What are the Product Standards for Capacitor Parallel Connection?
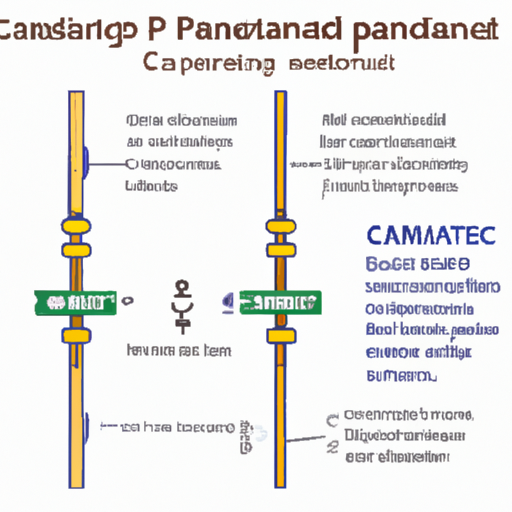
I. Introduction
Capacitors are fundamental components in electrical circuits, serving various roles such as energy storage, filtering, and signal coupling. Understanding the product standards for capacitor parallel connections is crucial for engineers and designers to ensure reliability, safety, and performance in their applications. This article will explore the basics of capacitor parallel connections, the relevant product standards, technical considerations, testing methods, challenges, and best practices.
II. Basics of Capacitor Parallel Connection
A. Explanation of Capacitor Parallel Connection
When capacitors are connected in parallel, their capacitance values add up, resulting in a total capacitance that is greater than any individual capacitor in the circuit. This configuration allows for increased energy storage and improved performance in various applications. In a parallel connection, the voltage across each capacitor remains the same, while the total current is the sum of the currents through each capacitor.
B. Advantages of Parallel Connections
The advantages of connecting capacitors in parallel include:
1. **Increased Capacitance**: The total capacitance increases, allowing for greater energy storage.
2. **Improved Reliability**: If one capacitor fails, the others can continue to function, enhancing the overall reliability of the circuit.
3. **Flexibility in Design**: Engineers can mix and match capacitors with different values and characteristics to achieve desired performance.
C. Common Applications of Parallel Capacitor Connections
Parallel capacitor connections are widely used in various applications, including:
1. **Power Factor Correction**: Capacitors are used to improve the power factor in electrical systems, reducing energy losses and improving efficiency.
2. **Energy Storage**: In power electronics, capacitors store energy for later use, smoothing out voltage fluctuations.
3. **Signal Coupling and Decoupling**: Capacitors help filter out noise and stabilize voltage levels in signal processing applications.
III. Product Standards Overview
A. Definition of Product Standards in Electronics
Product standards in electronics are established guidelines that ensure the safety, reliability, and performance of electronic components, including capacitors. These standards are developed by various organizations and are essential for manufacturers, engineers, and consumers.
B. Importance of Adhering to Product Standards
Adhering to product standards is vital for several reasons:
1. **Safety**: Standards help prevent electrical hazards and ensure safe operation.
2. **Quality Assurance**: Compliance with standards ensures consistent quality and performance of components.
3. **Market Acceptance**: Products that meet recognized standards are more likely to be accepted in the marketplace.
C. Key Organizations Involved in Setting Standards
Several organizations play a significant role in developing and maintaining product standards for capacitors:
1. **International Electrotechnical Commission (IEC)**: Develops international standards for electrical and electronic technologies.
2. **Institute of Electrical and Electronics Engineers (IEEE)**: Focuses on standards for electrical and electronic engineering.
3. **Underwriters Laboratories (UL)**: Provides safety certification and standards for various electrical products.
4. **American National Standards Institute (ANSI)**: Oversees the development of voluntary consensus standards for products in the U.S.
IV. Key Standards for Capacitors
A. IEC Standards
1. **IEC 60384**: This standard covers fixed capacitors for use in electronic equipment, specifying requirements for performance, safety, and testing.
2. **IEC 61071**: This standard addresses capacitors for power electronics, focusing on their performance in high-voltage applications.
B. IEEE Standards
1. **IEEE 18**: This standard outlines the measurement of capacitance, providing guidelines for accurate testing methods.
2. **IEEE 519**: This standard offers recommended practices and requirements for harmonic control in electrical systems, which often involve capacitors.
C. UL Standards
1. **UL 1414**: This standard specifies safety requirements for capacitors, ensuring they can operate safely under specified conditions.
