance Standards
A. Electrical Performance Criteria
1. Resistance Tolerance
Resistance tolerance is a critical performance criterion, indicating how much the actual resistance can deviate from the specified value. Common tolerances include ±1%, ±5%, and ±10%.
2. Power Rating
The power rating of a resistor indicates the maximum amount of power it can dissipate without overheating. This is crucial for ensuring that resistors operate safely within their specified limits.
3. Temperature Coefficient
The temperature coefficient measures how much the resistance changes with temperature. A low temperature coefficient is desirable for applications requiring stable performance across varying temperatures.
B. Reliability and Lifespan
1. Factors Affecting Resistor Longevity
Several factors can affect the longevity of resistors, including operating temperature, humidity, and electrical stress. Understanding these factors is essential for designing reliable circuits.
2. Testing for Reliability
Manufacturers conduct reliability testing to assess how resistors perform under various conditions, ensuring that they meet the expected lifespan and performance criteria.
C. Application-Specific Standards
1. Automotive, Industrial, and Consumer Electronics Applications
Different applications may require specific performance standards. For example, automotive resistors must withstand harsher environmental conditions than those used in consumer electronics.
VII. Challenges and Innovations in Resistor Standards
A. Evolving Technology and Its Impact on Standards
As technology advances, the standards governing resistors must also evolve. New materials, manufacturing techniques, and applications necessitate updates to existing standards to ensure safety and performance.
B. The Role of Digitalization in Resistor Manufacturing
Digitalization is transforming resistor manufacturing, enabling greater precision, efficiency, and traceability. This shift is likely to influence future standards and compliance processes.
C. Future Trends in Resistor Technology and Standards
Emerging trends, such as the development of smart resistors and the integration of resistors into printed circuit boards (PCBs), will shape the future of resistor technology and the standards that govern them.
VIII. Conclusion
In conclusion, product standards for color ring resistors are vital for ensuring the quality, reliability, and safety of electronic components. These standards encompass various aspects, from manufacturing processes to performance criteria, and are essential for maintaining the integrity of electronic devices. As technology continues to evolve, so too will the standards that govern resistors, ensuring that they meet the demands of modern applications. The future of resistor technology promises exciting innovations, and adherence to established standards will remain crucial in navigating this dynamic landscape.
IX. References
- International Electrotechnical Commission (IEC)
- American National Standards Institute (ANSI)
- Japanese Industrial Standards (JIS)
- Deutsches Institut für Normung (DIN)
- Restriction of Hazardous Substances (RoHS) Directive
- Waste Electrical and Electronic Equipment (WEEE) Directive
This comprehensive overview of product standards for color ring resistors highlights their significance in the electronics industry, providing a foundation for understanding the complexities of resistor technology and its future.
What are the Product Standards for Color Ring Resistors?
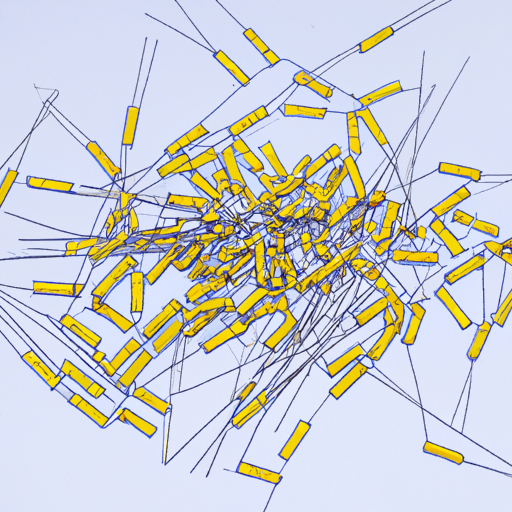
I. Introduction
Color ring resistors are ubiquitous components in electronic circuits, serving a fundamental role in controlling current flow. These resistors are characterized by their distinctive color bands, which indicate their resistance values and tolerances. As the electronics industry continues to evolve, the importance of product standards for color ring resistors cannot be overstated. Standards ensure that these components meet specific performance criteria, enhancing reliability and safety in electronic devices. This article will explore the various product standards for color ring resistors, delving into their significance, the color coding system, international and national standards, manufacturing processes, performance criteria, and future trends in resistor technology.
II. Understanding Resistors
A. Basic Principles of Resistance
At the heart of electronics lies the concept of resistance, which is defined as the opposition to the flow of electric current. According to Ohm's Law, the relationship between voltage (V), current (I), and resistance (R) is expressed as V = I × R. This fundamental principle underpins the operation of resistors, which are classified into various types, including fixed, variable, and specialty resistors.
B. Role of Resistors in Electronic Circuits
Resistors play a crucial role in electronic circuits by controlling current flow, dividing voltages, and protecting sensitive components from excessive current. They are essential in applications ranging from simple circuits to complex systems, ensuring that devices operate within their specified parameters.
C. Introduction to Color Coding in Resistors
Color coding is a standardized method used to indicate the resistance value and tolerance of resistors. Each color corresponds to a specific number, allowing users to quickly identify the resistor's specifications without needing to measure it directly.
III. Color Coding System
A. Explanation of the Color Code
The color code for resistors consists of a series of colored bands printed on the resistor's body. Each color represents a digit or a multiplier, with the first two or three bands indicating the significant digits of the resistance value, the next band representing the multiplier, and the final band denoting tolerance.
B. Standard Color Code for 4-band, 5-band, and 6-band Resistors
4-band Resistors: The first two bands represent significant digits, the third band is the multiplier, and the fourth band indicates tolerance.
5-band Resistors: The first three bands represent significant digits, the fourth band is the multiplier, and the fifth band indicates tolerance.
