What are the Manufacturing Processes of the Latest Chip Resistors?
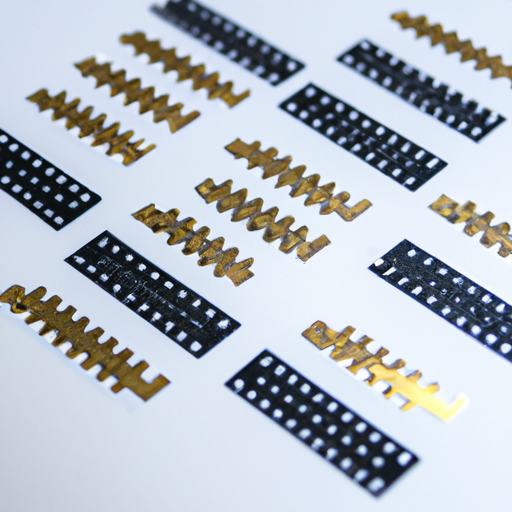
I. Introduction
Chip resistors are essential components in modern electronic devices, serving the critical function of controlling current flow and voltage levels. These tiny components are ubiquitous in everything from smartphones and computers to automotive systems and medical devices. As technology has advanced, so too have the manufacturing processes for chip resistors, evolving to meet the demands of increasingly compact and efficient electronic designs. This blog post will explore the various types of chip resistors, the raw materials used in their production, the detailed manufacturing processes, recent innovations, challenges faced by manufacturers, and future trends in the industry.
II. Types of Chip Resistors
A. Thin Film Resistors
Thin film resistors are characterized by their precise resistance values and excellent stability. They are made by depositing a thin layer of conductive material onto a substrate, allowing for high accuracy and low noise. These resistors are commonly used in applications requiring high precision, such as in medical devices and high-frequency circuits.
B. Thick Film Resistors
Thick film resistors, on the other hand, are made by applying a thicker layer of resistive paste onto a substrate. This type of resistor is known for its robustness and is often used in applications where high power handling is required, such as in power supplies and automotive electronics. Thick film resistors are generally less expensive than thin film resistors, making them a popular choice for many applications.
C. Other Types
In addition to thin and thick film resistors, there are other types of chip resistors, including wirewound and metal oxide resistors. Wirewound resistors are constructed by winding a metal wire around a core, providing high precision and stability. Metal oxide resistors, made from metal oxide films, are known for their high-temperature stability and are often used in high-voltage applications.
III. Raw Materials Used in Chip Resistor Manufacturing
A. Conductive Materials
The choice of conductive materials is crucial in chip resistor manufacturing. Common materials include metal films such as nickel and gold, which are used in thin film resistors due to their excellent conductivity and stability. Carbon-based materials are also popular, particularly in thick film resistors, where they provide a cost-effective solution with good performance.
B. Substrates
The substrate serves as the foundation for the resistor and plays a significant role in its performance. Ceramic materials are commonly used for their thermal stability and electrical insulation properties. Organic materials are also gaining popularity due to their lightweight and flexible characteristics, making them suitable for various applications.
C. Insulating Materials
Insulating materials are essential for ensuring the reliability and performance of chip resistors. Epoxy resins are widely used for their excellent adhesion and insulating properties, while glass is often employed for its high-temperature resistance and durability.
IV. Manufacturing Processes
A. Thin Film Resistor Manufacturing
The manufacturing process for thin film resistors involves several key steps:
1. **Substrate Preparation**: The substrate is cleaned and prepared to ensure optimal adhesion of the conductive films.
2. **Deposition of Conductive Films**: This can be achieved through methods such as sputtering or evaporation, where a thin layer of conductive material is deposited onto the substrate.
3. **Photolithography**: A photoresist layer is applied, and patterns are created using ultraviolet light, allowing for precise control over the resistor's dimensions.
4. **Etching**: The unwanted material is removed through chemical or plasma etching, leaving behind the desired resistor pattern.
5. **Passivation**: A protective layer is applied to enhance the resistor's stability and protect it from environmental factors.
B. Thick Film Resistor Manufacturing
The thick film resistor manufacturing process includes:
1. **Paste Preparation**: A resistive paste is formulated, typically containing conductive materials mixed with a binder.
