The Production Process of Mainstream High-Voltage Capacitors
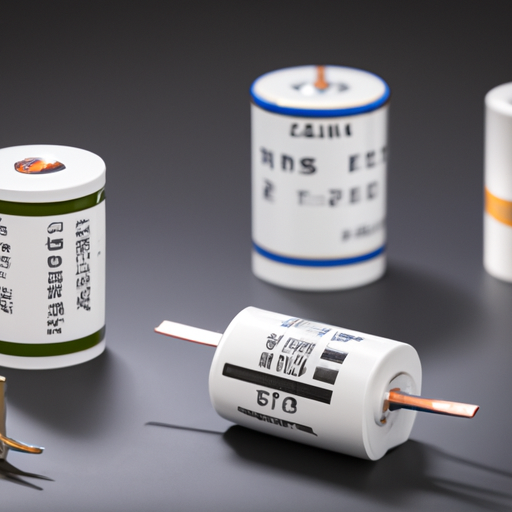
I. Introduction
High-voltage capacitors are essential components in various electrical and electronic systems, designed to store and release electrical energy efficiently. These capacitors are crucial in applications ranging from power transmission and distribution to renewable energy systems and industrial machinery. Understanding the production process of high-voltage capacitors is vital for appreciating their role in modern technology and ensuring their reliability and performance.
II. Types of High-Voltage Capacitors
High-voltage capacitors come in several types, each with unique characteristics and applications:
A. Ceramic Capacitors
Ceramic capacitors are widely used for their stability and reliability. They are made from ceramic materials that provide excellent dielectric properties, making them suitable for high-frequency applications.
B. Film Capacitors
Film capacitors utilize thin plastic films as dielectric materials. They are known for their low loss and high insulation resistance, making them ideal for power electronics and audio applications.
C. Electrolytic Capacitors
Electrolytic capacitors are polarized capacitors that use an electrolyte as one of their plates. They offer high capacitance values in a compact size, making them popular in power supply circuits.
D. Tantalum Capacitors
Tantalum capacitors are known for their high capacitance and voltage ratings in a small package. They are often used in military and aerospace applications due to their reliability.
E. Comparison of Different Types
Each type of high-voltage capacitor has its advantages and disadvantages, making them suitable for specific applications. For instance, while ceramic capacitors are excellent for high-frequency applications, electrolytic capacitors are preferred for bulk energy storage.
III. Raw Materials
The production of high-voltage capacitors begins with the selection of raw materials, which significantly influence the performance and reliability of the final product.
A. Overview of Materials Used in High-Voltage Capacitors
1. **Dielectric Materials**: The dielectric material is crucial for energy storage. Common materials include ceramic, polyester, polypropylene, and tantalum oxide.
2. **Conductive Materials**: Conductive materials, such as aluminum and copper, are used for the electrodes. The choice of material affects the capacitor's conductivity and overall performance.
3. **Packaging Materials**: The encapsulation and packaging materials protect the capacitor from environmental factors. Common materials include epoxy resins and plastics.
B. Sourcing and Quality Control of Raw Materials
Sourcing high-quality raw materials is essential for ensuring the reliability of high-voltage capacitors. Manufacturers often establish strict quality control measures to verify the purity and performance of materials before they enter the production process.
IV. Design and Engineering
The design and engineering phase is critical in determining the specifications and performance of high-voltage capacitors.
A. Initial Design Considerations
1. **Voltage Rating**: The voltage rating is a key parameter that defines the maximum voltage the capacitor can handle without failure.
2. **Capacitance Value**: The capacitance value determines how much charge the capacitor can store, influencing its application.
3. **Size and Form Factor**: The physical dimensions of the capacitor must align with the intended application, balancing performance with space constraints.
B. Simulation and Modeling
Advanced simulation and modeling techniques are employed to predict the performance of the capacitor under various conditions. This step helps identify potential issues before physical prototypes are created.
C. Prototyping and Testing
Once the design is finalized, prototypes are manufactured and subjected to rigorous testing to ensure they meet the specified performance criteria.
V. Manufacturing Process
The manufacturing process of high-voltage capacitors involves several key steps:
A. Dielectric Layer Production
1. **Material Preparation**: The dielectric materials are prepared through processes such as mixing, grinding, and drying to achieve the desired properties.
2. **Layer Formation Techniques**: Techniques such as casting, extrusion, or film deposition are used to create the dielectric layers.
B. Electrode Fabrication
1. **Material Selection**: The choice of conductive materials for the electrodes is critical for performance.
2. **Electrode Deposition Methods**: Methods such as sputtering, evaporation, or chemical deposition are employed to create the electrodes.
C. Assembly of Capacitor Components
1. **Layer Stacking**: The dielectric layers and electrodes are stacked in a specific order to form the capacitor structure.
2. **Connection of Electrodes**: The electrodes are connected to ensure proper electrical functionality.
D. Encapsulation and Packaging
1. **Protective Coatings**: A protective coating is applied to shield the capacitor from environmental factors.
