The Production Process of Mainstream Capacitors
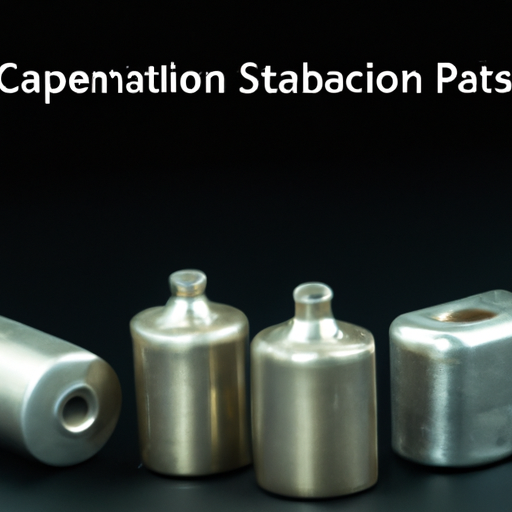
I. Introduction
Capacitors are essential components in the world of electronics, serving as energy storage devices that can release energy quickly when needed. They play a crucial role in various applications, from smoothing out voltage fluctuations in power supplies to enabling signal processing in communication devices. As technology continues to advance, the demand for capacitors has surged, leading to a sophisticated production process that ensures high quality and reliability. This blog post will explore the production process of mainstream capacitors, detailing the types, raw materials, design considerations, manufacturing steps, quality control measures, and future trends in the industry.
II. Types of Capacitors
Capacitors come in various types, each designed for specific applications and performance characteristics. The most common types include:
A. Ceramic Capacitors
Ceramic capacitors are widely used due to their small size, low cost, and stability. They are made from ceramic materials that serve as the dielectric.
B. Electrolytic Capacitors
These capacitors are known for their high capacitance values and are often used in power supply applications. They utilize an electrolyte as one of the conductive plates.
C. Film Capacitors
Film capacitors are made from thin plastic films and are known for their reliability and low loss characteristics. They are commonly used in audio and signal applications.
D. Tantalum Capacitors
Tantalum capacitors are known for their high capacitance in a small volume and are often used in military and aerospace applications due to their reliability.
E. Supercapacitors
Supercapacitors, or ultracapacitors, have a very high capacitance and are used for energy storage applications, such as in electric vehicles and renewable energy systems.
F. Comparison of Different Types
Each type of capacitor has its advantages and disadvantages, making them suitable for different applications. For instance, while ceramic capacitors are excellent for high-frequency applications, electrolytic capacitors are preferred for bulk energy storage.
III. Raw Materials
A. Overview of Materials Used in Capacitor Production
The production of capacitors requires a variety of raw materials, primarily categorized into dielectric and conductive materials.
1. **Dielectric Materials**: These materials, which include ceramics, plastics, and electrolytes, are crucial for storing electrical energy.
2. **Conductive Materials**: Metals such as aluminum, tantalum, and copper are used for the conductive plates of capacitors.
B. Sourcing and Quality Control of Raw Materials
The quality of raw materials directly impacts the performance and reliability of capacitors. Manufacturers often establish strict sourcing protocols and conduct thorough quality control checks to ensure that materials meet industry standards.
IV. Design and Engineering
A. Initial Design Considerations
The design phase is critical in capacitor production, where engineers consider several factors:
1. **Capacitance Value**: The amount of charge a capacitor can store.
2. **Voltage Rating**: The maximum voltage the capacitor can handle without failure.
3. **Size and Form Factor**: The physical dimensions of the capacitor, which can affect its application.
B. Simulation and Modeling
Advanced simulation tools are used to model the electrical behavior of capacitors under various conditions, allowing engineers to optimize designs before moving to production.
C. Prototyping and Testing
Prototypes are created to test the design's performance. This phase includes rigorous testing to ensure that the capacitor meets the required specifications.
V. Manufacturing Process
A. General Steps in Capacitor Production
The manufacturing process of capacitors involves several key steps:
1. **Preparation of Materials**: Raw materials are processed and prepared for assembly.
2. **Layering and Assembly**: The dielectric and conductive materials are layered and assembled into the capacitor structure.
3. **Encapsulation**: The assembled capacitor is encapsulated to protect it from environmental factors.
B. Specific Processes for Different Capacitor Types
Each type of capacitor has unique manufacturing processes:
1. Ceramic Capacitors
Powder Preparation: Ceramic powders are mixed and processed to create the dielectric material.
Pressing and Sintering: The powder is pressed into shape and then sintered at high temperatures to form a solid dielectric.
2. Electrolytic Capacitors
Anodization: An aluminum foil is anodized to create a thin oxide layer that serves as the dielectric.
Electrolyte Filling: The capacitor is filled with an electrolyte, which enhances its capacitance.
3. Film Capacitors
Film Production: Thin plastic films are produced and treated to enhance their dielectric properties.
Winding and Cutting: The films are wound into rolls and cut to the desired size for assembly.
4. Tantalum Capacitors
Tantalum Powder Processing: Tantalum powder is processed and shaped into an anode.
