Common Production Processes for Lifting Resistors
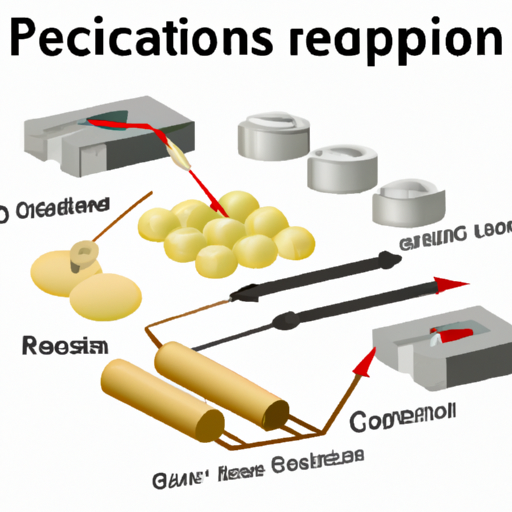
I. Introduction
Lifting resistors are essential components in various electrical applications, serving to manage voltage levels and protect sensitive equipment from overcurrent conditions. These resistors are designed to "lift" or elevate the voltage in a circuit, ensuring that devices operate within their specified parameters. The production of lifting resistors involves a series of intricate processes that transform raw materials into reliable components. This blog post will explore the common production processes for lifting resistors, detailing the types of resistors, raw materials used, manufacturing techniques, and innovations in the field.
II. Types of Lifting Resistors
Lifting resistors come in several types, each with unique characteristics and applications:
A. Wirewound Resistors
Wirewound resistors are made by winding a resistive wire around a core. They are known for their high precision and ability to handle high power levels, making them suitable for applications in power electronics and industrial equipment.
B. Thick Film Resistors
Thick film resistors are created by applying a thick layer of resistive material onto a substrate. This type of resistor is widely used in surface-mount technology (SMT) due to its compact size and cost-effectiveness.
C. Thin Film Resistors
Thin film resistors are produced by depositing a very thin layer of resistive material onto a substrate. They offer high accuracy and stability, making them ideal for precision applications in instrumentation and telecommunications.
D. Carbon Composition Resistors
Carbon composition resistors are made from a mixture of carbon particles and a binding agent. They are known for their high energy absorption capabilities and are often used in applications where high pulse loads are expected.
III. Raw Materials Used in Production
The production of lifting resistors requires a variety of raw materials, which can be categorized into conductive and insulating materials.
A. Conductive Materials
1. **Metals**: Common metals used in wirewound resistors include nickel and copper, which provide excellent conductivity and thermal stability.
2. **Carbon-based Materials**: Carbon is a key component in carbon composition resistors, offering a balance between conductivity and resistance.
B. Insulating Materials
1. **Ceramics**: Ceramics are often used as substrates for thick and thin film resistors due to their excellent insulating properties and thermal stability.
2. **Epoxy Resins**: Epoxy resins are used for encapsulating resistors, providing protection against environmental factors.
C. Substrates for Film Resistors
Substrates play a crucial role in the performance of film resistors. Common substrates include alumina and glass, which provide a stable base for the resistive layer.
IV. Common Production Processes
The production of lifting resistors involves several key processes, each critical to ensuring the quality and performance of the final product.
A. Design and Prototyping
The first step in the production process is design and prototyping. Engineers define the electrical specifications, such as resistance value, tolerance, and power rating. Mechanical design considerations, including size and shape, are also addressed to ensure compatibility with the intended application.
B. Material Preparation
Once the design is finalized, the next step is material preparation. This involves sourcing and conducting quality control on raw materials to ensure they meet the required standards. Pre-processing of materials, such as cutting and shaping, is also performed to prepare them for manufacturing.
C. Manufacturing Techniques
The manufacturing techniques vary depending on the type of lifting resistor being produced:
1. **Wirewound Resistor Production**
- **Winding Process**: A resistive wire is wound around a core, typically made of ceramic or metal. The number of turns and the wire gauge determine the resistance value.
- **Resistance Value Adjustment**: After winding, the resistor may undergo trimming to achieve the desired resistance value.
2. **Thick Film Resistor Production**
- **Screen Printing Technique**: A paste made of conductive material is screen-printed onto a substrate. The thickness of the printed layer influences the resistance.
- **Firing Process**: The printed substrate is then fired in a kiln to cure the paste, creating a solid resistive layer.
3. **Thin Film Resistor Production**
- **Vacuum Deposition**: A thin layer of resistive material is deposited onto a substrate using vacuum deposition techniques, ensuring uniform thickness.
- **Etching and Patterning**: The deposited layer is then etched to create the desired resistance pattern.
4. **Carbon Composition Resistor Production**
- **Mixing and Molding**: Carbon particles are mixed with a binding agent and molded into the desired shape.
- **Curing Process**: The molded resistors are cured to harden the material and enhance durability.
