Common Production Processes for High-Voltage Parallel Capacitors
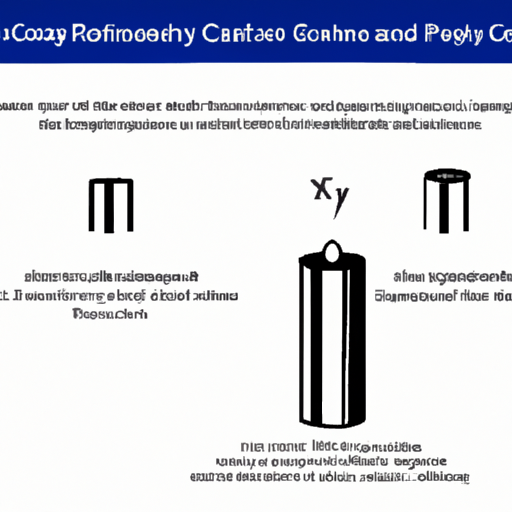
I. Introduction
High-voltage parallel capacitors are essential components in various electrical and electronic applications, ranging from power transmission systems to consumer electronics. These capacitors store and release electrical energy, helping to stabilize voltage and improve the efficiency of electrical systems. As technology advances, the demand for high-voltage capacitors continues to grow, necessitating a thorough understanding of their production processes. This blog post will explore the common production processes for high-voltage parallel capacitors, highlighting the materials, techniques, and challenges involved in their manufacturing.
II. Understanding High-Voltage Parallel Capacitors
A. Basic Principles of Capacitors
Capacitors are passive electronic components that store electrical energy in an electric field. The fundamental principle behind a capacitor is its ability to hold a charge, which is defined by its capacitance. Capacitance is measured in farads (F) and is influenced by the surface area of the electrodes, the distance between them, and the dielectric material used. High-voltage capacitors are designed to operate at elevated voltage levels, typically exceeding 1,000 volts, making them crucial for applications that require reliable energy storage and voltage regulation.
B. Specific Characteristics of High-Voltage Capacitors
High-voltage capacitors possess unique characteristics that differentiate them from standard capacitors. The choice of dielectric material is critical, as it must withstand high electric fields without breaking down. Common dielectric materials include polypropylene, polyester, and ceramic, each offering distinct advantages in terms of dielectric strength, temperature stability, and energy density. Additionally, the construction and design of high-voltage capacitors must account for factors such as thermal management, mechanical stress, and electrical insulation to ensure safe and efficient operation.
III. Raw Materials for High-Voltage Capacitors
A. Dielectric Materials
The dielectric material is a key component of high-voltage capacitors, as it determines the capacitor's voltage rating and overall performance. Polypropylene and polyester are popular choices due to their excellent dielectric properties and thermal stability. Ceramic dielectrics, on the other hand, are favored for their high dielectric strength and compact size, making them suitable for high-frequency applications. The selection of dielectric materials is based on factors such as voltage rating, temperature range, and application requirements.
B. Conductive Materials
Electrodes in high-voltage capacitors are typically made from conductive materials like aluminum or copper. These materials are chosen for their high conductivity and resistance to corrosion, which is essential for maintaining performance over time. The design of the electrodes, including their thickness and surface area, also plays a significant role in the capacitor's overall efficiency and reliability.
C. Insulating Materials
Insulation is critical in high-voltage applications to prevent electrical breakdown and ensure safety. Common insulating materials include various plastics and ceramics, which provide excellent dielectric properties and mechanical strength. The choice of insulation material is influenced by factors such as operating temperature, environmental conditions, and regulatory standards.
IV. Production Processes
A. Material Preparation
The production of high-voltage capacitors begins with the careful sourcing and quality control of raw materials. Manufacturers must ensure that the dielectric, conductive, and insulating materials meet stringent specifications. Pre-treatment processes, such as cleaning and drying, are essential to remove impurities and prepare the materials for subsequent processing.
B. Dielectric Layer Formation
The dielectric layer is a critical component of high-voltage capacitors, and its formation involves several techniques. Coating methods, such as spray, dip, or roll coating, are commonly used to apply the dielectric material onto the electrodes. For film capacitors, film extrusion is employed to create thin, uniform layers of dielectric material. After application, curing and drying processes are necessary to ensure the dielectric layer achieves the desired properties and adheres properly to the electrodes.
