Manufacturing Processes of the Latest Capacitor Principles
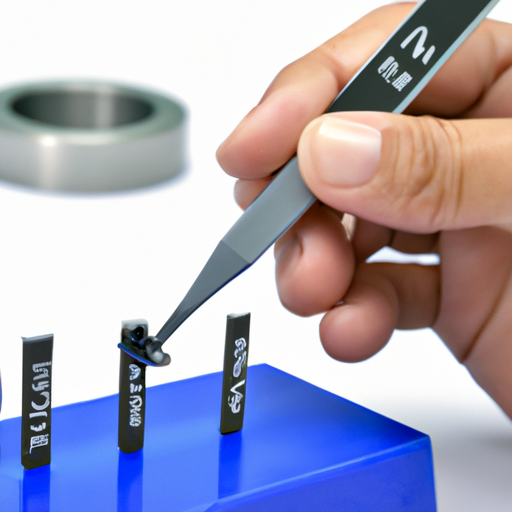
I. Introduction
Capacitors are fundamental components in modern electronics, serving as energy storage devices that can release energy quickly when needed. They play a crucial role in various applications, from power supply smoothing to signal coupling and decoupling in circuits. As technology advances, so do the principles and manufacturing processes behind capacitors, leading to improved performance, efficiency, and miniaturization. This blog post explores the latest capacitor principles, their types, manufacturing processes, innovations, challenges, and future trends.
II. Types of Capacitors
A. Electrolytic Capacitors
Electrolytic capacitors are polarized capacitors that use an electrolyte as one of their plates. They are known for their high capacitance values, making them ideal for applications requiring significant energy storage, such as power supply circuits and audio equipment. The construction typically involves an aluminum or tantalum foil as the anode, coated with a thin layer of oxide that acts as the dielectric, and a liquid or solid electrolyte as the cathode.
B. Ceramic Capacitors
Ceramic capacitors are non-polarized capacitors made from ceramic materials. They are categorized into Class 1 (temperature-stable) and Class 2 (high-capacitance) types. Class 1 capacitors are used in precision applications, while Class 2 capacitors are favored for their higher capacitance values in smaller sizes. Their applications range from decoupling in high-frequency circuits to timing applications in oscillators.
C. Film Capacitors
Film capacitors utilize thin plastic films as dielectrics. They are known for their stability, low self-inductance, and high insulation resistance. Common types include polyester, polypropylene, and polycarbonate capacitors. Film capacitors are widely used in audio equipment, power electronics, and applications requiring high reliability.
D. Supercapacitors
Supercapacitors, or ultracapacitors, are energy storage devices that bridge the gap between traditional capacitors and batteries. They offer high capacitance values and rapid charge/discharge capabilities. Supercapacitors are used in applications such as energy harvesting, backup power supplies, and electric vehicles, where quick bursts of energy are required.
E. Emerging Capacitor Technologies
Recent advancements have led to the development of solid-state capacitors and organic capacitors. Solid-state capacitors use solid electrolytes, offering improved safety and performance over traditional electrolytic capacitors. Organic capacitors, made from organic materials, promise to be lightweight and environmentally friendly, making them suitable for future applications.
III. Manufacturing Processes
A. Raw Material Selection
The manufacturing of capacitors begins with the selection of raw materials. The choice of dielectric materials is critical, as it directly affects the capacitor's performance. Common dielectric materials include ceramic, plastic films, and electrolytes. Conductive materials, such as aluminum, tantalum, and conductive polymers, are also essential for the capacitor's plates.
B. Fabrication Techniques
1. Thin-film Deposition
Thin-film deposition techniques, such as Physical Vapor Deposition (PVD) and Chemical Vapor Deposition (CVD), are widely used in capacitor manufacturing. PVD involves the physical transfer of material from a source to a substrate, creating thin films of dielectric or conductive materials. CVD, on the other hand, involves chemical reactions that deposit materials onto the substrate, allowing for precise control over film thickness and composition.
