What are the Main Parameters and Manufacturing Processes of the Latest Resistors?
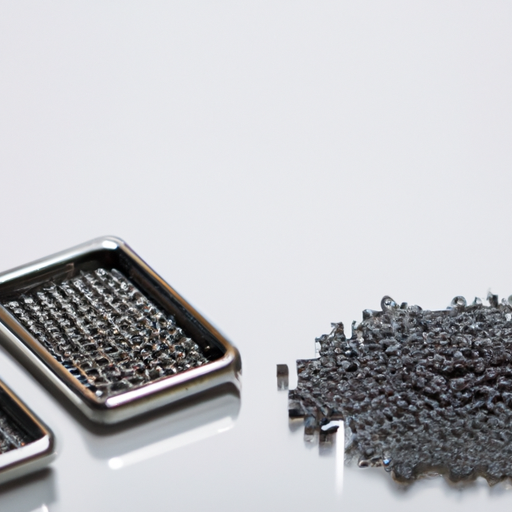
I. Introduction
Resistors are fundamental components in electronic circuits, serving the crucial role of controlling current flow. By providing resistance, they help to manage voltage levels, protect sensitive components, and ensure that circuits function as intended. Over the years, resistor technology has evolved significantly, driven by advancements in materials science, manufacturing processes, and the increasing demands of modern electronics. This blog post will explore the key parameters that define resistors, the various types available, and the manufacturing processes that bring these essential components to life.
II. Key Parameters of Resistors
Understanding the main parameters of resistors is essential for engineers and designers to select the right components for their applications. Here are the key parameters to consider:
A. Resistance Value
The resistance value of a resistor is measured in ohms (Ω) and indicates how much the resistor opposes the flow of electric current. This value is critical in determining how much current will flow through a circuit for a given voltage. Tolerance levels, expressed as a percentage, indicate how much the actual resistance can vary from the stated value. For example, a resistor with a tolerance of ±5% can have a resistance value that is 5% higher or lower than its nominal value. Understanding tolerance is vital for ensuring circuit reliability and performance.
B. Power Rating
Power rating refers to the maximum amount of power a resistor can dissipate without being damaged. It is typically measured in watts (W) and is crucial for circuit design. If a resistor dissipates more power than its rated capacity, it can overheat and fail. Therefore, engineers must consider the power rating when designing circuits to ensure that resistors can handle the expected load.
C. Temperature Coefficient
The temperature coefficient of a resistor indicates how its resistance changes with temperature. It is expressed in parts per million per degree Celsius (ppm/°C). A positive temperature coefficient means that resistance increases with temperature, while a negative coefficient indicates a decrease. This parameter is essential for applications where temperature fluctuations are expected, as it can significantly impact circuit performance.
D. Voltage Rating
The voltage rating of a resistor defines the maximum voltage that can be applied across it without risking breakdown or failure. Exceeding this voltage can lead to catastrophic failure, including short circuits or fires. Understanding voltage ratings is crucial for ensuring the safety and reliability of electronic devices.
E. Noise Characteristics
Noise in resistors refers to the unwanted electrical signals that can interfere with circuit performance. It is typically measured in microvolts (µV) and can affect sensitive applications, such as audio and precision measurement systems. Engineers must consider noise characteristics when selecting resistors for high-performance circuits.
F. Reliability and Lifespan
The reliability and lifespan of a resistor are influenced by various factors, including material quality, manufacturing processes, and environmental conditions. High-quality resistors are designed to withstand stress and have a longer lifespan, making them suitable for critical applications. Understanding these factors is essential for engineers to ensure that their designs are robust and reliable.
III. Types of Resistors
Resistors come in various types, each suited for specific applications. Here are the main categories:
A. Fixed Resistors
1. **Carbon Composition**: These resistors are made from a mixture of carbon and a binding material. They are known for their high energy absorption but have a relatively high noise level and lower precision.
2. **Metal Film**: Metal film resistors offer better precision and stability than carbon composition resistors. They are made by depositing a thin layer of metal onto a ceramic substrate, providing low noise and high reliability.