D. Assembly and Packaging
After manufacturing, the resistors undergo assembly and packaging. This includes the integration of components, such as terminals and leads, and encapsulation with protective coatings to shield against moisture and mechanical damage.
E. Quality Control and Testing
Quality control is a critical aspect of lifting resistor production. Various tests are conducted to ensure the resistors meet electrical and environmental standards:
1. **Electrical Testing**: Each resistor is tested for resistance value, tolerance, and power rating to ensure it meets specifications.
2. **Environmental Testing**: Resistors are subjected to temperature and humidity tests to assess their performance under different conditions.
3. **Reliability Assessments**: Long-term reliability tests are conducted to evaluate the lifespan and durability of the resistors.
V. Innovations in Lifting Resistor Production
The production of lifting resistors is continually evolving, driven by advancements in materials science and manufacturing technologies.
A. Advances in Materials Science
New materials are being developed to enhance the performance of lifting resistors. For example, the use of nanomaterials can improve conductivity and thermal stability, leading to more efficient resistors.
B. Automation and Robotics in Manufacturing
Automation and robotics are increasingly being integrated into the manufacturing process, improving efficiency and precision. Automated systems can handle repetitive tasks, reducing the risk of human error and increasing production speed.
C. Sustainable Production Practices
Sustainability is becoming a key focus in resistor production. Manufacturers are exploring eco-friendly materials and processes to minimize waste and reduce environmental impact. This includes recycling materials and using energy-efficient manufacturing techniques.
VI. Conclusion
In summary, the production of lifting resistors involves a complex interplay of design, material selection, manufacturing techniques, and quality control. Each step is crucial to ensuring that the final product meets the high standards required for electrical applications. As technology continues to advance, the production processes for lifting resistors will likely evolve, incorporating new materials and innovative manufacturing practices. The significance of quality in lifting resistor manufacturing cannot be overstated, as it directly impacts the reliability and performance of electrical systems. Looking ahead, we can expect to see exciting trends in the production of lifting resistors, driven by the need for greater efficiency, sustainability, and performance in the ever-evolving world of electronics.
VII. References
1. Academic journals on electrical engineering and materials science.
2. Industry reports on resistor manufacturing trends and technologies.
3. Manufacturer guidelines and specifications for lifting resistors.
This comprehensive overview of the common production processes for lifting resistors highlights the importance of each stage in creating reliable and effective components for electrical applications.
Common Production Processes for Lifting Resistors
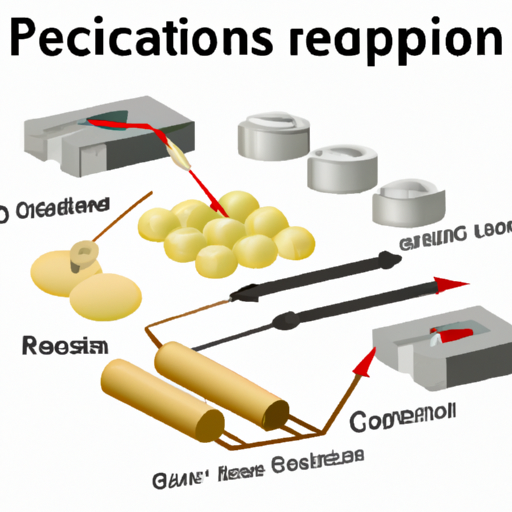
I. Introduction
Lifting resistors are essential components in various electrical applications, serving to manage voltage levels and protect sensitive equipment from overcurrent conditions. These resistors are designed to "lift" or elevate the voltage in a circuit, ensuring that devices operate within their specified parameters. The production of lifting resistors involves a series of intricate processes that transform raw materials into reliable components. This blog post will explore the common production processes for lifting resistors, detailing the types of resistors, raw materials used, manufacturing techniques, and innovations in the field.
II. Types of Lifting Resistors
Lifting resistors come in several types, each with unique characteristics and applications:
A. Wirewound Resistors
Wirewound resistors are made by winding a resistive wire around a core. They are known for their high precision and ability to handle high power levels, making them suitable for applications in power electronics and industrial equipment.
B. Thick Film Resistors
Thick film resistors are created by applying a thick layer of resistive material onto a substrate. This type of resistor is widely used in surface-mount technology (SMT) due to its compact size and cost-effectiveness.
C. Thin Film Resistors
Thin film resistors are produced by depositing a very thin layer of resistive material onto a substrate. They offer high accuracy and stability, making them ideal for precision applications in instrumentation and telecommunications.
D. Carbon Composition Resistors
Carbon composition resistors are made from a mixture of carbon particles and a binding agent. They are known for their high energy absorption capabilities and are often used in applications where high pulse loads are expected.
III. Raw Materials Used in Production
The production of lifting resistors requires a variety of raw materials, which can be categorized into conductive and insulating materials.