C. Electrode Fabrication
Electrode fabrication involves several methods to produce the conductive layers that will be paired with the dielectric material. Foil cutting and shaping are common techniques for creating aluminum or copper electrodes, while thin film deposition techniques may be used for more advanced applications. Surface treatments, such as anodization or plating, enhance the conductivity and corrosion resistance of the electrodes, ensuring long-term reliability.
D. Assembly of Capacitor Components
Once the dielectric and electrodes are prepared, the assembly process begins. This involves stacking and aligning the layers of dielectric and electrodes to form the capacitor structure. The connection of electrodes and dielectric layers is critical, as it affects the capacitor's performance. After assembly, encapsulation and sealing processes protect the internal components from environmental factors and mechanical stress.
E. Testing and Quality Assurance
Quality assurance is a vital step in the production of high-voltage capacitors. Electrical testing, including capacitance measurement and leakage current assessment, ensures that the capacitors meet performance specifications. Mechanical testing, such as pressure and thermal cycling tests, evaluates the durability and reliability of the capacitors under various conditions. Compliance with industry standards, such as those set by the International Electrotechnical Commission (IEC) and Underwriters Laboratories (UL), is also essential to ensure safety and performance.
V. Finalization and Packaging
After passing quality control, high-voltage capacitors undergo final inspection to ensure they meet all specifications. Packaging methods are crucial for protecting the capacitors during shipping and storage. Manufacturers often employ protective measures, such as shock-absorbing materials and moisture barriers, to prevent damage. Proper labeling and documentation are also essential for traceability and compliance with regulatory requirements.
VI. Challenges in Production
A. Technical Challenges
Manufacturing high-voltage capacitors presents several technical challenges, including the need for precise control over material properties and production processes. Variations in dielectric thickness, electrode alignment, and curing conditions can significantly impact performance and reliability.
B. Material Sourcing and Cost Considerations
Sourcing high-quality raw materials can be challenging, particularly for specialized dielectric and insulating materials. Fluctuations in material costs can also affect the overall production cost, making it essential for manufacturers to establish reliable supply chains and explore alternative materials when necessary.
C. Environmental and Regulatory Compliance
Manufacturers must navigate a complex landscape of environmental regulations and industry standards. Compliance with these regulations is essential to ensure the safety and sustainability of high-voltage capacitor production. This includes managing waste, reducing emissions, and adhering to safety standards throughout the manufacturing process.
VII. Future Trends in High-Voltage Capacitor Production
A. Innovations in Materials and Technologies
The future of high-voltage capacitor production is likely to be shaped by innovations in materials and manufacturing technologies. Researchers are exploring advanced dielectric materials, such as nanocomposites and organic materials, which could enhance performance and reduce costs. Additionally, advancements in manufacturing techniques, such as additive manufacturing, may enable the production of more complex capacitor designs.
B. Sustainability in Capacitor Manufacturing
As environmental concerns grow, the capacitor manufacturing industry is increasingly focusing on sustainability. This includes the development of eco-friendly materials, energy-efficient production processes, and recycling initiatives to minimize waste and reduce the environmental impact of capacitor production.
C. Market Demand and Evolving Applications
The demand for high-voltage capacitors is expected to rise as industries such as renewable energy, electric vehicles, and advanced electronics continue to expand. Manufacturers must stay attuned to evolving market needs and adapt their production processes to meet the requirements of new applications.
VIII. Conclusion
High-voltage parallel capacitors play a crucial role in modern electrical systems, and understanding their production processes is essential for manufacturers and engineers alike. From material selection to assembly and testing, each step in the production process contributes to the performance and reliability of these vital components. As the industry evolves, innovations in materials and technologies will shape the future of high-voltage capacitor manufacturing, ensuring that these components continue to meet the demands of an increasingly electrified world.
IX. References
1. Academic journals and articles on capacitor technology and manufacturing processes.
2. Industry standards and guidelines from organizations such as the IEC and UL.
3. Manufacturer resources and technical papers detailing advancements in capacitor design and production.
This comprehensive overview of the production processes for high-voltage parallel capacitors highlights the complexity and importance of these components in various applications, providing valuable insights for those involved in the industry.