2. **Final Assembly**: The final assembly involves encasing the capacitor in its packaging, ensuring durability and reliability.
VI. Quality Control and Testing
Quality control is paramount in the production of high-voltage capacitors to ensure they meet industry standards and customer expectations.
A. Importance of Quality Assurance in Capacitor Production
Quality assurance processes help identify defects and ensure that each capacitor performs reliably under specified conditions.
B. Testing Methods
1. **Electrical Testing**: Capacitors undergo electrical testing to verify their capacitance, voltage rating, and leakage current.
2. **Mechanical Testing**: Mechanical tests assess the physical integrity of the capacitors, including stress and strain tests.
3. **Environmental Testing**: Environmental tests evaluate the capacitor's performance under various temperature and humidity conditions.
C. Certification and Compliance with Industry Standards
Manufacturers must comply with industry standards, such as IEC and UL certifications, to ensure their products are safe and reliable.
VII. Challenges in Production
The production of high-voltage capacitors faces several challenges:
A. Material Sourcing and Supply Chain Issues
Global supply chain disruptions can impact the availability and cost of raw materials, affecting production schedules.
B. Technological Advancements and Their Impact
Rapid technological advancements require manufacturers to continuously innovate and adapt their production processes to remain competitive.
C. Environmental Considerations and Sustainability
Manufacturers are increasingly focusing on sustainable practices, including reducing waste and using eco-friendly materials.
VIII. Future Trends in High-Voltage Capacitor Production
The future of high-voltage capacitor production is shaped by several trends:
A. Innovations in Materials and Technology
Research into new dielectric materials and manufacturing techniques promises to enhance the performance and efficiency of high-voltage capacitors.
B. Market Demand and Growth Projections
As industries increasingly adopt renewable energy sources and electric vehicles, the demand for high-voltage capacitors is expected to grow significantly.
C. Potential Applications in Emerging Technologies
High-voltage capacitors will play a crucial role in emerging technologies, including energy storage systems, electric propulsion, and advanced power electronics.
IX. Conclusion
The production process of mainstream high-voltage capacitors is a complex and multifaceted endeavor that requires careful consideration of materials, design, and manufacturing techniques. As technology continues to evolve, the significance of high-voltage capacitors in modern applications will only increase. By understanding the intricacies of their production, we can appreciate the vital role these components play in powering our world and driving innovation in various industries. The future of capacitor manufacturing looks promising, with advancements in materials and technology paving the way for more efficient and reliable energy storage solutions.
The Production Process of Mainstream High-Voltage Capacitors
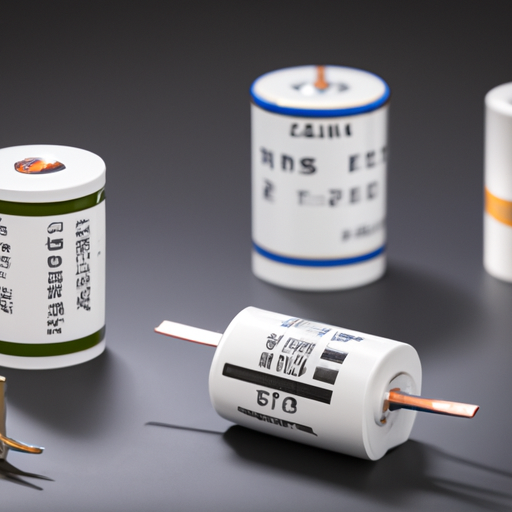
I. Introduction
High-voltage capacitors are essential components in various electrical and electronic systems, designed to store and release electrical energy efficiently. These capacitors are crucial in applications ranging from power transmission and distribution to renewable energy systems and industrial machinery. Understanding the production process of high-voltage capacitors is vital for appreciating their role in modern technology and ensuring their reliability and performance.
II. Types of High-Voltage Capacitors
High-voltage capacitors come in several types, each with unique characteristics and applications:
A. Ceramic Capacitors
Ceramic capacitors are widely used for their stability and reliability. They are made from ceramic materials that provide excellent dielectric properties, making them suitable for high-frequency applications.
B. Film Capacitors
Film capacitors utilize thin plastic films as dielectric materials. They are known for their low loss and high insulation resistance, making them ideal for power electronics and audio applications.
C. Electrolytic Capacitors
Electrolytic capacitors are polarized capacitors that use an electrolyte as one of their plates. They offer high capacitance values in a compact size, making them popular in power supply circuits.
D. Tantalum Capacitors
Tantalum capacitors are known for their high capacitance and voltage ratings in a small package. They are often used in military and aerospace applications due to their reliability.
E. Comparison of Different Types
Each type of high-voltage capacitor has its advantages and disadvantages, making them suitable for specific applications. For instance, while ceramic capacitors are excellent for high-frequency applications, electrolytic capacitors are preferred for bulk energy storage.
III. Raw Materials
The production of high-voltage capacitors begins with the selection of raw materials, which significantly influence the performance and reliability of the final product.
