The Production Process of Mainstream Capacitor Voltage
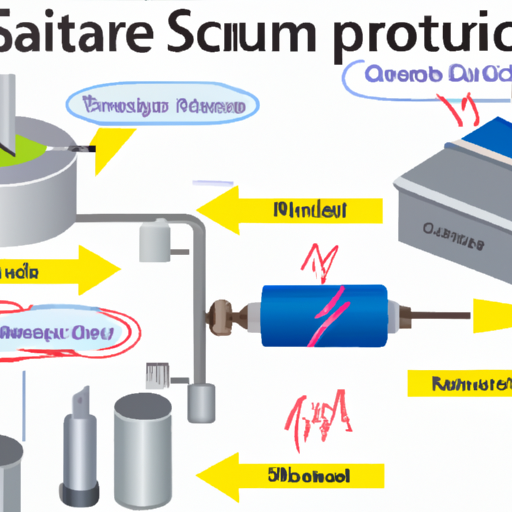
I. Introduction
Capacitors are fundamental components in electronic circuits, serving as energy storage devices that can release energy quickly when needed. They play a crucial role in various applications, from smoothing out voltage fluctuations in power supplies to enabling signal processing in communication devices. Understanding capacitor voltage is essential, as it determines the maximum voltage a capacitor can handle before failure. This article aims to explore the production process of mainstream capacitors, shedding light on the materials, techniques, and quality control measures involved in their manufacturing.
II. Types of Capacitors
Capacitors come in various types, each suited for specific applications based on their characteristics. The most common types include:
1. **Ceramic Capacitors**: Known for their small size and high stability, ceramic capacitors are widely used in high-frequency applications.
2. **Electrolytic Capacitors**: These capacitors offer high capacitance values and are often used in power supply circuits.
3. **Film Capacitors**: Made from plastic films, these capacitors are known for their reliability and low loss, making them suitable for audio and RF applications.
4. **Tantalum Capacitors**: With a high capacitance-to-volume ratio, tantalum capacitors are used in compact electronic devices.
This article will focus on the production processes of these mainstream capacitors, which are integral to modern electronics.
III. Raw Materials Used in Capacitor Production
The production of capacitors begins with the selection of raw materials, which significantly influence their performance and reliability.
A. Dielectric Materials
Dielectrics are insulating materials that store electrical energy in a capacitor. The choice of dielectric material affects the capacitor's capacitance, voltage rating, and temperature stability. Common types of dielectrics include:
Ceramic: Used in ceramic capacitors, offering high dielectric strength and stability.
Polymer: Found in film capacitors, providing excellent performance in various conditions.
Electrolytic: Used in electrolytic capacitors, where a liquid electrolyte serves as the dielectric.
B. Conductive Materials
Conductive materials are essential for the electrodes of capacitors. The most commonly used metals include:
Aluminum: Widely used in electrolytic capacitors due to its good conductivity and cost-effectiveness.
Tantalum: Known for its high capacitance and reliability, used in tantalum capacitors.
Copper: Often used in film capacitors for its excellent conductivity.
C. Other Materials
In addition to dielectrics and conductors, other materials play a role in capacitor production:
Insulating Materials: Used to prevent electrical leakage and ensure safety.
Packaging Materials: Essential for protecting capacitors during storage and transportation.
IV. The Production Process of Capacitors
The production of capacitors involves several key steps, from design to assembly.
A. Design and Engineering
The production process begins with design and engineering, where initial considerations include the capacitor's intended application, required specifications, and performance characteristics. Engineers use simulation and modeling tools to predict how the capacitor will perform under various conditions, ensuring that the final product meets the necessary standards.
B. Material Preparation
Once the design is finalized, the next step is material preparation. This involves sourcing high-quality raw materials and conducting quality control checks to ensure they meet specifications. Pre-processing may include powdering and mixing materials to achieve the desired properties.
C. Fabrication Techniques
The fabrication of capacitors varies depending on the type being produced:
1. **Ceramic Capacitors**:
- **Powder Pressing and Sintering**: Ceramic powders are pressed into shape and then sintered at high temperatures to form a solid dielectric.
- **Electrode Application**: Conductive layers are applied to the ceramic body, typically using screen printing or sputtering techniques.