2. Screen Printing
Screen printing is a cost-effective method for producing capacitors, particularly for thick-film technologies. This technique involves applying conductive and dielectric inks onto substrates through a mesh screen, allowing for the creation of multilayer capacitors with complex geometries.
3. Stamping and Cutting
For certain types of capacitors, stamping and cutting techniques are employed to shape the conductive materials into the desired forms. This process is particularly common in the production of aluminum electrolytic capacitors, where foils are stamped into specific shapes before assembly.
C. Assembly Processes
The assembly of capacitors involves several steps, including layer stacking for multilayer capacitors and encapsulation techniques. In multilayer capacitors, layers of dielectric and conductive materials are stacked and pressed together to form a compact unit. Encapsulation techniques, such as potting or molding, protect the capacitor from environmental factors and enhance its durability.
D. Quality Control Measures
Quality control is paramount in capacitor manufacturing. Testing for capacitance and Equivalent Series Resistance (ESR) ensures that the capacitors meet performance specifications. Reliability testing under various conditions, such as temperature, humidity, and voltage stress, helps identify potential failures and ensures long-term performance.
IV. Innovations in Capacitor Manufacturing
A. Nanotechnology in Capacitors
Nanotechnology has revolutionized capacitor manufacturing by enabling the use of nanoscale materials that enhance performance. Nanoscale dielectrics can improve capacitance and reduce leakage currents, leading to smaller and more efficient capacitors. The impact of these innovations is significant, as they allow for the development of capacitors that can fit into increasingly compact electronic devices.
B. Sustainable Manufacturing Practices
As environmental concerns grow, the capacitor industry is adopting sustainable manufacturing practices. This includes the use of eco-friendly materials and energy-efficient production methods. Manufacturers are exploring biodegradable dielectrics and recyclable components to minimize their environmental footprint.
C. Automation and Industry 4.0
The integration of automation and Industry 4.0 technologies is transforming capacitor manufacturing. The use of AI and machine learning in production processes enhances efficiency and reduces waste. Smart manufacturing systems enable real-time monitoring and optimization of production lines, leading to higher quality and lower costs.
V. Challenges in Capacitor Manufacturing
Despite advancements, capacitor manufacturing faces several challenges. Material limitations can restrict the performance and miniaturization of capacitors. Cost considerations are also critical, as manufacturers strive to balance quality with affordability. Additionally, environmental regulations are becoming stricter, pushing manufacturers to adopt greener practices. Finally, competition and market dynamics require constant innovation to stay ahead in a rapidly evolving industry.
VI. Future Trends in Capacitor Technology
The future of capacitor technology is promising, with several trends emerging. Miniaturization and high-capacity designs are expected to continue, driven by the demand for smaller electronic devices. The integration of capacitors with renewable energy systems, such as solar and wind, will enhance energy storage solutions. The development of new materials, including graphene, holds the potential for capacitors with unprecedented performance characteristics. Furthermore, capacitors will play a crucial role in emerging technologies, such as electric vehicles and the Internet of Things (IoT), where efficient energy storage and management are essential.
VII. Conclusion
In summary, the manufacturing processes of the latest capacitor principles are evolving rapidly, driven by advancements in materials, fabrication techniques, and technology. Understanding the various types of capacitors, their manufacturing processes, and the innovations shaping the industry is essential for anyone involved in electronics. As research and development continue, the future outlook for capacitor manufacturing is bright, promising enhanced performance, sustainability, and integration with cutting-edge technologies.
VIII. References
1. Academic journals on capacitor technology and materials science.
2. Industry reports on capacitor market trends and innovations.
3. Books and articles discussing the principles and applications of capacitors in electronics.
This comprehensive overview of capacitor manufacturing processes highlights the significance of ongoing research and development in this critical field of electronics. As technology continues to advance, capacitors will remain integral to the performance and efficiency of electronic devices, paving the way for a more connected and energy-efficient future.
