What is the Mainstream Cement Resistor Production Process?
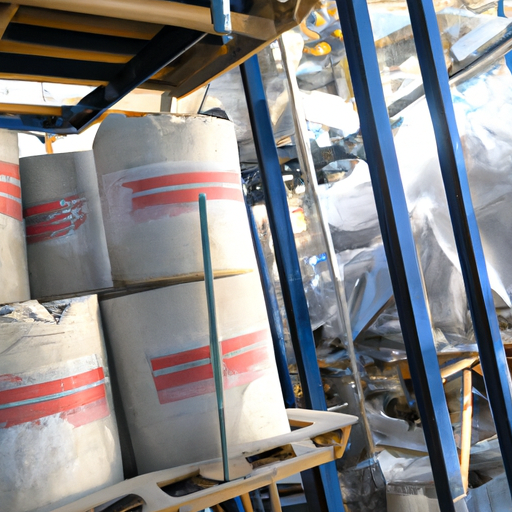
I. Introduction
Cement resistors are essential components in electrical engineering, widely used in various applications, including power electronics, automotive systems, and consumer electronics. These resistors are known for their durability, high power handling capabilities, and ability to withstand harsh environmental conditions. Understanding the production process of cement resistors is crucial for engineers and manufacturers alike, as it ensures the quality and reliability of these components. This blog post will delve into the mainstream cement resistor production process, exploring each stage from raw materials to distribution.
II. Raw Materials
A. Types of Materials Used
The production of cement resistors begins with the careful selection of raw materials. The primary components include:
1. **Cement**: The main binding agent, typically Portland cement, provides structural integrity and thermal stability.
2. **Carbon Black**: This material is crucial for imparting resistive properties to the cement. It enhances conductivity and helps achieve the desired resistance values.
3. **Metal Oxides**: Various metal oxides, such as manganese oxide and iron oxide, are added to modify the electrical and thermal properties of the resistors.
4. **Other Additives**: Additional materials, such as silica and alumina, may be included to improve performance characteristics like temperature stability and mechanical strength.
B. Quality Control of Raw Materials
Quality control is vital in the production of cement resistors. Each raw material undergoes rigorous testing to ensure it meets specific standards. This includes checking for purity, particle size, and consistency, which are critical for achieving uniformity in the final product.
C. Sourcing and Sustainability Considerations
Sourcing raw materials responsibly is increasingly important in today’s manufacturing landscape. Many companies are adopting sustainable practices, such as using recycled materials and ensuring that their suppliers adhere to environmental regulations. This not only helps reduce the ecological footprint but also enhances the brand's reputation.
III. Design and Specifications
A. Determining Resistance Values
The design phase involves calculating the desired resistance values based on the intended application. Engineers use Ohm's law and other electrical principles to determine the appropriate specifications.
B. Power Ratings and Tolerance Levels
Power ratings indicate how much power a resistor can handle without failing. Tolerance levels define the acceptable range of resistance values, which is crucial for ensuring that the resistor performs reliably in its application.
C. Environmental Considerations
Factors such as temperature and humidity can significantly affect resistor performance. Engineers must consider these environmental conditions during the design phase to ensure that the resistors can operate effectively in various settings.
D. Compliance with Industry Standards
Compliance with industry standards, such as those set by the International Electrotechnical Commission (IEC) and the American National Standards Institute (ANSI), is essential. These standards ensure that the resistors meet safety and performance requirements.
IV. Mixing Process
A. Proportioning of Raw Materials
Once the design specifications are established, the next step is to proportion the raw materials accurately. This is critical for achieving the desired electrical and mechanical properties.
B. Mixing Techniques
The mixing process can be conducted using two primary techniques:
1. **Dry Mixing**: In this method, the dry components are blended together to achieve a uniform mixture. This technique is often used for materials that do not require moisture.
2. **Wet Mixing**: This involves adding a liquid binder to the dry materials, creating a slurry that can be molded more easily. Wet mixing is beneficial for achieving a homogenous mixture.
C. Achieving Homogeneity
Achieving a homogeneous mixture is crucial for the performance of cement resistors. Inconsistent mixtures can lead to variations in resistance and other properties, affecting the overall quality of the final product.