Sintering and Assembly: The anode is sintered, and the capacitor is assembled with a dielectric and cathode.
5. Supercapacitors
Electrode Preparation: Carbon-based materials are processed to create electrodes with high surface area.
Electrolyte Application: An electrolyte is applied to facilitate charge storage.
VI. Quality Control
A. Importance of Quality Assurance in Capacitor Production
Quality assurance is vital in capacitor production to ensure reliability and performance. Capacitors are often used in critical applications where failure can lead to significant consequences.
B. Testing Methods
Various testing methods are employed to assess the quality of capacitors:
1. **Electrical Testing**: Measures capacitance, leakage current, and equivalent series resistance (ESR).
2. **Environmental Testing**: Assesses performance under different temperature and humidity conditions.
3. **Reliability Testing**: Evaluates long-term performance and failure rates.
C. Compliance with Industry Standards
Manufacturers must comply with industry standards, such as ISO and IEC, to ensure that their products meet safety and performance requirements.
VII. Packaging and Distribution
A. Packaging Methods for Different Capacitor Types
Capacitors are packaged in various ways, depending on their type and application. For instance, surface-mount capacitors are typically packaged in tape and reel formats for automated assembly.
B. Logistics and Distribution Channels
Efficient logistics and distribution channels are essential for delivering capacitors to manufacturers and end-users. This includes managing inventory and ensuring timely delivery.
C. Importance of Proper Handling and Storage
Capacitors must be handled and stored properly to prevent damage. This includes maintaining appropriate temperature and humidity levels to avoid degradation of materials.
VIII. Future Trends in Capacitor Production
A. Innovations in Materials and Technology
The capacitor industry is witnessing innovations in materials, such as the development of new dielectric materials that enhance performance and reduce size.
B. Environmental Considerations and Sustainability
Sustainability is becoming increasingly important, with manufacturers exploring eco-friendly materials and production processes to minimize environmental impact.
C. Market Trends and Demand for Capacitors
The demand for capacitors is expected to grow, driven by advancements in technology, such as electric vehicles, renewable energy systems, and consumer electronics.
IX. Conclusion
In conclusion, the production process of mainstream capacitors is a complex and multifaceted endeavor that involves careful consideration of materials, design, manufacturing, and quality control. Capacitors are integral to modern electronics, enabling a wide range of applications that enhance our daily lives. As technology continues to evolve, the capacitor industry will adapt, embracing innovations and sustainability to meet the growing demand for reliable and efficient energy storage solutions. The future of capacitor manufacturing looks promising, with exciting developments on the horizon that will shape the next generation of electronic devices.
The Production Process of Mainstream Capacitors
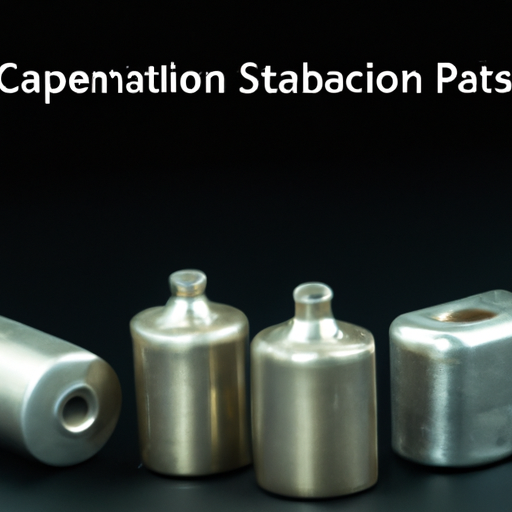
I. Introduction
Capacitors are essential components in the world of electronics, serving as energy storage devices that can release energy quickly when needed. They play a crucial role in various applications, from smoothing out voltage fluctuations in power supplies to enabling signal processing in communication devices. As technology continues to advance, the demand for capacitors has surged, leading to a sophisticated production process that ensures high quality and reliability. This blog post will explore the production process of mainstream capacitors, detailing the types, raw materials, design considerations, manufacturing steps, quality control measures, and future trends in the industry.
II. Types of Capacitors
Capacitors come in various types, each designed for specific applications and performance characteristics. The most common types include:
A. Ceramic Capacitors
Ceramic capacitors are widely used due to their small size, low cost, and stability. They are made from ceramic materials that serve as the dielectric.
B. Electrolytic Capacitors
These capacitors are known for their high capacitance values and are often used in power supply applications. They utilize an electrolyte as one of the conductive plates.
C. Film Capacitors
Film capacitors are made from thin plastic films and are known for their reliability and low loss characteristics. They are commonly used in audio and signal applications.
D. Tantalum Capacitors
Tantalum capacitors are known for their high capacitance in a small volume and are often used in military and aerospace applications due to their reliability.
E. Supercapacitors
Supercapacitors, or ultracapacitors, have a very high capacitance and are used for energy storage applications, such as in electric vehicles and renewable energy systems.
F. Comparison of Different Types
Each type of capacitor has its advantages and disadvantages, making them suitable for different applications. For instance, while ceramic capacitors are excellent for high-frequency applications, electrolytic capacitors are preferred for bulk energy storage.