Common Production Processes for High-Voltage Parallel Capacitors
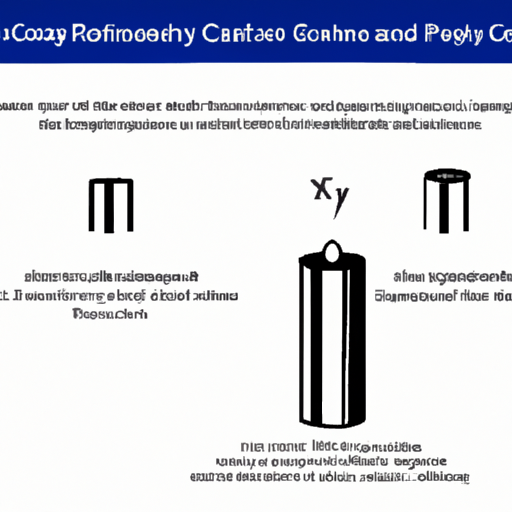
I. Introduction
High-voltage parallel capacitors are essential components in various electrical and electronic applications, ranging from power transmission systems to consumer electronics. These capacitors store and release electrical energy, helping to stabilize voltage and improve the efficiency of electrical systems. As technology advances, the demand for high-voltage capacitors continues to grow, necessitating a thorough understanding of their production processes. This blog post will explore the common production processes for high-voltage parallel capacitors, highlighting the materials, techniques, and challenges involved in their manufacturing.
II. Understanding High-Voltage Parallel Capacitors
A. Basic Principles of Capacitors
Capacitors are passive electronic components that store electrical energy in an electric field. The fundamental principle behind a capacitor is its ability to hold a charge, which is defined by its capacitance. Capacitance is measured in farads (F) and is influenced by the surface area of the electrodes, the distance between them, and the dielectric material used. High-voltage capacitors are designed to operate at elevated voltage levels, typically exceeding 1,000 volts, making them crucial for applications that require reliable energy storage and voltage regulation.
B. Specific Characteristics of High-Voltage Capacitors
High-voltage capacitors possess unique characteristics that differentiate them from standard capacitors. The choice of dielectric material is critical, as it must withstand high electric fields without breaking down. Common dielectric materials include polypropylene, polyester, and ceramic, each offering distinct advantages in terms of dielectric strength, temperature stability, and energy density. Additionally, the construction and design of high-voltage capacitors must account for factors such as thermal management, mechanical stress, and electrical insulation to ensure safe and efficient operation.
III. Raw Materials for High-Voltage Capacitors
A. Dielectric Materials
The dielectric material is a key component of high-voltage capacitors, as it determines the capacitor's voltage rating and overall performance. Polypropylene and polyester are popular choices due to their excellent dielectric properties and thermal stability. Ceramic dielectrics, on the other hand, are favored for their high dielectric strength and compact size, making them suitable for high-frequency applications. The selection of dielectric materials is based on factors such as voltage rating, temperature range, and application requirements.
B. Conductive Materials
Electrodes in high-voltage capacitors are typically made from conductive materials like aluminum or copper. These materials are chosen for their high conductivity and resistance to corrosion, which is essential for maintaining performance over time. The design of the electrodes, including their thickness and surface area, also plays a significant role in the capacitor's overall efficiency and reliability.
C. Insulating Materials
Insulation is critical in high-voltage applications to prevent electrical breakdown and ensure safety. Common insulating materials include various plastics and ceramics, which provide excellent dielectric properties and mechanical strength. The choice of insulation material is influenced by factors such as operating temperature, environmental conditions, and regulatory standards.
IV. Production Processes
A. Material Preparation
The production of high-voltage capacitors begins with the careful sourcing and quality control of raw materials. Manufacturers must ensure that the dielectric, conductive, and insulating materials meet stringent specifications. Pre-treatment processes, such as cleaning and drying, are essential to remove impurities and prepare the materials for subsequent processing.
B. Dielectric Layer Formation
The dielectric layer is a critical component of high-voltage capacitors, and its formation involves several techniques. Coating methods, such as spray, dip, or roll coating, are commonly used to apply the dielectric material onto the electrodes. For film capacitors, film extrusion is employed to create thin, uniform layers of dielectric material. After application, curing and drying processes are necessary to ensure the dielectric layer achieves the desired properties and adheres properly to the electrodes.
