What is the Mainstream Resistor Packaging Production Process?
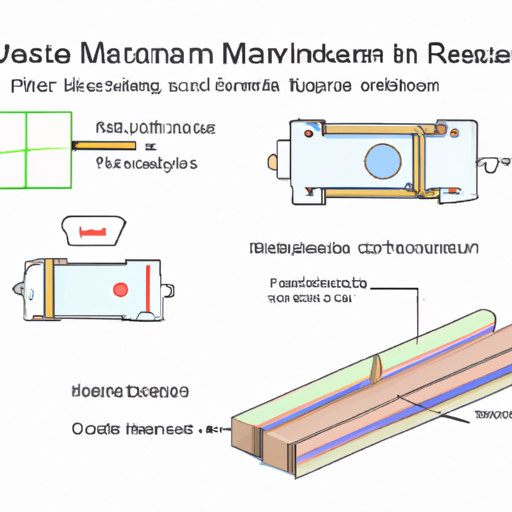
I. Introduction
Resistors are fundamental components in electronic circuits, serving the critical function of controlling current flow. They are essential for protecting sensitive components, dividing voltages, and setting bias points in various applications. The performance and reliability of resistors are significantly influenced by their packaging, which not only protects the internal components but also affects thermal management and electrical performance. This article aims to explore the mainstream resistor packaging production process, shedding light on the intricate steps involved in creating these vital electronic components.
II. Types of Resistors
Resistors come in various types, each suited for specific applications and performance requirements. The most common types include:
Carbon Film Resistors: Made by depositing a thin layer of carbon on a ceramic substrate, these resistors are known for their stability and low noise.
Metal Film Resistors: These resistors utilize a thin film of metal, offering higher precision and lower temperature coefficients compared to carbon film resistors.
Wirewound Resistors: Constructed by winding a metal wire around a ceramic core, wirewound resistors are capable of handling high power and are often used in high-frequency applications.
The choice of resistor type directly impacts the packaging requirements. For instance, wirewound resistors may require more robust packaging to handle their higher power ratings, while metal film resistors may prioritize precision and thermal management.
III. The Resistor Packaging Production Process
The production of resistors involves several key steps, each critical to ensuring the final product meets the required specifications.
A. Raw Material Selection
The first step in the resistor packaging production process is the selection of raw materials. The resistive elements can be made from various materials, including carbon, metal, or metal oxide, depending on the type of resistor being produced. Substrates, which provide the base for the resistive element, can be made from ceramics, plastics, or other materials.
Quality control measures are essential during this stage to ensure that the raw materials meet industry standards. This includes testing for purity, consistency, and performance characteristics.
B. Manufacturing the Resistor Element
Once the raw materials are selected, the next step is to manufacture the resistive element. This process varies depending on the type of resistor:
1. **Carbon Film Deposition**: In this method, a thin layer of carbon is deposited onto a ceramic substrate using a vacuum deposition process. The thickness of the film determines the resistance value.
2. **Metal Film Sputtering**: For metal film resistors, a metal layer is sputtered onto the substrate. This process allows for precise control over the thickness and resistance value.
3. **Wirewound Techniques**: Wirewound resistors are created by winding a metal wire around a ceramic core. The resistance is determined by the wire's length, diameter, and material.
After the resistive element is created, it undergoes rigorous testing and quality assurance to ensure it meets the required specifications for resistance, tolerance, and temperature coefficient.
C. Substrate Preparation
The substrate plays a crucial role in the performance of the resistor. Different types of substrates, such as ceramic or plastic, are chosen based on the application requirements. The substrate must undergo surface treatment and preparation processes to ensure proper adhesion of the resistive element and to enhance thermal conductivity.
D. Assembly of Resistor Components
Once the resistive element and substrate are prepared, the assembly process begins:
1. **Mounting the Resistive Element**: The resistive element is carefully mounted onto the substrate, ensuring proper alignment and contact.
2. **Soldering and Connecting Leads**: Leads are soldered to the resistive element to facilitate electrical connections. This step requires precision to avoid damaging the components.
3. **Encapsulation and Protective Coatings**: To protect the resistor from environmental factors such as moisture and dust, encapsulation is applied. This can involve coating the resistor with a protective layer or placing it in a housing.
E. Final Testing and Quality Control
The final stage of the production process involves comprehensive testing and quality control measures:
1. **Electrical Testing**: Resistors are tested for tolerance, temperature coefficient, and other electrical characteristics to ensure they meet specifications.
2. **Mechanical Testing**: Mechanical tests, such as vibration and thermal cycling, are conducted to assess the durability and reliability of the resistor under various conditions.
3. **Visual Inspection and Packaging**: A final visual inspection is performed to check for any defects before the resistors are packaged for shipment.
IV. Packaging Techniques
The packaging of resistors is crucial for their performance and reliability. There are two primary types of packaging:
Through-Hole Packaging: This traditional method involves inserting leads through holes in a printed circuit board (PCB). It is commonly used for larger resistors and provides robust mechanical support.