Manufacturing Processes of the Latest Capacitor Principles
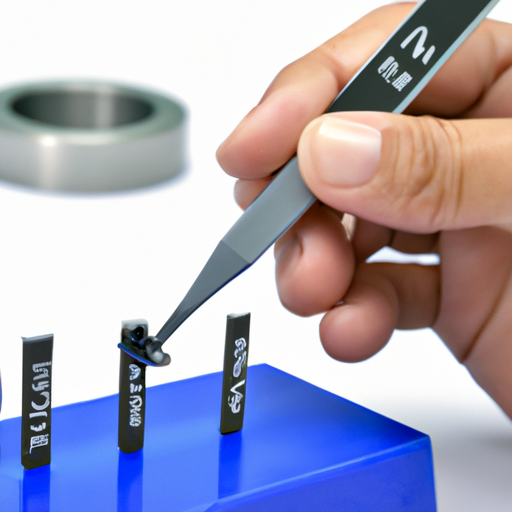
I. Introduction
Capacitors are fundamental components in modern electronics, serving as energy storage devices that can release energy quickly when needed. They play a crucial role in various applications, from power supply smoothing to signal coupling and decoupling in circuits. As technology advances, so do the principles and manufacturing processes behind capacitors, leading to improved performance, efficiency, and miniaturization. This blog post explores the latest capacitor principles, their types, manufacturing processes, innovations, challenges, and future trends.
II. Types of Capacitors
A. Electrolytic Capacitors
Electrolytic capacitors are polarized capacitors that use an electrolyte as one of their plates. They are known for their high capacitance values, making them ideal for applications requiring significant energy storage, such as power supply circuits and audio equipment. The construction typically involves an aluminum or tantalum foil as the anode, coated with a thin layer of oxide that acts as the dielectric, and a liquid or solid electrolyte as the cathode.
B. Ceramic Capacitors
Ceramic capacitors are non-polarized capacitors made from ceramic materials. They are categorized into Class 1 (temperature-stable) and Class 2 (high-capacitance) types. Class 1 capacitors are used in precision applications, while Class 2 capacitors are favored for their higher capacitance values in smaller sizes. Their applications range from decoupling in high-frequency circuits to timing applications in oscillators.
C. Film Capacitors
Film capacitors utilize thin plastic films as dielectrics. They are known for their stability, low self-inductance, and high insulation resistance. Common types include polyester, polypropylene, and polycarbonate capacitors. Film capacitors are widely used in audio equipment, power electronics, and applications requiring high reliability.
D. Supercapacitors
Supercapacitors, or ultracapacitors, are energy storage devices that bridge the gap between traditional capacitors and batteries. They offer high capacitance values and rapid charge/discharge capabilities. Supercapacitors are used in applications such as energy harvesting, backup power supplies, and electric vehicles, where quick bursts of energy are required.
E. Emerging Capacitor Technologies
Recent advancements have led to the development of solid-state capacitors and organic capacitors. Solid-state capacitors use solid electrolytes, offering improved safety and performance over traditional electrolytic capacitors. Organic capacitors, made from organic materials, promise to be lightweight and environmentally friendly, making them suitable for future applications.
III. Manufacturing Processes
A. Raw Material Selection
The manufacturing of capacitors begins with the selection of raw materials. The choice of dielectric materials is critical, as it directly affects the capacitor's performance. Common dielectric materials include ceramic, plastic films, and electrolytes. Conductive materials, such as aluminum, tantalum, and conductive polymers, are also essential for the capacitor's plates.
B. Fabrication Techniques
1. Thin-film Deposition
Thin-film deposition techniques, such as Physical Vapor Deposition (PVD) and Chemical Vapor Deposition (CVD), are widely used in capacitor manufacturing. PVD involves the physical transfer of material from a source to a substrate, creating thin films of dielectric or conductive materials. CVD, on the other hand, involves chemical reactions that deposit materials onto the substrate, allowing for precise control over film thickness and composition.