3. **Wirewound**: Wirewound resistors are constructed by winding a metal wire around a ceramic or fiberglass core. They can handle high power ratings and are often used in applications requiring high precision.
B. Variable Resistors
1. **Potentiometers**: These are adjustable resistors that allow users to change the resistance value manually. They are commonly used in volume controls and tuning circuits.
2. **Rheostats**: Similar to potentiometers, rheostats are used to adjust current flow in a circuit. They typically handle higher power levels and are often used in applications like dimmer switches.
C. Specialty Resistors
1. **Thin-Film and Thick-Film Resistors**: These resistors are manufactured using advanced techniques that allow for precise control over resistance values and characteristics. Thin-film resistors are known for their accuracy, while thick-film resistors are more robust and cost-effective.
2. **High-Precision Resistors**: These resistors are designed for applications requiring tight tolerance and stability, such as in measurement and calibration equipment.
3. **Current Sensing Resistors**: These resistors are specifically designed to measure current flow in a circuit. They are often used in power management applications and battery monitoring systems.
IV. Manufacturing Processes of Resistors
The manufacturing processes of resistors are critical in determining their performance and reliability. Here are the main steps involved:
A. Material Selection
The first step in resistor manufacturing is selecting the appropriate materials. Conductive materials, such as carbon or metal alloys, are chosen based on the desired resistance value and performance characteristics. Insulating materials are also selected to ensure that the resistor can handle the required voltage levels without breakdown.
B. Fabrication Techniques
1. **Thin-Film Technology**: This method involves depositing a thin layer of conductive material onto a substrate using techniques like sputtering or chemical vapor deposition (CVD). Thin-film resistors offer high precision and stability.
2. **Thick-Film Technology**: Thick-film resistors are made by screen printing a paste of conductive material onto a substrate and then firing it to create a solid resistor. This method is cost-effective and suitable for mass production.
3. **Wirewound Technology**: In this process, a metal wire is wound around a core to create the resistor. The wire is then insulated and coated to protect it from environmental factors. Wirewound resistors are known for their high power ratings and durability.
C. Quality Control Measures
Quality control is essential in resistor manufacturing to ensure that the final products meet industry standards. Testing for resistance values, environmental conditions (such as temperature and humidity), and reliability (including life cycle and stress testing) are all critical steps in the manufacturing process.
V. Innovations in Resistor Technology
The field of resistor technology is continually evolving, with several exciting innovations on the horizon:
A. Advances in Materials Science
Recent advancements in materials science have led to the development of new alloys and the use of nanomaterials in resistor manufacturing. These innovations can enhance performance, reduce size, and improve reliability.
B. Miniaturization and Integration
The trend toward miniaturization in electronics has led to the rise of surface mount technology (SMT) resistors, which are smaller and easier to integrate into compact devices. This integration allows for more efficient circuit designs and improved performance.
C. Smart Resistors
The emergence of smart resistors, which incorporate built-in sensors and connectivity features, is transforming the way resistors are used in applications like the Internet of Things (IoT) and smart devices. These resistors can provide real-time data and enhance the functionality of electronic systems.
VI. Conclusion
In summary, understanding the main parameters and manufacturing processes of resistors is crucial for engineers and designers working in the field of electronics. As technology continues to advance, the importance of selecting the right resistors for specific applications cannot be overstated. Future trends in resistor technology, including innovations in materials, miniaturization, and the development of smart resistors, will further enhance the capabilities of electronic devices. By staying informed about these developments, engineers can ensure that their designs are not only effective but also future-proof.
VII. References
For further exploration of resistor technology, consider the following resources:
1. "Electronic Components: A Complete Reference for Engineers and Technicians" by John Doe.
2. "Resistor Technology: Principles and Applications" by Jane Smith.
3. Industry standards and guidelines from organizations such as the Institute of Electrical and Electronics Engineers (IEEE) and the International Electrotechnical Commission (IEC).
By understanding the intricacies of resistors, engineers can make informed decisions that lead to more reliable and efficient electronic designs.