Surface Mount Packaging: This modern technique allows resistors to be mounted directly onto the surface of a PCB, enabling higher density and smaller designs. Surface mount resistors are often used in compact electronic devices.
Effective packaging is essential for thermal management, as it helps dissipate heat generated during operation. Innovations in packaging technology, such as the use of advanced materials and designs, continue to enhance the performance and reliability of resistors.
V. Environmental Considerations
The production of resistors, like many manufacturing processes, has an impact on the environment. Key considerations include:
Impact of Resistor Production: The extraction of raw materials and energy consumption during manufacturing can contribute to environmental degradation.
Sustainable Practices: Many manufacturers are adopting sustainable practices, such as using recycled materials, reducing waste, and implementing energy-efficient processes.
Compliance with Environmental Regulations: Adhering to environmental regulations is crucial for manufacturers to minimize their ecological footprint and ensure the safety of their products.
VI. Future Trends in Resistor Packaging
The resistor packaging industry is evolving, driven by advances in materials and technology. Key trends include:
Advances in Materials: New materials are being developed to enhance performance, such as high-temperature resistant substrates and conductive coatings.
Automation and Industry 4.0: The integration of automation and smart manufacturing technologies is streamlining production processes, improving efficiency, and reducing costs.
Predictions for the Future: As electronic devices continue to shrink in size and increase in complexity, the demand for innovative resistor packaging solutions will grow. Future developments may focus on miniaturization, enhanced thermal management, and improved reliability.
VII. Conclusion
The resistor packaging production process is a complex and multifaceted endeavor that plays a vital role in the performance and reliability of electronic circuits. From raw material selection to final testing, each step is critical to ensuring that resistors meet the stringent demands of modern electronics. As technology continues to advance, the importance of quality and innovation in resistor manufacturing will only increase, underscoring the significance of resistors in the ever-evolving landscape of electronic devices.
VIII. References
For further exploration of resistor technology and manufacturing processes, consider the following resources:
1. "Resistor Technology: A Comprehensive Guide" - A detailed overview of resistor types and applications.
2. "Advances in Electronic Component Packaging" - Insights into the latest trends in packaging technology.
3. "Sustainable Practices in Electronics Manufacturing" - An exploration of eco-friendly practices in the industry.
By understanding the intricacies of the resistor packaging production process, we can appreciate the essential role these components play in the functionality of electronic devices that shape our daily lives.
What is the Mainstream Resistor Packaging Production Process?
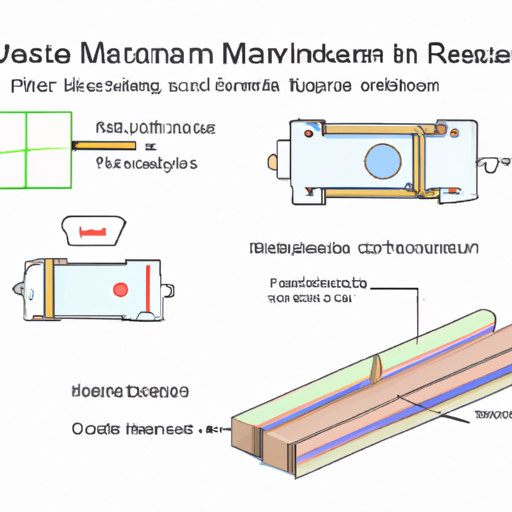
I. Introduction
Resistors are fundamental components in electronic circuits, serving the critical function of controlling current flow. They are essential for protecting sensitive components, dividing voltages, and setting bias points in various applications. The performance and reliability of resistors are significantly influenced by their packaging, which not only protects the internal components but also affects thermal management and electrical performance. This article aims to explore the mainstream resistor packaging production process, shedding light on the intricate steps involved in creating these vital electronic components.
II. Types of Resistors
Resistors come in various types, each suited for specific applications and performance requirements. The most common types include:
Carbon Film Resistors: Made by depositing a thin layer of carbon on a ceramic substrate, these resistors are known for their stability and low noise.
Metal Film Resistors: These resistors utilize a thin film of metal, offering higher precision and lower temperature coefficients compared to carbon film resistors.
Wirewound Resistors: Constructed by winding a metal wire around a ceramic core, wirewound resistors are capable of handling high power and are often used in high-frequency applications.
The choice of resistor type directly impacts the packaging requirements. For instance, wirewound resistors may require more robust packaging to handle their higher power ratings, while metal film resistors may prioritize precision and thermal management.
III. The Resistor Packaging Production Process
The production of resistors involves several key steps, each critical to ensuring the final product meets the required specifications.
A. Raw Material Selection
The first step in the resistor packaging production process is the selection of raw materials. The resistive elements can be made from various materials, including carbon, metal, or metal oxide, depending on the type of resistor being produced. Substrates, which provide the base for the resistive element, can be made from ceramics, plastics, or other materials.
