Manufacturing Processes of the Latest Metallized Film Capacitors
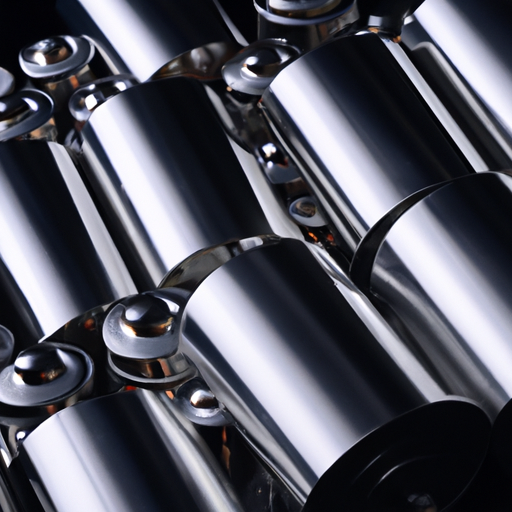
I. Introduction
Metallized film capacitors are essential components in modern electronic devices, known for their reliability, stability, and versatility. These capacitors are widely used in applications ranging from power electronics to audio equipment, where they serve critical roles in filtering, energy storage, and signal coupling. Understanding the manufacturing processes behind these capacitors is crucial for appreciating their performance and reliability. This blog post will explore the various types of metallized film capacitors, the raw materials used, the intricate manufacturing processes, innovations in the field, challenges faced by manufacturers, and future trends.
II. Types of Metallized Film Capacitors
Metallized film capacitors can be categorized based on the type of polymer film used as the dielectric. The most common types include:
A. Polypropylene (PP) Capacitors
Polypropylene capacitors are known for their low dielectric losses and high insulation resistance. They are often used in applications requiring high stability and low distortion, such as audio circuits and power electronics.
B. Polyester (PET) Capacitors
Polyester capacitors are more cost-effective than polypropylene capacitors and are widely used in general-purpose applications. They offer decent performance but have higher dielectric losses compared to PP capacitors.
C. Polycarbonate (PC) Capacitors
Polycarbonate capacitors provide excellent electrical properties and stability over a wide temperature range. However, due to the phasing out of polycarbonate materials for environmental reasons, their use has declined.
D. Other Materials and Their Applications
Other materials, such as polyphenylene sulfide (PPS) and polyimide, are also used in specialized applications, particularly where high-temperature resistance is required.
III. Raw Materials
The performance of metallized film capacitors heavily relies on the quality of raw materials used in their production.
A. Film Substrates
The film substrate serves as the dielectric material in capacitors. Key properties include dielectric strength, thermal stability, and moisture resistance. Common materials used include:
1. **Polypropylene (PP)**: Offers low dielectric losses and high insulation resistance.
2. **Polyester (PET)**: Cost-effective with moderate performance.
3. **Polycarbonate (PC)**: Excellent electrical properties but less common due to environmental concerns.
B. Metallization Materials
The choice of metallization material significantly impacts the capacitor's performance. Common metals used include:
1. **Aluminum**: Widely used due to its good conductivity and cost-effectiveness.
2. **Zinc**: Sometimes used for specific applications requiring lower costs.
The method of applying the metallization also affects performance, with various coating techniques available.
IV. Manufacturing Processes
The manufacturing of metallized film capacitors involves several key processes, each critical to ensuring the final product meets performance standards.
A. Film Production
1. **Extrusion of Polymer Films**: The first step in manufacturing involves extruding polymer materials into thin films. This process requires precise control over temperature and pressure to ensure uniform thickness and quality.
2. **Thickness Control and Quality Assurance**: The thickness of the film is crucial for determining the capacitor's capacitance. Quality assurance measures, including optical and electronic testing, are implemented to ensure consistency.
B. Metallization Techniques
The metallization process involves applying a conductive layer to the dielectric film. Several techniques are commonly used:
1. **Vacuum Deposition**:
- **Process Overview**: In this method, metal is vaporized in a vacuum chamber and deposited onto the film surface.