2. **UL 810**: This standard covers capacitors for use in electronic circuits, focusing on safety and performance criteria.
D. ANSI Standards
1. **ANSI C37.99**: This standard addresses capacitors in power systems, providing guidelines for their use and performance.
2. **ANSI/IEEE C57.12.01**: This standard covers transformers and capacitors, ensuring compatibility and safety in electrical systems.
V. Technical Considerations for Parallel Capacitor Connections
A. Voltage Ratings and Derating Factors
When connecting capacitors in parallel, it is essential to consider their voltage ratings. Each capacitor should have a voltage rating that exceeds the maximum voltage in the circuit. Additionally, derating factors may be applied to account for temperature, frequency, and other operating conditions to ensure reliability.
B. Capacitance Values and Tolerance Levels
Capacitance values and their tolerances are critical in parallel connections. Engineers must select capacitors with appropriate capacitance values to achieve the desired total capacitance while considering the tolerance levels to ensure performance within acceptable limits.
C. Equivalent Series Resistance (ESR) and Equivalent Series Inductance (ESL)
ESR and ESL are important parameters that affect the performance of capacitors in parallel connections. Low ESR is desirable for minimizing power losses, while low ESL is essential for high-frequency applications. Engineers should consider these factors when selecting capacitors for parallel configurations.
D. Temperature Coefficients and Their Impact on Performance
Temperature coefficients indicate how a capacitor's capacitance changes with temperature. Understanding these coefficients is crucial for ensuring stable performance across varying operating conditions, especially in applications where temperature fluctuations are common.
E. Safety Considerations and Failure Modes
Safety is paramount when working with capacitors. Engineers must be aware of potential failure modes, such as dielectric breakdown or thermal runaway, and design circuits to mitigate these risks. Proper fusing and circuit protection can help prevent catastrophic failures.
VI. Testing and Quality Assurance
A. Importance of Testing in Ensuring Compliance with Standards
Testing is essential to ensure that capacitors meet the required product standards. Regular testing helps identify potential issues early in the manufacturing process, ensuring that only compliant products reach the market.
B. Common Testing Methods for Capacitors
1. **Capacitance Measurement**: This method verifies the capacitance value against specified tolerances.
2. **Insulation Resistance Testing**: This test assesses the insulation quality of capacitors, ensuring they can withstand operating voltages without leakage.
3. **Dielectric Strength Testing**: This test evaluates the capacitor's ability to withstand high voltages without breakdown.
C. Quality Assurance Processes in Manufacturing
Manufacturers must implement robust quality assurance processes to ensure compliance with standards. This includes regular audits, process control, and documentation to track compliance throughout the production cycle.
VII. Challenges and Best Practices
A. Common Challenges in Parallel Capacitor Connections
1. **Balancing Capacitance Values**: Achieving the desired total capacitance while balancing individual capacitor values can be challenging.
2. **Managing Heat Dissipation**: Parallel connections can lead to increased heat generation, requiring careful thermal management to prevent overheating.
B. Best Practices for Designing and Implementing Parallel Capacitor Connections
1. **Selecting Appropriate Capacitors**: Choose capacitors with suitable voltage ratings, capacitance values, and performance characteristics for the application.
2. **Ensuring Proper Layout and Connections**: Design the circuit layout to minimize inductance and resistance, ensuring efficient operation.
3. **Regular Maintenance and Monitoring**: Implement a maintenance schedule to monitor capacitor performance and replace components as needed.
VIII. Conclusion
Understanding product standards for capacitor parallel connections is essential for ensuring safety, reliability, and performance in electrical circuits. By adhering to established standards and considering technical factors, engineers can design effective capacitor configurations that meet the demands of modern applications. As technology evolves, staying informed about emerging trends and best practices will be crucial for continued success in the field of electronics.
IX. References
1. IEC 60384 - Fixed capacitors for use in electronic equipment.
2. IEC 61071 - Capacitors for power electronics.
3. IEEE 18 - Standard for the measurement of capacitance.
4. IEEE 519 - Recommended practices and requirements for harmonic control.
5. UL 1414 - Standard for capacitors.
6. UL 810 - Standard for capacitors for use in electronic circuits.
7. ANSI C37.99 - Standard for capacitors in power systems.
8. ANSI/IEEE C57.12.01 - Standard for transformers and capacitors.
This comprehensive overview of product standards for capacitor parallel connections provides valuable insights for engineers and designers, ensuring they can navigate the complexities of capacitor technology effectively.