What are the Main Parameters and Manufacturing Processes of the Latest Resistors?
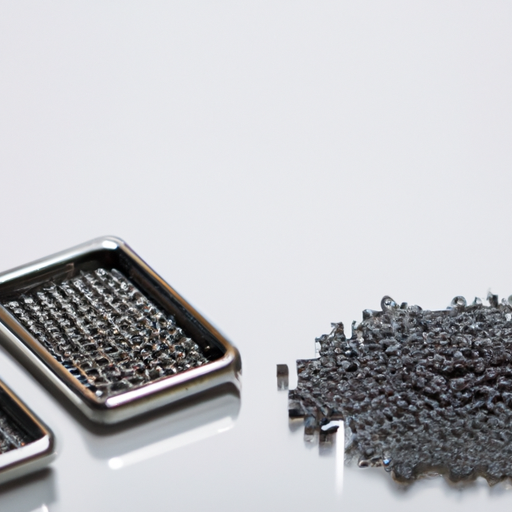
I. Introduction
Resistors are fundamental components in electronic circuits, serving the crucial role of controlling current flow. By providing resistance, they help to manage voltage levels, protect sensitive components, and ensure that circuits function as intended. Over the years, resistor technology has evolved significantly, driven by advancements in materials science, manufacturing processes, and the increasing demands of modern electronics. This blog post will explore the key parameters that define resistors, the various types available, and the manufacturing processes that bring these essential components to life.
II. Key Parameters of Resistors
Understanding the main parameters of resistors is essential for engineers and designers to select the right components for their applications. Here are the key parameters to consider:
A. Resistance Value
The resistance value of a resistor is measured in ohms (Ω) and indicates how much the resistor opposes the flow of electric current. This value is critical in determining how much current will flow through a circuit for a given voltage. Tolerance levels, expressed as a percentage, indicate how much the actual resistance can vary from the stated value. For example, a resistor with a tolerance of ±5% can have a resistance value that is 5% higher or lower than its nominal value. Understanding tolerance is vital for ensuring circuit reliability and performance.
B. Power Rating
Power rating refers to the maximum amount of power a resistor can dissipate without being damaged. It is typically measured in watts (W) and is crucial for circuit design. If a resistor dissipates more power than its rated capacity, it can overheat and fail. Therefore, engineers must consider the power rating when designing circuits to ensure that resistors can handle the expected load.
C. Temperature Coefficient
The temperature coefficient of a resistor indicates how its resistance changes with temperature. It is expressed in parts per million per degree Celsius (ppm/°C). A positive temperature coefficient means that resistance increases with temperature, while a negative coefficient indicates a decrease. This parameter is essential for applications where temperature fluctuations are expected, as it can significantly impact circuit performance.
D. Voltage Rating
The voltage rating of a resistor defines the maximum voltage that can be applied across it without risking breakdown or failure. Exceeding this voltage can lead to catastrophic failure, including short circuits or fires. Understanding voltage ratings is crucial for ensuring the safety and reliability of electronic devices.
E. Noise Characteristics
Noise in resistors refers to the unwanted electrical signals that can interfere with circuit performance. It is typically measured in microvolts (µV) and can affect sensitive applications, such as audio and precision measurement systems. Engineers must consider noise characteristics when selecting resistors for high-performance circuits.
F. Reliability and Lifespan
The reliability and lifespan of a resistor are influenced by various factors, including material quality, manufacturing processes, and environmental conditions. High-quality resistors are designed to withstand stress and have a longer lifespan, making them suitable for critical applications. Understanding these factors is essential for engineers to ensure that their designs are robust and reliable.
III. Types of Resistors
Resistors come in various types, each suited for specific applications. Here are the main categories:
A. Fixed Resistors
1. **Carbon Composition**: These resistors are made from a mixture of carbon and a binding material. They are known for their high energy absorption but have a relatively high noise level and lower precision.
2. **Metal Film**: Metal film resistors offer better precision and stability than carbon composition resistors. They are made by depositing a thin layer of metal onto a ceramic substrate, providing low noise and high reliability.