V. Molding and Shaping
A. Types of Molds Used
The mixed material is then placed into molds to shape the resistors. Various types of molds can be used, including metal and silicone molds, depending on the desired shape and size of the resistor.
B. Molding Techniques
1. **Manual vs. Automated Molding**: Manual molding allows for greater flexibility and customization, while automated molding increases production efficiency and consistency.
2. **Compression Molding**: This technique involves applying pressure to the mixture in the mold, ensuring that it takes the desired shape and density.
C. Curing Process
1. Importance of Curing
Curing is a critical step in the production process, as it allows the cement to harden and develop its strength. Proper curing ensures that the resistors can withstand mechanical stress and thermal cycling.
2. Curing Conditions
Curing conditions, such as temperature and humidity, must be carefully controlled to achieve optimal results. Typically, a controlled environment is maintained to ensure uniform curing across all resistors.
VI. Firing and Sintering
A. Purpose of Firing
Firing is the process of heating the molded resistors to a specific temperature to enhance their electrical and mechanical properties. This step is essential for achieving the desired resistive characteristics.
B. Temperature Control
Temperature control during firing is critical. Too high a temperature can lead to degradation of the materials, while too low a temperature may not achieve the necessary sintering.
C. Duration of Firing
The duration of the firing process varies depending on the materials used and the desired properties. Typically, firing can last from several hours to a full day.
D. Effects on Material Properties
Firing alters the microstructure of the materials, improving their electrical conductivity and mechanical strength. This transformation is crucial for the performance of the final product.
VII. Finishing Processes
A. Trimming and Cutting
After firing, the resistors are trimmed and cut to the specified dimensions. This step ensures that the resistors fit properly in their intended applications.
B. Surface Treatment
1. Coating
Surface coatings may be applied to enhance the resistors' durability and resistance to environmental factors. Coatings can also improve aesthetics.
2. Painting
Painting is another finishing option that can provide additional protection and branding opportunities for manufacturers.
C. Quality Assurance Checks
Quality assurance checks are conducted throughout the finishing process to ensure that the resistors meet the required specifications. This includes visual inspections and measurements.
VIII. Testing and Quality Control
A. Electrical Testing
1. Resistance Measurement
Electrical testing begins with measuring the resistance of each resistor to ensure it falls within the specified tolerance levels.
2. Power Rating Tests
Power rating tests are conducted to verify that the resistors can handle the specified power levels without failure.
B. Mechanical Testing
1. Durability Tests
Mechanical testing includes durability tests to assess the resistors' ability to withstand physical stress and environmental conditions.
2. Environmental Resistance Tests
Environmental resistance tests evaluate how well the resistors perform under various temperature and humidity conditions.
C. Certification and Compliance
Once testing is complete, resistors are certified for compliance with industry standards. This certification is crucial for ensuring that the products are safe and reliable.
IX. Packaging and Distribution
A. Packaging Materials and Techniques
Proper packaging is essential to protect the resistors during transportation and storage. Manufacturers often use anti-static materials and cushioning to prevent damage.
B. Logistics and Supply Chain Considerations
Efficient logistics and supply chain management are critical for timely delivery to customers. Manufacturers must coordinate with suppliers and distributors to ensure a smooth process.
C. Market Trends and Demand
Understanding market trends and demand is vital for manufacturers to remain competitive. This includes keeping an eye on emerging technologies and customer preferences.
X. Conclusion
In summary, the production process of cement resistors involves several critical stages, from raw material selection to testing and distribution. Each step plays a vital role in ensuring the quality and reliability of the final product. As technology advances, the cement resistor manufacturing industry is likely to see innovations that improve efficiency and performance. Continuous improvement and innovation will be essential for manufacturers to meet the evolving demands of the market and maintain their competitive edge.
XI. References
A. Academic Journals
- Journal of Electrical Engineering
- Materials Science and Engineering Reports
B. Industry Reports
- Global Resistor Market Analysis
- Trends in Electronic Component Manufacturing
C. Standards Organizations
- International Electrotechnical Commission (IEC)
- American National Standards Institute (ANSI)
This comprehensive overview of the mainstream cement resistor production process highlights the complexity and precision required in manufacturing these essential components. By understanding each stage, manufacturers can ensure they produce high-quality resistors that meet the demands of modern electrical engineering applications.