What are the Product Standards for Capacitor Parallel Connection?
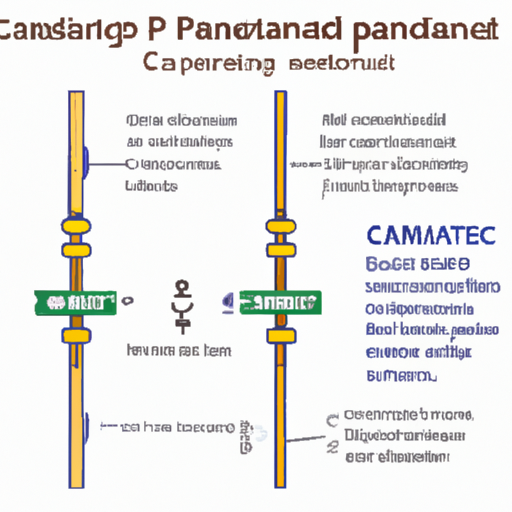
I. Introduction
Capacitors are fundamental components in electrical circuits, serving various roles such as energy storage, filtering, and signal coupling. Understanding the product standards for capacitor parallel connections is crucial for engineers and designers to ensure reliability, safety, and performance in their applications. This article will explore the basics of capacitor parallel connections, the relevant product standards, technical considerations, testing methods, challenges, and best practices.
II. Basics of Capacitor Parallel Connection
A. Explanation of Capacitor Parallel Connection
When capacitors are connected in parallel, their capacitance values add up, resulting in a total capacitance that is greater than any individual capacitor in the circuit. This configuration allows for increased energy storage and improved performance in various applications. In a parallel connection, the voltage across each capacitor remains the same, while the total current is the sum of the currents through each capacitor.
B. Advantages of Parallel Connections
The advantages of connecting capacitors in parallel include:
1. **Increased Capacitance**: The total capacitance increases, allowing for greater energy storage.
2. **Improved Reliability**: If one capacitor fails, the others can continue to function, enhancing the overall reliability of the circuit.
3. **Flexibility in Design**: Engineers can mix and match capacitors with different values and characteristics to achieve desired performance.
C. Common Applications of Parallel Capacitor Connections
Parallel capacitor connections are widely used in various applications, including:
1. **Power Factor Correction**: Capacitors are used to improve the power factor in electrical systems, reducing energy losses and improving efficiency.
2. **Energy Storage**: In power electronics, capacitors store energy for later use, smoothing out voltage fluctuations.
3. **Signal Coupling and Decoupling**: Capacitors help filter out noise and stabilize voltage levels in signal processing applications.
III. Product Standards Overview
A. Definition of Product Standards in Electronics
Product standards in electronics are established guidelines that ensure the safety, reliability, and performance of electronic components, including capacitors. These standards are developed by various organizations and are essential for manufacturers, engineers, and consumers.
B. Importance of Adhering to Product Standards
Adhering to product standards is vital for several reasons:
1. **Safety**: Standards help prevent electrical hazards and ensure safe operation.
2. **Quality Assurance**: Compliance with standards ensures consistent quality and performance of components.
3. **Market Acceptance**: Products that meet recognized standards are more likely to be accepted in the marketplace.
C. Key Organizations Involved in Setting Standards
Several organizations play a significant role in developing and maintaining product standards for capacitors:
1. **International Electrotechnical Commission (IEC)**: Develops international standards for electrical and electronic technologies.
2. **Institute of Electrical and Electronics Engineers (IEEE)**: Focuses on standards for electrical and electronic engineering.
3. **Underwriters Laboratories (UL)**: Provides safety certification and standards for various electrical products.
4. **American National Standards Institute (ANSI)**: Oversees the development of voluntary consensus standards for products in the U.S.
IV. Key Standards for Capacitors
A. IEC Standards
1. **IEC 60384**: This standard covers fixed capacitors for use in electronic equipment, specifying requirements for performance, safety, and testing.
2. **IEC 61071**: This standard addresses capacitors for power electronics, focusing on their performance in high-voltage applications.
B. IEEE Standards
1. **IEEE 18**: This standard outlines the measurement of capacitance, providing guidelines for accurate testing methods.
2. **IEEE 519**: This standard offers recommended practices and requirements for harmonic control in electrical systems, which often involve capacitors.
C. UL Standards
1. **UL 1414**: This standard specifies safety requirements for capacitors, ensuring they can operate safely under specified conditions.