A. Overview of Materials Used in High-Voltage Capacitors
1. **Dielectric Materials**: The dielectric material is crucial for energy storage. Common materials include ceramic, polyester, polypropylene, and tantalum oxide.
2. **Conductive Materials**: Conductive materials, such as aluminum and copper, are used for the electrodes. The choice of material affects the capacitor's conductivity and overall performance.
3. **Packaging Materials**: The encapsulation and packaging materials protect the capacitor from environmental factors. Common materials include epoxy resins and plastics.
B. Sourcing and Quality Control of Raw Materials
Sourcing high-quality raw materials is essential for ensuring the reliability of high-voltage capacitors. Manufacturers often establish strict quality control measures to verify the purity and performance of materials before they enter the production process.
IV. Design and Engineering
The design and engineering phase is critical in determining the specifications and performance of high-voltage capacitors.
A. Initial Design Considerations
1. **Voltage Rating**: The voltage rating is a key parameter that defines the maximum voltage the capacitor can handle without failure.
2. **Capacitance Value**: The capacitance value determines how much charge the capacitor can store, influencing its application.
3. **Size and Form Factor**: The physical dimensions of the capacitor must align with the intended application, balancing performance with space constraints.
B. Simulation and Modeling
Advanced simulation and modeling techniques are employed to predict the performance of the capacitor under various conditions. This step helps identify potential issues before physical prototypes are created.
C. Prototyping and Testing
Once the design is finalized, prototypes are manufactured and subjected to rigorous testing to ensure they meet the specified performance criteria.
V. Manufacturing Process
The manufacturing process of high-voltage capacitors involves several key steps:
A. Dielectric Layer Production
1. **Material Preparation**: The dielectric materials are prepared through processes such as mixing, grinding, and drying to achieve the desired properties.
2. **Layer Formation Techniques**: Techniques such as casting, extrusion, or film deposition are used to create the dielectric layers.
B. Electrode Fabrication
1. **Material Selection**: The choice of conductive materials for the electrodes is critical for performance.
2. **Electrode Deposition Methods**: Methods such as sputtering, evaporation, or chemical deposition are employed to create the electrodes.
C. Assembly of Capacitor Components
1. **Layer Stacking**: The dielectric layers and electrodes are stacked in a specific order to form the capacitor structure.
2. **Connection of Electrodes**: The electrodes are connected to ensure proper electrical functionality.
D. Encapsulation and Packaging
1. **Protective Coatings**: A protective coating is applied to shield the capacitor from environmental factors.
2. **Final Assembly**: The final assembly involves encasing the capacitor in its packaging, ensuring durability and reliability.
VI. Quality Control and Testing
Quality control is paramount in the production of high-voltage capacitors to ensure they meet industry standards and customer expectations.
A. Importance of Quality Assurance in Capacitor Production
Quality assurance processes help identify defects and ensure that each capacitor performs reliably under specified conditions.
B. Testing Methods
1. **Electrical Testing**: Capacitors undergo electrical testing to verify their capacitance, voltage rating, and leakage current.
2. **Mechanical Testing**: Mechanical tests assess the physical integrity of the capacitors, including stress and strain tests.
3. **Environmental Testing**: Environmental tests evaluate the capacitor's performance under various temperature and humidity conditions.
C. Certification and Compliance with Industry Standards
Manufacturers must comply with industry standards, such as IEC and UL certifications, to ensure their products are safe and reliable.
VII. Challenges in Production
The production of high-voltage capacitors faces several challenges:
A. Material Sourcing and Supply Chain Issues
Global supply chain disruptions can impact the availability and cost of raw materials, affecting production schedules.
B. Technological Advancements and Their Impact
Rapid technological advancements require manufacturers to continuously innovate and adapt their production processes to remain competitive.
C. Environmental Considerations and Sustainability
Manufacturers are increasingly focusing on sustainable practices, including reducing waste and using eco-friendly materials.
VIII. Future Trends in High-Voltage Capacitor Production
The future of high-voltage capacitor production is shaped by several trends:
A. Innovations in Materials and Technology
Research into new dielectric materials and manufacturing techniques promises to enhance the performance and efficiency of high-voltage capacitors.
B. Market Demand and Growth Projections
As industries increasingly adopt renewable energy sources and electric vehicles, the demand for high-voltage capacitors is expected to grow significantly.
C. Potential Applications in Emerging Technologies
High-voltage capacitors will play a crucial role in emerging technologies, including energy storage systems, electric propulsion, and advanced power electronics.
IX. Conclusion
The production process of mainstream high-voltage capacitors is a complex and multifaceted endeavor that requires careful consideration of materials, design, and manufacturing techniques. As technology continues to evolve, the significance of high-voltage capacitors in modern applications will only increase. By understanding the intricacies of their production, we can appreciate the vital role these components play in powering our world and driving innovation in various industries. The future of capacitor manufacturing looks promising, with advancements in materials and technology paving the way for more efficient and reliable energy storage solutions.