C. Electrode Fabrication
Electrode fabrication involves several methods to produce the conductive layers that will be paired with the dielectric material. Foil cutting and shaping are common techniques for creating aluminum or copper electrodes, while thin film deposition techniques may be used for more advanced applications. Surface treatments, such as anodization or plating, enhance the conductivity and corrosion resistance of the electrodes, ensuring long-term reliability.
D. Assembly of Capacitor Components
Once the dielectric and electrodes are prepared, the assembly process begins. This involves stacking and aligning the layers of dielectric and electrodes to form the capacitor structure. The connection of electrodes and dielectric layers is critical, as it affects the capacitor's performance. After assembly, encapsulation and sealing processes protect the internal components from environmental factors and mechanical stress.
E. Testing and Quality Assurance
Quality assurance is a vital step in the production of high-voltage capacitors. Electrical testing, including capacitance measurement and leakage current assessment, ensures that the capacitors meet performance specifications. Mechanical testing, such as pressure and thermal cycling tests, evaluates the durability and reliability of the capacitors under various conditions. Compliance with industry standards, such as those set by the International Electrotechnical Commission (IEC) and Underwriters Laboratories (UL), is also essential to ensure safety and performance.
V. Finalization and Packaging
After passing quality control, high-voltage capacitors undergo final inspection to ensure they meet all specifications. Packaging methods are crucial for protecting the capacitors during shipping and storage. Manufacturers often employ protective measures, such as shock-absorbing materials and moisture barriers, to prevent damage. Proper labeling and documentation are also essential for traceability and compliance with regulatory requirements.
VI. Challenges in Production
A. Technical Challenges
Manufacturing high-voltage capacitors presents several technical challenges, including the need for precise control over material properties and production processes. Variations in dielectric thickness, electrode alignment, and curing conditions can significantly impact performance and reliability.
B. Material Sourcing and Cost Considerations
Sourcing high-quality raw materials can be challenging, particularly for specialized dielectric and insulating materials. Fluctuations in material costs can also affect the overall production cost, making it essential for manufacturers to establish reliable supply chains and explore alternative materials when necessary.
C. Environmental and Regulatory Compliance
Manufacturers must navigate a complex landscape of environmental regulations and industry standards. Compliance with these regulations is essential to ensure the safety and sustainability of high-voltage capacitor production. This includes managing waste, reducing emissions, and adhering to safety standards throughout the manufacturing process.
VII. Future Trends in High-Voltage Capacitor Production
A. Innovations in Materials and Technologies
The future of high-voltage capacitor production is likely to be shaped by innovations in materials and manufacturing technologies. Researchers are exploring advanced dielectric materials, such as nanocomposites and organic materials, which could enhance performance and reduce costs. Additionally, advancements in manufacturing techniques, such as additive manufacturing, may enable the production of more complex capacitor designs.
B. Sustainability in Capacitor Manufacturing
As environmental concerns grow, the capacitor manufacturing industry is increasingly focusing on sustainability. This includes the development of eco-friendly materials, energy-efficient production processes, and recycling initiatives to minimize waste and reduce the environmental impact of capacitor production.
C. Market Demand and Evolving Applications
The demand for high-voltage capacitors is expected to rise as industries such as renewable energy, electric vehicles, and advanced electronics continue to expand. Manufacturers must stay attuned to evolving market needs and adapt their production processes to meet the requirements of new applications.
VIII. Conclusion
High-voltage parallel capacitors play a crucial role in modern electrical systems, and understanding their production processes is essential for manufacturers and engineers alike. From material selection to assembly and testing, each step in the production process contributes to the performance and reliability of these vital components. As the industry evolves, innovations in materials and technologies will shape the future of high-voltage capacitor manufacturing, ensuring that these components continue to meet the demands of an increasingly electrified world.
IX. References
1. Academic journals and articles on capacitor technology and manufacturing processes.
2. Industry standards and guidelines from organizations such as the IEC and UL.
3. Manufacturer resources and technical papers detailing advancements in capacitor design and production.
This comprehensive overview of the production processes for high-voltage parallel capacitors highlights the complexity and importance of these components in various applications, providing valuable insights for those involved in the industry.