- **Advantages and Disadvantages**: Vacuum deposition provides a uniform coating but can be costly and time-consuming.
2. **Sputtering**:
- **Process Overview**: Sputtering involves bombarding a metal target with ions, causing atoms to be ejected and deposited onto the film.
- **Advantages and Disadvantages**: This method allows for precise control over thickness but requires complex equipment.
3. **Chemical Vapor Deposition (CVD)**:
- **Process Overview**: CVD involves chemical reactions that deposit a thin film of material onto the substrate.
- **Advantages and Disadvantages**: CVD can produce high-quality coatings but is often more expensive than other methods.
C. Capacitor Assembly
Once the film is metallized, the assembly process begins:
1. **Layering of Film and Metallization**: The metallized film is layered to create the capacitor structure.
2. **Winding or Stacking Methods**: Capacitors can be wound into cylindrical shapes or stacked in layers, depending on design requirements.
3. **Encapsulation and Insulation**: The assembled capacitor is then encapsulated to protect it from environmental factors and ensure electrical insulation.
D. Testing and Quality Control
Quality control is paramount in capacitor manufacturing:
1. **Electrical Testing**: Capacitors undergo rigorous electrical testing to measure capacitance, equivalent series resistance (ESR), and leakage current.
2. **Environmental Testing**: Capacitors are subjected to temperature and humidity tests to ensure reliability under various conditions.
3. **Reliability Testing**: Long-term reliability tests assess the capacitor's lifespan and failure rates, ensuring they meet industry standards.
V. Innovations in Manufacturing
The field of metallized film capacitors is continuously evolving, driven by innovations in materials and manufacturing techniques.
A. Advances in Materials Science
New materials are being developed to enhance performance, such as high-temperature polymers and advanced metallization techniques that improve conductivity and reduce losses.
B. Automation and Industry 4.0
The integration of automation and smart manufacturing technologies is streamlining production processes, improving efficiency, and reducing costs.
C. Sustainable Manufacturing Practices
Manufacturers are increasingly adopting sustainable practices, such as recycling materials and reducing waste, to minimize their environmental impact.
D. Impact of Nanotechnology on Performance
Nanotechnology is being explored to enhance the properties of dielectric materials, potentially leading to capacitors with higher capacitance and lower losses.
VI. Challenges in Manufacturing
Despite advancements, manufacturers face several challenges:
A. Cost Management
Balancing production costs while maintaining high quality is a constant challenge in the competitive capacitor market.
B. Quality Consistency
Ensuring consistent quality across production batches is critical, requiring stringent quality control measures.
C. Environmental Regulations
Manufacturers must navigate complex environmental regulations, particularly concerning materials and waste management.
D. Supply Chain Issues
Global supply chain disruptions can impact the availability of raw materials, affecting production schedules and costs.
VII. Future Trends
The future of metallized film capacitors looks promising, with several emerging trends:
A. Emerging Applications in Renewable Energy
As the demand for renewable energy sources grows, metallized film capacitors are increasingly used in applications like solar inverters and wind turbines.
B. Miniaturization and High-Capacity Designs
There is a trend towards miniaturization, with manufacturers developing smaller capacitors that offer higher capacitance values, catering to the needs of compact electronic devices.
C. Integration with Smart Technologies
The integration of capacitors with smart technologies, such as IoT devices, is expected to drive innovation and create new applications.
VIII. Conclusion
In summary, metallized film capacitors play a vital role in modern electronics, and understanding their manufacturing processes is essential for appreciating their significance. From the selection of raw materials to advanced manufacturing techniques and quality control measures, each step is crucial in producing reliable and high-performance capacitors. As the industry continues to innovate and adapt to new challenges, the future of metallized film capacitors looks bright, with exciting developments on the horizon.
IX. References
1. Academic journals on capacitor technology and materials science.
2. Industry reports on trends and innovations in capacitor manufacturing.
3. Manufacturer specifications and white papers detailing production processes and quality standards.
This comprehensive overview of metallized film capacitors highlights the intricate processes involved in their manufacturing and the ongoing advancements that will shape their future in the electronics industry.