2. **Screen Printing**: The paste is applied to the substrate using a screen printing technique, allowing for the creation of thick layers.
3. **Firing Process**: The printed resistors are fired in a kiln, which cures the paste and forms a solid resistive layer.
4. **Trimming and Testing**: The resistors are trimmed to achieve the desired resistance values, followed by rigorous testing to ensure quality and performance.
C. Wirewound Resistor Manufacturing
The manufacturing of wirewound resistors involves:
1. **Wire Selection and Winding**: A suitable metal wire is selected based on the desired resistance and power rating, then wound around a core.
2. **Insulation and Encapsulation**: The wound resistor is insulated and encapsulated to protect it from environmental factors and ensure reliability.
D. Quality Control and Testing
Quality control is a critical aspect of chip resistor manufacturing. Various testing methods are employed, including:
1. **Electrical Testing**: Resistors are tested for their resistance values and tolerance levels.
2. **Environmental Testing**: Resistors undergo tests to assess their performance under different environmental conditions, such as temperature and humidity.
3. **Reliability Testing**: Long-term reliability tests are conducted to ensure that the resistors will perform consistently over time.
V. Innovations in Chip Resistor Manufacturing
The chip resistor manufacturing industry has seen significant innovations in recent years:
A. Advances in Materials Science
New materials are being developed to enhance the performance of chip resistors. For example, researchers are exploring nanomaterials and composites that offer improved conductivity and stability.
B. Automation and Industry 4.0
The integration of automation and Industry 4.0 technologies is revolutionizing the manufacturing process. Smart factories equipped with IoT devices and AI-driven analytics enable real-time monitoring and optimization of production processes.
C. Miniaturization and Integration
As electronic devices become smaller and more complex, the demand for miniaturized chip resistors has increased. Manufacturers are developing integrated solutions that combine resistors with other components, reducing space and improving performance.
D. Environmental Considerations and Sustainability
Sustainability is becoming a key focus in chip resistor manufacturing. Companies are exploring eco-friendly materials and processes to minimize their environmental impact, including the use of recyclable materials and energy-efficient manufacturing techniques.
VI. Challenges in Chip Resistor Manufacturing
Despite the advancements in technology, the chip resistor manufacturing industry faces several challenges:
A. Supply Chain Issues
Global supply chain disruptions have impacted the availability of raw materials and components, leading to delays and increased costs for manufacturers.
B. Cost Management
As the demand for high-performance resistors grows, manufacturers must find ways to manage costs while maintaining quality and performance.
C. Meeting Increasing Demand
The rapid growth of the electronics market has led to an increased demand for chip resistors, putting pressure on manufacturers to scale production while ensuring reliability and performance.
VII. Future Trends in Chip Resistor Manufacturing
Looking ahead, several trends are expected to shape the future of chip resistor manufacturing:
A. Emerging Technologies
The rise of flexible electronics and wearable devices is driving the development of new types of chip resistors that can conform to various shapes and sizes.
B. Potential Impact of AI and Machine Learning
AI and machine learning technologies are poised to enhance manufacturing processes, enabling predictive maintenance, quality control, and process optimization.
C. Predictions for Market Growth
The chip resistor market is expected to continue growing, driven by advancements in technology and increasing demand for electronic devices across various industries.
VIII. Conclusion
Chip resistors play a vital role in the functionality of modern electronic devices, and their manufacturing processes have evolved significantly to meet the demands of the industry. From the types of resistors available to the raw materials and innovative manufacturing techniques, the landscape of chip resistor production is dynamic and continually advancing. As we look to the future, the integration of new technologies and a focus on sustainability will likely shape the next generation of chip resistors, ensuring their continued relevance in an ever-evolving electronic world.
IX. References
- Academic journals on materials science and electronics.
- Industry reports from market research firms.
- Manufacturer specifications and white papers on chip resistor technology.
This comprehensive overview of chip resistor manufacturing processes highlights the importance of these components in modern electronics and the innovations driving their production. As technology continues to advance, chip resistors will remain a cornerstone of electronic design and functionality.