6-band Resistors: In addition to the previous bands, the sixth band often represents the temperature coefficient.
C. Tolerance and Temperature Coefficient Bands
Tolerance indicates how much the actual resistance can vary from the stated value, typically expressed as a percentage. The temperature coefficient band indicates how much the resistance changes with temperature, which is crucial for applications where temperature fluctuations are expected.
IV. Product Standards for Color Ring Resistors
A. International Standards
1. IEC (International Electrotechnical Commission) Standards
The IEC sets international standards for electrical and electronic devices, including resistors. These standards ensure that components are safe, reliable, and compatible across different regions.
2. ANSI (American National Standards Institute) Standards
ANSI standards complement IEC guidelines, providing additional specifications for resistors used in the United States. Compliance with ANSI standards is essential for manufacturers targeting the North American market.
B. National Standards
1. JIS (Japanese Industrial Standards)
In Japan, JIS standards govern the manufacturing and testing of resistors, ensuring that they meet specific quality and performance criteria.
2. DIN (Deutsches Institut für Normung) Standards
Germany's DIN standards provide guidelines for resistor manufacturing, focusing on quality assurance and performance metrics.
C. Compliance and Certification Processes
1. Importance of Compliance
Compliance with established standards is crucial for manufacturers, as it ensures that their products are safe and reliable. Non-compliance can lead to product recalls, legal issues, and damage to a company's reputation.
2. Testing and Quality Assurance
Manufacturers must implement rigorous testing and quality assurance processes to verify that their resistors meet the required standards. This includes electrical testing, environmental testing, and reliability assessments.
V. Manufacturing Standards
A. Material Specifications
1. Types of Materials Used in Resistors
Resistors can be made from various materials, including carbon, metal film, and wire-wound materials. The choice of material affects the resistor's performance, including its stability, tolerance, and temperature coefficient.
2. Impact of Material Choice on Performance
Different materials offer distinct advantages and disadvantages. For example, metal film resistors provide better accuracy and stability than carbon resistors, making them suitable for precision applications.
B. Production Processes
1. Automated vs. Manual Production
The production of resistors can be automated or manual, with automated processes typically offering higher consistency and efficiency. However, manual production may be necessary for specialized or low-volume applications.
2. Quality Control Measures in Manufacturing
Quality control is essential in resistor manufacturing to ensure that each component meets the required specifications. This includes regular inspections, testing, and adherence to established manufacturing protocols.
C. Environmental Considerations
1. RoHS (Restriction of Hazardous Substances) Compliance
Manufacturers must comply with RoHS regulations, which restrict the use of hazardous substances in electronic components. This ensures that resistors are safe for both consumers and the environment.
2. WEEE (Waste Electrical and Electronic Equipment) Directives
WEEE directives govern the disposal and recycling of electronic waste, encouraging manufacturers to design products that are easier to recycle and less harmful to the environment.
VI. Performance Standards
A. Electrical Performance Criteria
1. Resistance Tolerance
Resistance tolerance is a critical performance criterion, indicating how much the actual resistance can deviate from the specified value. Common tolerances include ±1%, ±5%, and ±10%.
2. Power Rating
The power rating of a resistor indicates the maximum amount of power it can dissipate without overheating. This is crucial for ensuring that resistors operate safely within their specified limits.
3. Temperature Coefficient
The temperature coefficient measures how much the resistance changes with temperature. A low temperature coefficient is desirable for applications requiring stable performance across varying temperatures.
B. Reliability and Lifespan
1. Factors Affecting Resistor Longevity
Several factors can affect the longevity of resistors, including operating temperature, humidity, and electrical stress. Understanding these factors is essential for designing reliable circuits.
2. Testing for Reliability
Manufacturers conduct reliability testing to assess how resistors perform under various conditions, ensuring that they meet the expected lifespan and performance criteria.
C. Application-Specific Standards
1. Automotive, Industrial, and Consumer Electronics Applications
Different applications may require specific performance standards. For example, automotive resistors must withstand harsher environmental conditions than those used in consumer electronics.
VII. Challenges and Innovations in Resistor Standards
A. Evolving Technology and Its Impact on Standards
As technology advances, the standards governing resistors must also evolve. New materials, manufacturing techniques, and applications necessitate updates to existing standards to ensure safety and performance.
B. The Role of Digitalization in Resistor Manufacturing
Digitalization is transforming resistor manufacturing, enabling greater precision, efficiency, and traceability. This shift is likely to influence future standards and compliance processes.
C. Future Trends in Resistor Technology and Standards
Emerging trends, such as the development of smart resistors and the integration of resistors into printed circuit boards (PCBs), will shape the future of resistor technology and the standards that govern them.
VIII. Conclusion
In conclusion, product standards for color ring resistors are vital for ensuring the quality, reliability, and safety of electronic components. These standards encompass various aspects, from manufacturing processes to performance criteria, and are essential for maintaining the integrity of electronic devices. As technology continues to evolve, so too will the standards that govern resistors, ensuring that they meet the demands of modern applications. The future of resistor technology promises exciting innovations, and adherence to established standards will remain crucial in navigating this dynamic landscape.
IX. References
- International Electrotechnical Commission (IEC)
- American National Standards Institute (ANSI)
- Japanese Industrial Standards (JIS)
- Deutsches Institut für Normung (DIN)
- Restriction of Hazardous Substances (RoHS) Directive
- Waste Electrical and Electronic Equipment (WEEE) Directive
This comprehensive overview of product standards for color ring resistors highlights their significance in the electronics industry, providing a foundation for understanding the complexities of resistor technology and its future.