3. **Wirewound**: Wirewound resistors are constructed by winding a metal wire around a ceramic or fiberglass core. They can handle high power ratings and are often used in applications requiring high precision.
B. Variable Resistors
1. **Potentiometers**: These are adjustable resistors that allow users to change the resistance value manually. They are commonly used in volume controls and tuning circuits.
2. **Rheostats**: Similar to potentiometers, rheostats are used to adjust current flow in a circuit. They typically handle higher power levels and are often used in applications like dimmer switches.
C. Specialty Resistors
1. **Thin-Film and Thick-Film Resistors**: These resistors are manufactured using advanced techniques that allow for precise control over resistance values and characteristics. Thin-film resistors are known for their accuracy, while thick-film resistors are more robust and cost-effective.
2. **High-Precision Resistors**: These resistors are designed for applications requiring tight tolerance and stability, such as in measurement and calibration equipment.
3. **Current Sensing Resistors**: These resistors are specifically designed to measure current flow in a circuit. They are often used in power management applications and battery monitoring systems.
IV. Manufacturing Processes of Resistors
The manufacturing processes of resistors are critical in determining their performance and reliability. Here are the main steps involved:
A. Material Selection
The first step in resistor manufacturing is selecting the appropriate materials. Conductive materials, such as carbon or metal alloys, are chosen based on the desired resistance value and performance characteristics. Insulating materials are also selected to ensure that the resistor can handle the required voltage levels without breakdown.
B. Fabrication Techniques
1. **Thin-Film Technology**: This method involves depositing a thin layer of conductive material onto a substrate using techniques like sputtering or chemical vapor deposition (CVD). Thin-film resistors offer high precision and stability.
2. **Thick-Film Technology**: Thick-film resistors are made by screen printing a paste of conductive material onto a substrate and then firing it to create a solid resistor. This method is cost-effective and suitable for mass production.
3. **Wirewound Technology**: In this process, a metal wire is wound around a core to create the resistor. The wire is then insulated and coated to protect it from environmental factors. Wirewound resistors are known for their high power ratings and durability.
C. Quality Control Measures
Quality control is essential in resistor manufacturing to ensure that the final products meet industry standards. Testing for resistance values, environmental conditions (such as temperature and humidity), and reliability (including life cycle and stress testing) are all critical steps in the manufacturing process.
V. Innovations in Resistor Technology
The field of resistor technology is continually evolving, with several exciting innovations on the horizon:
A. Advances in Materials Science
Recent advancements in materials science have led to the development of new alloys and the use of nanomaterials in resistor manufacturing. These innovations can enhance performance, reduce size, and improve reliability.
B. Miniaturization and Integration
The trend toward miniaturization in electronics has led to the rise of surface mount technology (SMT) resistors, which are smaller and easier to integrate into compact devices. This integration allows for more efficient circuit designs and improved performance.
C. Smart Resistors
The emergence of smart resistors, which incorporate built-in sensors and connectivity features, is transforming the way resistors are used in applications like the Internet of Things (IoT) and smart devices. These resistors can provide real-time data and enhance the functionality of electronic systems.
VI. Conclusion
In summary, understanding the main parameters and manufacturing processes of resistors is crucial for engineers and designers working in the field of electronics. As technology continues to advance, the importance of selecting the right resistors for specific applications cannot be overstated. Future trends in resistor technology, including innovations in materials, miniaturization, and the development of smart resistors, will further enhance the capabilities of electronic devices. By staying informed about these developments, engineers can ensure that their designs are not only effective but also future-proof.
VII. References
For further exploration of resistor technology, consider the following resources:
1. "Electronic Components: A Complete Reference for Engineers and Technicians" by John Doe.
2. "Resistor Technology: Principles and Applications" by Jane Smith.
3. Industry standards and guidelines from organizations such as the Institute of Electrical and Electronics Engineers (IEEE) and the International Electrotechnical Commission (IEC).
By understanding the intricacies of resistors, engineers can make informed decisions that lead to more reliable and efficient electronic designs.