Manufacturing Processes of the Latest Metallized Film Capacitors
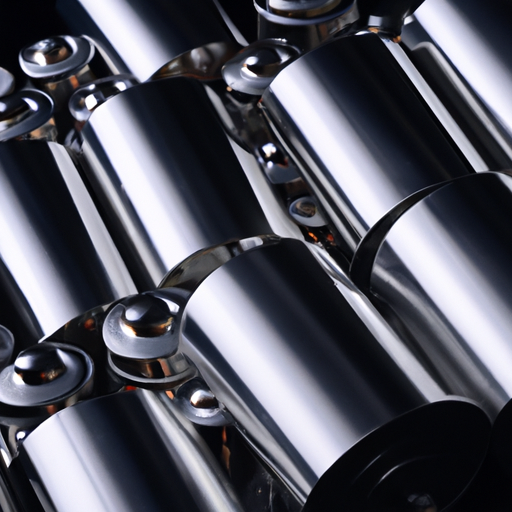
I. Introduction
Metallized film capacitors are essential components in modern electronic devices, known for their reliability, stability, and versatility. These capacitors are widely used in applications ranging from power electronics to audio equipment, where they serve critical roles in filtering, energy storage, and signal coupling. Understanding the manufacturing processes behind these capacitors is crucial for appreciating their performance and reliability. This blog post will explore the various types of metallized film capacitors, the raw materials used, the intricate manufacturing processes, innovations in the field, challenges faced by manufacturers, and future trends.
II. Types of Metallized Film Capacitors
Metallized film capacitors can be categorized based on the type of polymer film used as the dielectric. The most common types include:
A. Polypropylene (PP) Capacitors
Polypropylene capacitors are known for their low dielectric losses and high insulation resistance. They are often used in applications requiring high stability and low distortion, such as audio circuits and power electronics.
B. Polyester (PET) Capacitors
Polyester capacitors are more cost-effective than polypropylene capacitors and are widely used in general-purpose applications. They offer decent performance but have higher dielectric losses compared to PP capacitors.
C. Polycarbonate (PC) Capacitors
Polycarbonate capacitors provide excellent electrical properties and stability over a wide temperature range. However, due to the phasing out of polycarbonate materials for environmental reasons, their use has declined.
D. Other Materials and Their Applications
Other materials, such as polyphenylene sulfide (PPS) and polyimide, are also used in specialized applications, particularly where high-temperature resistance is required.
III. Raw Materials
The performance of metallized film capacitors heavily relies on the quality of raw materials used in their production.
A. Film Substrates
The film substrate serves as the dielectric material in capacitors. Key properties include dielectric strength, thermal stability, and moisture resistance. Common materials used include:
1. **Polypropylene (PP)**: Offers low dielectric losses and high insulation resistance.
2. **Polyester (PET)**: Cost-effective with moderate performance.
3. **Polycarbonate (PC)**: Excellent electrical properties but less common due to environmental concerns.
B. Metallization Materials
The choice of metallization material significantly impacts the capacitor's performance. Common metals used include:
1. **Aluminum**: Widely used due to its good conductivity and cost-effectiveness.
2. **Zinc**: Sometimes used for specific applications requiring lower costs.
The method of applying the metallization also affects performance, with various coating techniques available.
IV. Manufacturing Processes
The manufacturing of metallized film capacitors involves several key processes, each critical to ensuring the final product meets performance standards.
A. Film Production
1. **Extrusion of Polymer Films**: The first step in manufacturing involves extruding polymer materials into thin films. This process requires precise control over temperature and pressure to ensure uniform thickness and quality.
2. **Thickness Control and Quality Assurance**: The thickness of the film is crucial for determining the capacitor's capacitance. Quality assurance measures, including optical and electronic testing, are implemented to ensure consistency.
B. Metallization Techniques
The metallization process involves applying a conductive layer to the dielectric film. Several techniques are commonly used:
1. **Vacuum Deposition**:
- **Process Overview**: In this method, metal is vaporized in a vacuum chamber and deposited onto the film surface.