What is the Mainstream Cement Resistor Production Process?
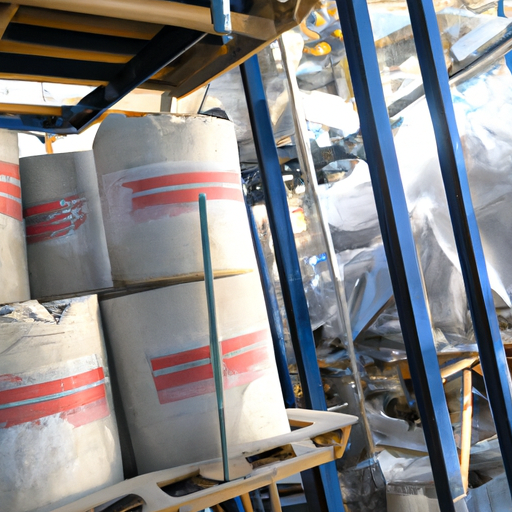
I. Introduction
Cement resistors are essential components in electrical engineering, widely used in various applications, including power electronics, automotive systems, and consumer electronics. These resistors are known for their durability, high power handling capabilities, and ability to withstand harsh environmental conditions. Understanding the production process of cement resistors is crucial for engineers and manufacturers alike, as it ensures the quality and reliability of these components. This blog post will delve into the mainstream cement resistor production process, exploring each stage from raw materials to distribution.
II. Raw Materials
A. Types of Materials Used
The production of cement resistors begins with the careful selection of raw materials. The primary components include:
1. **Cement**: The main binding agent, typically Portland cement, provides structural integrity and thermal stability.
2. **Carbon Black**: This material is crucial for imparting resistive properties to the cement. It enhances conductivity and helps achieve the desired resistance values.
3. **Metal Oxides**: Various metal oxides, such as manganese oxide and iron oxide, are added to modify the electrical and thermal properties of the resistors.
4. **Other Additives**: Additional materials, such as silica and alumina, may be included to improve performance characteristics like temperature stability and mechanical strength.
B. Quality Control of Raw Materials
Quality control is vital in the production of cement resistors. Each raw material undergoes rigorous testing to ensure it meets specific standards. This includes checking for purity, particle size, and consistency, which are critical for achieving uniformity in the final product.
C. Sourcing and Sustainability Considerations
Sourcing raw materials responsibly is increasingly important in today’s manufacturing landscape. Many companies are adopting sustainable practices, such as using recycled materials and ensuring that their suppliers adhere to environmental regulations. This not only helps reduce the ecological footprint but also enhances the brand's reputation.
III. Design and Specifications
A. Determining Resistance Values
The design phase involves calculating the desired resistance values based on the intended application. Engineers use Ohm's law and other electrical principles to determine the appropriate specifications.
B. Power Ratings and Tolerance Levels
Power ratings indicate how much power a resistor can handle without failing. Tolerance levels define the acceptable range of resistance values, which is crucial for ensuring that the resistor performs reliably in its application.
C. Environmental Considerations
Factors such as temperature and humidity can significantly affect resistor performance. Engineers must consider these environmental conditions during the design phase to ensure that the resistors can operate effectively in various settings.
D. Compliance with Industry Standards
Compliance with industry standards, such as those set by the International Electrotechnical Commission (IEC) and the American National Standards Institute (ANSI), is essential. These standards ensure that the resistors meet safety and performance requirements.
IV. Mixing Process
A. Proportioning of Raw Materials
Once the design specifications are established, the next step is to proportion the raw materials accurately. This is critical for achieving the desired electrical and mechanical properties.
B. Mixing Techniques
The mixing process can be conducted using two primary techniques:
1. **Dry Mixing**: In this method, the dry components are blended together to achieve a uniform mixture. This technique is often used for materials that do not require moisture.
2. **Wet Mixing**: This involves adding a liquid binder to the dry materials, creating a slurry that can be molded more easily. Wet mixing is beneficial for achieving a homogenous mixture.
C. Achieving Homogeneity
Achieving a homogeneous mixture is crucial for the performance of cement resistors. Inconsistent mixtures can lead to variations in resistance and other properties, affecting the overall quality of the final product.