2. Screen Printing
Screen printing is a cost-effective method for producing capacitors, particularly for thick-film technologies. This technique involves applying conductive and dielectric inks onto substrates through a mesh screen, allowing for the creation of multilayer capacitors with complex geometries.
3. Stamping and Cutting
For certain types of capacitors, stamping and cutting techniques are employed to shape the conductive materials into the desired forms. This process is particularly common in the production of aluminum electrolytic capacitors, where foils are stamped into specific shapes before assembly.
C. Assembly Processes
The assembly of capacitors involves several steps, including layer stacking for multilayer capacitors and encapsulation techniques. In multilayer capacitors, layers of dielectric and conductive materials are stacked and pressed together to form a compact unit. Encapsulation techniques, such as potting or molding, protect the capacitor from environmental factors and enhance its durability.
D. Quality Control Measures
Quality control is paramount in capacitor manufacturing. Testing for capacitance and Equivalent Series Resistance (ESR) ensures that the capacitors meet performance specifications. Reliability testing under various conditions, such as temperature, humidity, and voltage stress, helps identify potential failures and ensures long-term performance.
IV. Innovations in Capacitor Manufacturing
A. Nanotechnology in Capacitors
Nanotechnology has revolutionized capacitor manufacturing by enabling the use of nanoscale materials that enhance performance. Nanoscale dielectrics can improve capacitance and reduce leakage currents, leading to smaller and more efficient capacitors. The impact of these innovations is significant, as they allow for the development of capacitors that can fit into increasingly compact electronic devices.
B. Sustainable Manufacturing Practices
As environmental concerns grow, the capacitor industry is adopting sustainable manufacturing practices. This includes the use of eco-friendly materials and energy-efficient production methods. Manufacturers are exploring biodegradable dielectrics and recyclable components to minimize their environmental footprint.
C. Automation and Industry 4.0
The integration of automation and Industry 4.0 technologies is transforming capacitor manufacturing. The use of AI and machine learning in production processes enhances efficiency and reduces waste. Smart manufacturing systems enable real-time monitoring and optimization of production lines, leading to higher quality and lower costs.
V. Challenges in Capacitor Manufacturing
Despite advancements, capacitor manufacturing faces several challenges. Material limitations can restrict the performance and miniaturization of capacitors. Cost considerations are also critical, as manufacturers strive to balance quality with affordability. Additionally, environmental regulations are becoming stricter, pushing manufacturers to adopt greener practices. Finally, competition and market dynamics require constant innovation to stay ahead in a rapidly evolving industry.
VI. Future Trends in Capacitor Technology
The future of capacitor technology is promising, with several trends emerging. Miniaturization and high-capacity designs are expected to continue, driven by the demand for smaller electronic devices. The integration of capacitors with renewable energy systems, such as solar and wind, will enhance energy storage solutions. The development of new materials, including graphene, holds the potential for capacitors with unprecedented performance characteristics. Furthermore, capacitors will play a crucial role in emerging technologies, such as electric vehicles and the Internet of Things (IoT), where efficient energy storage and management are essential.
VII. Conclusion
In summary, the manufacturing processes of the latest capacitor principles are evolving rapidly, driven by advancements in materials, fabrication techniques, and technology. Understanding the various types of capacitors, their manufacturing processes, and the innovations shaping the industry is essential for anyone involved in electronics. As research and development continue, the future outlook for capacitor manufacturing is bright, promising enhanced performance, sustainability, and integration with cutting-edge technologies.
VIII. References
1. Academic journals on capacitor technology and materials science.
2. Industry reports on capacitor market trends and innovations.
3. Books and articles discussing the principles and applications of capacitors in electronics.
This comprehensive overview of capacitor manufacturing processes highlights the significance of ongoing research and development in this critical field of electronics. As technology continues to advance, capacitors will remain integral to the performance and efficiency of electronic devices, paving the way for a more connected and energy-efficient future.