- **Advantages and Disadvantages**: Vacuum deposition provides a uniform coating but can be costly and time-consuming.
2. **Sputtering**:
- **Process Overview**: Sputtering involves bombarding a metal target with ions, causing atoms to be ejected and deposited onto the film.
- **Advantages and Disadvantages**: This method allows for precise control over thickness but requires complex equipment.
3. **Chemical Vapor Deposition (CVD)**:
- **Process Overview**: CVD involves chemical reactions that deposit a thin film of material onto the substrate.
- **Advantages and Disadvantages**: CVD can produce high-quality coatings but is often more expensive than other methods.
C. Capacitor Assembly
Once the film is metallized, the assembly process begins:
1. **Layering of Film and Metallization**: The metallized film is layered to create the capacitor structure.
2. **Winding or Stacking Methods**: Capacitors can be wound into cylindrical shapes or stacked in layers, depending on design requirements.
3. **Encapsulation and Insulation**: The assembled capacitor is then encapsulated to protect it from environmental factors and ensure electrical insulation.
D. Testing and Quality Control
Quality control is paramount in capacitor manufacturing:
1. **Electrical Testing**: Capacitors undergo rigorous electrical testing to measure capacitance, equivalent series resistance (ESR), and leakage current.
2. **Environmental Testing**: Capacitors are subjected to temperature and humidity tests to ensure reliability under various conditions.
3. **Reliability Testing**: Long-term reliability tests assess the capacitor's lifespan and failure rates, ensuring they meet industry standards.
V. Innovations in Manufacturing
The field of metallized film capacitors is continuously evolving, driven by innovations in materials and manufacturing techniques.
A. Advances in Materials Science
New materials are being developed to enhance performance, such as high-temperature polymers and advanced metallization techniques that improve conductivity and reduce losses.
B. Automation and Industry 4.0
The integration of automation and smart manufacturing technologies is streamlining production processes, improving efficiency, and reducing costs.
C. Sustainable Manufacturing Practices
Manufacturers are increasingly adopting sustainable practices, such as recycling materials and reducing waste, to minimize their environmental impact.
D. Impact of Nanotechnology on Performance
Nanotechnology is being explored to enhance the properties of dielectric materials, potentially leading to capacitors with higher capacitance and lower losses.
VI. Challenges in Manufacturing
Despite advancements, manufacturers face several challenges:
A. Cost Management
Balancing production costs while maintaining high quality is a constant challenge in the competitive capacitor market.
B. Quality Consistency
Ensuring consistent quality across production batches is critical, requiring stringent quality control measures.
C. Environmental Regulations
Manufacturers must navigate complex environmental regulations, particularly concerning materials and waste management.
D. Supply Chain Issues
Global supply chain disruptions can impact the availability of raw materials, affecting production schedules and costs.
VII. Future Trends
The future of metallized film capacitors looks promising, with several emerging trends:
A. Emerging Applications in Renewable Energy
As the demand for renewable energy sources grows, metallized film capacitors are increasingly used in applications like solar inverters and wind turbines.
B. Miniaturization and High-Capacity Designs
There is a trend towards miniaturization, with manufacturers developing smaller capacitors that offer higher capacitance values, catering to the needs of compact electronic devices.
C. Integration with Smart Technologies
The integration of capacitors with smart technologies, such as IoT devices, is expected to drive innovation and create new applications.
VIII. Conclusion
In summary, metallized film capacitors play a vital role in modern electronics, and understanding their manufacturing processes is essential for appreciating their significance. From the selection of raw materials to advanced manufacturing techniques and quality control measures, each step is crucial in producing reliable and high-performance capacitors. As the industry continues to innovate and adapt to new challenges, the future of metallized film capacitors looks bright, with exciting developments on the horizon.
IX. References
1. Academic journals on capacitor technology and materials science.
2. Industry reports on trends and innovations in capacitor manufacturing.
3. Manufacturer specifications and white papers detailing production processes and quality standards.
This comprehensive overview of metallized film capacitors highlights the intricate processes involved in their manufacturing and the ongoing advancements that will shape their future in the electronics industry.