2. **UL 810**: This standard covers capacitors for use in electronic circuits, focusing on safety and performance criteria.
D. ANSI Standards
1. **ANSI C37.99**: This standard addresses capacitors in power systems, providing guidelines for their use and performance.
2. **ANSI/IEEE C57.12.01**: This standard covers transformers and capacitors, ensuring compatibility and safety in electrical systems.
V. Technical Considerations for Parallel Capacitor Connections
A. Voltage Ratings and Derating Factors
When connecting capacitors in parallel, it is essential to consider their voltage ratings. Each capacitor should have a voltage rating that exceeds the maximum voltage in the circuit. Additionally, derating factors may be applied to account for temperature, frequency, and other operating conditions to ensure reliability.
B. Capacitance Values and Tolerance Levels
Capacitance values and their tolerances are critical in parallel connections. Engineers must select capacitors with appropriate capacitance values to achieve the desired total capacitance while considering the tolerance levels to ensure performance within acceptable limits.
C. Equivalent Series Resistance (ESR) and Equivalent Series Inductance (ESL)
ESR and ESL are important parameters that affect the performance of capacitors in parallel connections. Low ESR is desirable for minimizing power losses, while low ESL is essential for high-frequency applications. Engineers should consider these factors when selecting capacitors for parallel configurations.
D. Temperature Coefficients and Their Impact on Performance
Temperature coefficients indicate how a capacitor's capacitance changes with temperature. Understanding these coefficients is crucial for ensuring stable performance across varying operating conditions, especially in applications where temperature fluctuations are common.
E. Safety Considerations and Failure Modes
Safety is paramount when working with capacitors. Engineers must be aware of potential failure modes, such as dielectric breakdown or thermal runaway, and design circuits to mitigate these risks. Proper fusing and circuit protection can help prevent catastrophic failures.
VI. Testing and Quality Assurance
A. Importance of Testing in Ensuring Compliance with Standards
Testing is essential to ensure that capacitors meet the required product standards. Regular testing helps identify potential issues early in the manufacturing process, ensuring that only compliant products reach the market.
B. Common Testing Methods for Capacitors
1. **Capacitance Measurement**: This method verifies the capacitance value against specified tolerances.
2. **Insulation Resistance Testing**: This test assesses the insulation quality of capacitors, ensuring they can withstand operating voltages without leakage.
3. **Dielectric Strength Testing**: This test evaluates the capacitor's ability to withstand high voltages without breakdown.
C. Quality Assurance Processes in Manufacturing
Manufacturers must implement robust quality assurance processes to ensure compliance with standards. This includes regular audits, process control, and documentation to track compliance throughout the production cycle.
VII. Challenges and Best Practices
A. Common Challenges in Parallel Capacitor Connections
1. **Balancing Capacitance Values**: Achieving the desired total capacitance while balancing individual capacitor values can be challenging.
2. **Managing Heat Dissipation**: Parallel connections can lead to increased heat generation, requiring careful thermal management to prevent overheating.
B. Best Practices for Designing and Implementing Parallel Capacitor Connections
1. **Selecting Appropriate Capacitors**: Choose capacitors with suitable voltage ratings, capacitance values, and performance characteristics for the application.
2. **Ensuring Proper Layout and Connections**: Design the circuit layout to minimize inductance and resistance, ensuring efficient operation.
3. **Regular Maintenance and Monitoring**: Implement a maintenance schedule to monitor capacitor performance and replace components as needed.
VIII. Conclusion
Understanding product standards for capacitor parallel connections is essential for ensuring safety, reliability, and performance in electrical circuits. By adhering to established standards and considering technical factors, engineers can design effective capacitor configurations that meet the demands of modern applications. As technology evolves, staying informed about emerging trends and best practices will be crucial for continued success in the field of electronics.
IX. References
1. IEC 60384 - Fixed capacitors for use in electronic equipment.
2. IEC 61071 - Capacitors for power electronics.
3. IEEE 18 - Standard for the measurement of capacitance.
4. IEEE 519 - Recommended practices and requirements for harmonic control.
5. UL 1414 - Standard for capacitors.
6. UL 810 - Standard for capacitors for use in electronic circuits.
7. ANSI C37.99 - Standard for capacitors in power systems.
8. ANSI/IEEE C57.12.01 - Standard for transformers and capacitors.
This comprehensive overview of product standards for capacitor parallel connections provides valuable insights for engineers and designers, ensuring they can navigate the complexities of capacitor technology effectively.