V. Molding and Shaping
A. Types of Molds Used
The mixed material is then placed into molds to shape the resistors. Various types of molds can be used, including metal and silicone molds, depending on the desired shape and size of the resistor.
B. Molding Techniques
1. **Manual vs. Automated Molding**: Manual molding allows for greater flexibility and customization, while automated molding increases production efficiency and consistency.
2. **Compression Molding**: This technique involves applying pressure to the mixture in the mold, ensuring that it takes the desired shape and density.
C. Curing Process
1. Importance of Curing
Curing is a critical step in the production process, as it allows the cement to harden and develop its strength. Proper curing ensures that the resistors can withstand mechanical stress and thermal cycling.
2. Curing Conditions
Curing conditions, such as temperature and humidity, must be carefully controlled to achieve optimal results. Typically, a controlled environment is maintained to ensure uniform curing across all resistors.
VI. Firing and Sintering
A. Purpose of Firing
Firing is the process of heating the molded resistors to a specific temperature to enhance their electrical and mechanical properties. This step is essential for achieving the desired resistive characteristics.
B. Temperature Control
Temperature control during firing is critical. Too high a temperature can lead to degradation of the materials, while too low a temperature may not achieve the necessary sintering.
C. Duration of Firing
The duration of the firing process varies depending on the materials used and the desired properties. Typically, firing can last from several hours to a full day.
D. Effects on Material Properties
Firing alters the microstructure of the materials, improving their electrical conductivity and mechanical strength. This transformation is crucial for the performance of the final product.
VII. Finishing Processes
A. Trimming and Cutting
After firing, the resistors are trimmed and cut to the specified dimensions. This step ensures that the resistors fit properly in their intended applications.
B. Surface Treatment
1. Coating
Surface coatings may be applied to enhance the resistors' durability and resistance to environmental factors. Coatings can also improve aesthetics.
2. Painting
Painting is another finishing option that can provide additional protection and branding opportunities for manufacturers.
C. Quality Assurance Checks
Quality assurance checks are conducted throughout the finishing process to ensure that the resistors meet the required specifications. This includes visual inspections and measurements.
VIII. Testing and Quality Control
A. Electrical Testing
1. Resistance Measurement
Electrical testing begins with measuring the resistance of each resistor to ensure it falls within the specified tolerance levels.
2. Power Rating Tests
Power rating tests are conducted to verify that the resistors can handle the specified power levels without failure.
B. Mechanical Testing
1. Durability Tests
Mechanical testing includes durability tests to assess the resistors' ability to withstand physical stress and environmental conditions.
2. Environmental Resistance Tests
Environmental resistance tests evaluate how well the resistors perform under various temperature and humidity conditions.
C. Certification and Compliance
Once testing is complete, resistors are certified for compliance with industry standards. This certification is crucial for ensuring that the products are safe and reliable.
IX. Packaging and Distribution
A. Packaging Materials and Techniques
Proper packaging is essential to protect the resistors during transportation and storage. Manufacturers often use anti-static materials and cushioning to prevent damage.
B. Logistics and Supply Chain Considerations
Efficient logistics and supply chain management are critical for timely delivery to customers. Manufacturers must coordinate with suppliers and distributors to ensure a smooth process.
C. Market Trends and Demand
Understanding market trends and demand is vital for manufacturers to remain competitive. This includes keeping an eye on emerging technologies and customer preferences.
X. Conclusion
In summary, the production process of cement resistors involves several critical stages, from raw material selection to testing and distribution. Each step plays a vital role in ensuring the quality and reliability of the final product. As technology advances, the cement resistor manufacturing industry is likely to see innovations that improve efficiency and performance. Continuous improvement and innovation will be essential for manufacturers to meet the evolving demands of the market and maintain their competitive edge.
XI. References
A. Academic Journals
- Journal of Electrical Engineering
- Materials Science and Engineering Reports
B. Industry Reports
- Global Resistor Market Analysis
- Trends in Electronic Component Manufacturing
C. Standards Organizations
- International Electrotechnical Commission (IEC)
- American National Standards Institute (ANSI)
This comprehensive overview of the mainstream cement resistor production process highlights the complexity and precision required in manufacturing these essential components. By understanding each stage, manufacturers can ensure they produce high-quality resistors that meet the demands of modern electrical engineering applications.