III. Raw Materials
A. Overview of Materials Used in Capacitor Production
The production of capacitors requires a variety of raw materials, primarily categorized into dielectric and conductive materials.
1. **Dielectric Materials**: These materials, which include ceramics, plastics, and electrolytes, are crucial for storing electrical energy.
2. **Conductive Materials**: Metals such as aluminum, tantalum, and copper are used for the conductive plates of capacitors.
B. Sourcing and Quality Control of Raw Materials
The quality of raw materials directly impacts the performance and reliability of capacitors. Manufacturers often establish strict sourcing protocols and conduct thorough quality control checks to ensure that materials meet industry standards.
IV. Design and Engineering
A. Initial Design Considerations
The design phase is critical in capacitor production, where engineers consider several factors:
1. **Capacitance Value**: The amount of charge a capacitor can store.
2. **Voltage Rating**: The maximum voltage the capacitor can handle without failure.
3. **Size and Form Factor**: The physical dimensions of the capacitor, which can affect its application.
B. Simulation and Modeling
Advanced simulation tools are used to model the electrical behavior of capacitors under various conditions, allowing engineers to optimize designs before moving to production.
C. Prototyping and Testing
Prototypes are created to test the design's performance. This phase includes rigorous testing to ensure that the capacitor meets the required specifications.
V. Manufacturing Process
A. General Steps in Capacitor Production
The manufacturing process of capacitors involves several key steps:
1. **Preparation of Materials**: Raw materials are processed and prepared for assembly.
2. **Layering and Assembly**: The dielectric and conductive materials are layered and assembled into the capacitor structure.
3. **Encapsulation**: The assembled capacitor is encapsulated to protect it from environmental factors.
B. Specific Processes for Different Capacitor Types
Each type of capacitor has unique manufacturing processes:
1. Ceramic Capacitors
Powder Preparation: Ceramic powders are mixed and processed to create the dielectric material.
Pressing and Sintering: The powder is pressed into shape and then sintered at high temperatures to form a solid dielectric.
2. Electrolytic Capacitors
Anodization: An aluminum foil is anodized to create a thin oxide layer that serves as the dielectric.
Electrolyte Filling: The capacitor is filled with an electrolyte, which enhances its capacitance.
3. Film Capacitors
Film Production: Thin plastic films are produced and treated to enhance their dielectric properties.
Winding and Cutting: The films are wound into rolls and cut to the desired size for assembly.
4. Tantalum Capacitors
Tantalum Powder Processing: Tantalum powder is processed and shaped into an anode.
Sintering and Assembly: The anode is sintered, and the capacitor is assembled with a dielectric and cathode.
5. Supercapacitors
Electrode Preparation: Carbon-based materials are processed to create electrodes with high surface area.
Electrolyte Application: An electrolyte is applied to facilitate charge storage.
VI. Quality Control
A. Importance of Quality Assurance in Capacitor Production
Quality assurance is vital in capacitor production to ensure reliability and performance. Capacitors are often used in critical applications where failure can lead to significant consequences.
B. Testing Methods
Various testing methods are employed to assess the quality of capacitors:
1. **Electrical Testing**: Measures capacitance, leakage current, and equivalent series resistance (ESR).
2. **Environmental Testing**: Assesses performance under different temperature and humidity conditions.
3. **Reliability Testing**: Evaluates long-term performance and failure rates.
C. Compliance with Industry Standards
Manufacturers must comply with industry standards, such as ISO and IEC, to ensure that their products meet safety and performance requirements.
VII. Packaging and Distribution
A. Packaging Methods for Different Capacitor Types
Capacitors are packaged in various ways, depending on their type and application. For instance, surface-mount capacitors are typically packaged in tape and reel formats for automated assembly.
B. Logistics and Distribution Channels
Efficient logistics and distribution channels are essential for delivering capacitors to manufacturers and end-users. This includes managing inventory and ensuring timely delivery.
C. Importance of Proper Handling and Storage
Capacitors must be handled and stored properly to prevent damage. This includes maintaining appropriate temperature and humidity levels to avoid degradation of materials.
VIII. Future Trends in Capacitor Production
A. Innovations in Materials and Technology
The capacitor industry is witnessing innovations in materials, such as the development of new dielectric materials that enhance performance and reduce size.
B. Environmental Considerations and Sustainability
Sustainability is becoming increasingly important, with manufacturers exploring eco-friendly materials and production processes to minimize environmental impact.
C. Market Trends and Demand for Capacitors
The demand for capacitors is expected to grow, driven by advancements in technology, such as electric vehicles, renewable energy systems, and consumer electronics.
IX. Conclusion
In conclusion, the production process of mainstream capacitors is a complex and multifaceted endeavor that involves careful consideration of materials, design, manufacturing, and quality control. Capacitors are integral to modern electronics, enabling a wide range of applications that enhance our daily lives. As technology continues to evolve, the capacitor industry will adapt, embracing innovations and sustainability to meet the growing demand for reliable and efficient energy storage solutions. The future of capacitor manufacturing looks promising, with exciting developments on the horizon that will shape the next generation of electronic devices.