A. Conductive Materials
1. **Metals**: Common metals used in wirewound resistors include nickel and copper, which provide excellent conductivity and thermal stability.
2. **Carbon-based Materials**: Carbon is a key component in carbon composition resistors, offering a balance between conductivity and resistance.
B. Insulating Materials
1. **Ceramics**: Ceramics are often used as substrates for thick and thin film resistors due to their excellent insulating properties and thermal stability.
2. **Epoxy Resins**: Epoxy resins are used for encapsulating resistors, providing protection against environmental factors.
C. Substrates for Film Resistors
Substrates play a crucial role in the performance of film resistors. Common substrates include alumina and glass, which provide a stable base for the resistive layer.
IV. Common Production Processes
The production of lifting resistors involves several key processes, each critical to ensuring the quality and performance of the final product.
A. Design and Prototyping
The first step in the production process is design and prototyping. Engineers define the electrical specifications, such as resistance value, tolerance, and power rating. Mechanical design considerations, including size and shape, are also addressed to ensure compatibility with the intended application.
B. Material Preparation
Once the design is finalized, the next step is material preparation. This involves sourcing and conducting quality control on raw materials to ensure they meet the required standards. Pre-processing of materials, such as cutting and shaping, is also performed to prepare them for manufacturing.
C. Manufacturing Techniques
The manufacturing techniques vary depending on the type of lifting resistor being produced:
1. **Wirewound Resistor Production**
- **Winding Process**: A resistive wire is wound around a core, typically made of ceramic or metal. The number of turns and the wire gauge determine the resistance value.
- **Resistance Value Adjustment**: After winding, the resistor may undergo trimming to achieve the desired resistance value.
2. **Thick Film Resistor Production**
- **Screen Printing Technique**: A paste made of conductive material is screen-printed onto a substrate. The thickness of the printed layer influences the resistance.
- **Firing Process**: The printed substrate is then fired in a kiln to cure the paste, creating a solid resistive layer.
3. **Thin Film Resistor Production**
- **Vacuum Deposition**: A thin layer of resistive material is deposited onto a substrate using vacuum deposition techniques, ensuring uniform thickness.
- **Etching and Patterning**: The deposited layer is then etched to create the desired resistance pattern.
4. **Carbon Composition Resistor Production**
- **Mixing and Molding**: Carbon particles are mixed with a binding agent and molded into the desired shape.
- **Curing Process**: The molded resistors are cured to harden the material and enhance durability.
D. Assembly and Packaging
After manufacturing, the resistors undergo assembly and packaging. This includes the integration of components, such as terminals and leads, and encapsulation with protective coatings to shield against moisture and mechanical damage.
E. Quality Control and Testing
Quality control is a critical aspect of lifting resistor production. Various tests are conducted to ensure the resistors meet electrical and environmental standards:
1. **Electrical Testing**: Each resistor is tested for resistance value, tolerance, and power rating to ensure it meets specifications.
2. **Environmental Testing**: Resistors are subjected to temperature and humidity tests to assess their performance under different conditions.
3. **Reliability Assessments**: Long-term reliability tests are conducted to evaluate the lifespan and durability of the resistors.
V. Innovations in Lifting Resistor Production
The production of lifting resistors is continually evolving, driven by advancements in materials science and manufacturing technologies.
A. Advances in Materials Science
New materials are being developed to enhance the performance of lifting resistors. For example, the use of nanomaterials can improve conductivity and thermal stability, leading to more efficient resistors.
B. Automation and Robotics in Manufacturing
Automation and robotics are increasingly being integrated into the manufacturing process, improving efficiency and precision. Automated systems can handle repetitive tasks, reducing the risk of human error and increasing production speed.
C. Sustainable Production Practices
Sustainability is becoming a key focus in resistor production. Manufacturers are exploring eco-friendly materials and processes to minimize waste and reduce environmental impact. This includes recycling materials and using energy-efficient manufacturing techniques.
VI. Conclusion
In summary, the production of lifting resistors involves a complex interplay of design, material selection, manufacturing techniques, and quality control. Each step is crucial to ensuring that the final product meets the high standards required for electrical applications. As technology continues to advance, the production processes for lifting resistors will likely evolve, incorporating new materials and innovative manufacturing practices. The significance of quality in lifting resistor manufacturing cannot be overstated, as it directly impacts the reliability and performance of electrical systems. Looking ahead, we can expect to see exciting trends in the production of lifting resistors, driven by the need for greater efficiency, sustainability, and performance in the ever-evolving world of electronics.
VII. References
1. Academic journals on electrical engineering and materials science.
2. Industry reports on resistor manufacturing trends and technologies.
3. Manufacturer guidelines and specifications for lifting resistors.
This comprehensive overview of the common production processes for lifting resistors highlights the importance of each stage in creating reliable and effective components for electrical applications.