What are the Manufacturing Processes of the Latest Chip Resistors?
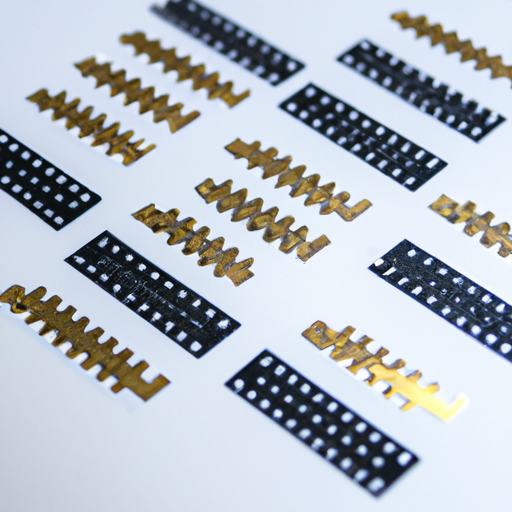
I. Introduction
Chip resistors are essential components in modern electronic devices, serving the critical function of controlling current flow and voltage levels. These tiny components are ubiquitous in everything from smartphones and computers to automotive systems and medical devices. As technology has advanced, so too have the manufacturing processes for chip resistors, evolving to meet the demands of increasingly compact and efficient electronic designs. This blog post will explore the various types of chip resistors, the raw materials used in their production, the detailed manufacturing processes, recent innovations, challenges faced by manufacturers, and future trends in the industry.
II. Types of Chip Resistors
A. Thin Film Resistors
Thin film resistors are characterized by their precise resistance values and excellent stability. They are made by depositing a thin layer of conductive material onto a substrate, allowing for high accuracy and low noise. These resistors are commonly used in applications requiring high precision, such as in medical devices and high-frequency circuits.
B. Thick Film Resistors
Thick film resistors, on the other hand, are made by applying a thicker layer of resistive paste onto a substrate. This type of resistor is known for its robustness and is often used in applications where high power handling is required, such as in power supplies and automotive electronics. Thick film resistors are generally less expensive than thin film resistors, making them a popular choice for many applications.
C. Other Types
In addition to thin and thick film resistors, there are other types of chip resistors, including wirewound and metal oxide resistors. Wirewound resistors are constructed by winding a metal wire around a core, providing high precision and stability. Metal oxide resistors, made from metal oxide films, are known for their high-temperature stability and are often used in high-voltage applications.
III. Raw Materials Used in Chip Resistor Manufacturing
A. Conductive Materials
The choice of conductive materials is crucial in chip resistor manufacturing. Common materials include metal films such as nickel and gold, which are used in thin film resistors due to their excellent conductivity and stability. Carbon-based materials are also popular, particularly in thick film resistors, where they provide a cost-effective solution with good performance.
B. Substrates
The substrate serves as the foundation for the resistor and plays a significant role in its performance. Ceramic materials are commonly used for their thermal stability and electrical insulation properties. Organic materials are also gaining popularity due to their lightweight and flexible characteristics, making them suitable for various applications.
C. Insulating Materials
Insulating materials are essential for ensuring the reliability and performance of chip resistors. Epoxy resins are widely used for their excellent adhesion and insulating properties, while glass is often employed for its high-temperature resistance and durability.
IV. Manufacturing Processes
A. Thin Film Resistor Manufacturing
The manufacturing process for thin film resistors involves several key steps:
1. **Substrate Preparation**: The substrate is cleaned and prepared to ensure optimal adhesion of the conductive films.
2. **Deposition of Conductive Films**: This can be achieved through methods such as sputtering or evaporation, where a thin layer of conductive material is deposited onto the substrate.
3. **Photolithography**: A photoresist layer is applied, and patterns are created using ultraviolet light, allowing for precise control over the resistor's dimensions.
4. **Etching**: The unwanted material is removed through chemical or plasma etching, leaving behind the desired resistor pattern.
5. **Passivation**: A protective layer is applied to enhance the resistor's stability and protect it from environmental factors.
B. Thick Film Resistor Manufacturing
The thick film resistor manufacturing process includes:
1. **Paste Preparation**: A resistive paste is formulated, typically containing conductive materials mixed with a binder.