Quality control measures are essential during this stage to ensure that the raw materials meet industry standards. This includes testing for purity, consistency, and performance characteristics.
B. Manufacturing the Resistor Element
Once the raw materials are selected, the next step is to manufacture the resistive element. This process varies depending on the type of resistor:
1. **Carbon Film Deposition**: In this method, a thin layer of carbon is deposited onto a ceramic substrate using a vacuum deposition process. The thickness of the film determines the resistance value.
2. **Metal Film Sputtering**: For metal film resistors, a metal layer is sputtered onto the substrate. This process allows for precise control over the thickness and resistance value.
3. **Wirewound Techniques**: Wirewound resistors are created by winding a metal wire around a ceramic core. The resistance is determined by the wire's length, diameter, and material.
After the resistive element is created, it undergoes rigorous testing and quality assurance to ensure it meets the required specifications for resistance, tolerance, and temperature coefficient.
C. Substrate Preparation
The substrate plays a crucial role in the performance of the resistor. Different types of substrates, such as ceramic or plastic, are chosen based on the application requirements. The substrate must undergo surface treatment and preparation processes to ensure proper adhesion of the resistive element and to enhance thermal conductivity.
D. Assembly of Resistor Components
Once the resistive element and substrate are prepared, the assembly process begins:
1. **Mounting the Resistive Element**: The resistive element is carefully mounted onto the substrate, ensuring proper alignment and contact.
2. **Soldering and Connecting Leads**: Leads are soldered to the resistive element to facilitate electrical connections. This step requires precision to avoid damaging the components.
3. **Encapsulation and Protective Coatings**: To protect the resistor from environmental factors such as moisture and dust, encapsulation is applied. This can involve coating the resistor with a protective layer or placing it in a housing.
E. Final Testing and Quality Control
The final stage of the production process involves comprehensive testing and quality control measures:
1. **Electrical Testing**: Resistors are tested for tolerance, temperature coefficient, and other electrical characteristics to ensure they meet specifications.
2. **Mechanical Testing**: Mechanical tests, such as vibration and thermal cycling, are conducted to assess the durability and reliability of the resistor under various conditions.
3. **Visual Inspection and Packaging**: A final visual inspection is performed to check for any defects before the resistors are packaged for shipment.
IV. Packaging Techniques
The packaging of resistors is crucial for their performance and reliability. There are two primary types of packaging:
Through-Hole Packaging: This traditional method involves inserting leads through holes in a printed circuit board (PCB). It is commonly used for larger resistors and provides robust mechanical support.
Surface Mount Packaging: This modern technique allows resistors to be mounted directly onto the surface of a PCB, enabling higher density and smaller designs. Surface mount resistors are often used in compact electronic devices.
Effective packaging is essential for thermal management, as it helps dissipate heat generated during operation. Innovations in packaging technology, such as the use of advanced materials and designs, continue to enhance the performance and reliability of resistors.
V. Environmental Considerations
The production of resistors, like many manufacturing processes, has an impact on the environment. Key considerations include:
Impact of Resistor Production: The extraction of raw materials and energy consumption during manufacturing can contribute to environmental degradation.
Sustainable Practices: Many manufacturers are adopting sustainable practices, such as using recycled materials, reducing waste, and implementing energy-efficient processes.
Compliance with Environmental Regulations: Adhering to environmental regulations is crucial for manufacturers to minimize their ecological footprint and ensure the safety of their products.
VI. Future Trends in Resistor Packaging
The resistor packaging industry is evolving, driven by advances in materials and technology. Key trends include:
Advances in Materials: New materials are being developed to enhance performance, such as high-temperature resistant substrates and conductive coatings.
Automation and Industry 4.0: The integration of automation and smart manufacturing technologies is streamlining production processes, improving efficiency, and reducing costs.
Predictions for the Future: As electronic devices continue to shrink in size and increase in complexity, the demand for innovative resistor packaging solutions will grow. Future developments may focus on miniaturization, enhanced thermal management, and improved reliability.
VII. Conclusion
The resistor packaging production process is a complex and multifaceted endeavor that plays a vital role in the performance and reliability of electronic circuits. From raw material selection to final testing, each step is critical to ensuring that resistors meet the stringent demands of modern electronics. As technology continues to advance, the importance of quality and innovation in resistor manufacturing will only increase, underscoring the significance of resistors in the ever-evolving landscape of electronic devices.
VIII. References
For further exploration of resistor technology and manufacturing processes, consider the following resources:
1. "Resistor Technology: A Comprehensive Guide" - A detailed overview of resistor types and applications.
2. "Advances in Electronic Component Packaging" - Insights into the latest trends in packaging technology.
3. "Sustainable Practices in Electronics Manufacturing" - An exploration of eco-friendly practices in the industry.
By understanding the intricacies of the resistor packaging production process, we can appreciate the essential role these components play in the functionality of electronic devices that shape our daily lives.