2. **Screen Printing**: The paste is applied to the substrate using a screen printing technique, allowing for the creation of thick layers.
3. **Firing Process**: The printed resistors are fired in a kiln, which cures the paste and forms a solid resistive layer.
4. **Trimming and Testing**: The resistors are trimmed to achieve the desired resistance values, followed by rigorous testing to ensure quality and performance.
C. Wirewound Resistor Manufacturing
The manufacturing of wirewound resistors involves:
1. **Wire Selection and Winding**: A suitable metal wire is selected based on the desired resistance and power rating, then wound around a core.
2. **Insulation and Encapsulation**: The wound resistor is insulated and encapsulated to protect it from environmental factors and ensure reliability.
D. Quality Control and Testing
Quality control is a critical aspect of chip resistor manufacturing. Various testing methods are employed, including:
1. **Electrical Testing**: Resistors are tested for their resistance values and tolerance levels.
2. **Environmental Testing**: Resistors undergo tests to assess their performance under different environmental conditions, such as temperature and humidity.
3. **Reliability Testing**: Long-term reliability tests are conducted to ensure that the resistors will perform consistently over time.
V. Innovations in Chip Resistor Manufacturing
The chip resistor manufacturing industry has seen significant innovations in recent years:
A. Advances in Materials Science
New materials are being developed to enhance the performance of chip resistors. For example, researchers are exploring nanomaterials and composites that offer improved conductivity and stability.
B. Automation and Industry 4.0
The integration of automation and Industry 4.0 technologies is revolutionizing the manufacturing process. Smart factories equipped with IoT devices and AI-driven analytics enable real-time monitoring and optimization of production processes.
C. Miniaturization and Integration
As electronic devices become smaller and more complex, the demand for miniaturized chip resistors has increased. Manufacturers are developing integrated solutions that combine resistors with other components, reducing space and improving performance.
D. Environmental Considerations and Sustainability
Sustainability is becoming a key focus in chip resistor manufacturing. Companies are exploring eco-friendly materials and processes to minimize their environmental impact, including the use of recyclable materials and energy-efficient manufacturing techniques.
VI. Challenges in Chip Resistor Manufacturing
Despite the advancements in technology, the chip resistor manufacturing industry faces several challenges:
A. Supply Chain Issues
Global supply chain disruptions have impacted the availability of raw materials and components, leading to delays and increased costs for manufacturers.
B. Cost Management
As the demand for high-performance resistors grows, manufacturers must find ways to manage costs while maintaining quality and performance.
C. Meeting Increasing Demand
The rapid growth of the electronics market has led to an increased demand for chip resistors, putting pressure on manufacturers to scale production while ensuring reliability and performance.
VII. Future Trends in Chip Resistor Manufacturing
Looking ahead, several trends are expected to shape the future of chip resistor manufacturing:
A. Emerging Technologies
The rise of flexible electronics and wearable devices is driving the development of new types of chip resistors that can conform to various shapes and sizes.
B. Potential Impact of AI and Machine Learning
AI and machine learning technologies are poised to enhance manufacturing processes, enabling predictive maintenance, quality control, and process optimization.
C. Predictions for Market Growth
The chip resistor market is expected to continue growing, driven by advancements in technology and increasing demand for electronic devices across various industries.
VIII. Conclusion
Chip resistors play a vital role in the functionality of modern electronic devices, and their manufacturing processes have evolved significantly to meet the demands of the industry. From the types of resistors available to the raw materials and innovative manufacturing techniques, the landscape of chip resistor production is dynamic and continually advancing. As we look to the future, the integration of new technologies and a focus on sustainability will likely shape the next generation of chip resistors, ensuring their continued relevance in an ever-evolving electronic world.
IX. References
- Academic journals on materials science and electronics.
- Industry reports from market research firms.
- Manufacturer specifications and white papers on chip resistor technology.
This comprehensive overview of chip resistor manufacturing processes highlights the importance of these components in modern electronics and the innovations driving their production. As technology continues to advance, chip resistors will remain a cornerstone of electronic design and functionality.