2. **Electrolytic Capacitors**:
- **Anodization Process**: Aluminum foils are anodized to create a thin oxide layer that acts as the dielectric.
- **Electrolyte Filling**: The capacitor is filled with an electrolyte solution, which enhances its capacitance.
3. **Film Capacitors**:
- **Film Extrusion and Metallization**: Plastic films are extruded and then metallized to form the electrodes.
- **Winding and Cutting**: The metallized film is wound into a cylindrical shape and cut to the desired size.
4. **Tantalum Capacitors**:
- **Tantalum Powder Preparation**: Tantalum powder is prepared and compacted to form the capacitor's anode.
- **Sintering and Electrode Formation**: The compacted powder is sintered, and a dielectric layer is formed through anodization.
D. Assembly and Packaging
After fabrication, the components are assembled into finished capacitors. This process includes:
Component Assembly: The dielectric and electrodes are combined, and any additional components are added.
Quality Assurance and Testing: Each capacitor undergoes rigorous testing to ensure it meets performance specifications.
Packaging for Distribution: Finally, capacitors are packaged to protect them during transportation and storage.
V. Quality Control and Testing
Quality control is a critical aspect of capacitor production, ensuring that each component meets the required standards for performance and reliability.
A. Importance of Quality Control
Quality control helps prevent defects that could lead to capacitor failure in electronic circuits. Manufacturers implement strict quality assurance protocols throughout the production process.
B. Testing Methods
Various testing methods are employed to evaluate capacitor performance:
1. **Electrical Testing**: This includes measuring capacitance, equivalent series resistance (ESR), and voltage rating to ensure the capacitor functions as intended.
2. **Environmental Testing**: Capacitors are subjected to temperature and humidity tests to assess their performance under different conditions.
3. **Reliability Testing**: Long-term reliability is evaluated through lifetime testing and failure rate analysis, ensuring that capacitors can withstand the rigors of their intended applications.
VI. Environmental Considerations
As the electronics industry evolves, so do the environmental considerations surrounding capacitor production.
A. Sustainability in Capacitor Production
Manufacturers are increasingly focusing on sustainable practices, such as reducing waste and energy consumption during production. This includes optimizing processes and sourcing materials responsibly.
B. Recycling and Disposal of Capacitors
Proper recycling and disposal of capacitors are essential to minimize environmental impact. Many manufacturers are developing programs to recycle old capacitors and recover valuable materials.
C. Regulations and Standards Affecting Production
Regulatory bodies impose standards on capacitor production to ensure safety and environmental compliance. Manufacturers must adhere to these regulations to maintain their market position.
VII. Future Trends in Capacitor Technology
The capacitor industry is poised for significant advancements as technology continues to evolve.
A. Innovations in Materials and Design
Research is ongoing to develop new materials that enhance capacitor performance, such as high-k dielectrics and advanced conductive materials. These innovations aim to improve energy density and reduce size.
B. The Impact of Emerging Technologies
Emerging technologies, such as electric vehicles and renewable energy systems, are driving demand for advanced capacitors. These applications require capacitors with higher energy storage capabilities and improved reliability.
C. Predictions for the Future of Capacitor Production
As the demand for electronic devices grows, the capacitor industry will likely see increased automation and efficiency in production processes. This will enable manufacturers to meet the rising demand while maintaining high-quality standards.
VIII. Conclusion
The production process of mainstream capacitors is a complex and multifaceted endeavor that involves careful consideration of materials, design, and quality control. Capacitors are vital components in modern electronics, enabling a wide range of applications from power supplies to communication devices. As technology continues to advance, the capacitor industry will evolve, embracing new materials and production techniques to meet the demands of the future.
IX. References
For further reading on capacitor technology and production processes, consider exploring the following resources:
1. "Capacitor Technology: A Comprehensive Guide" - Journal of Electronic Materials
2. "Advancements in Capacitor Design and Manufacturing" - IEEE Transactions on Industrial Electronics
3. "Sustainable Practices in Electronics Manufacturing" - Environmental Science & Technology
This blog post provides an in-depth look at the production process of mainstream capacitors, highlighting the importance of these components in the ever-evolving landscape of electronics.
The Production Process of Mainstream Capacitor Voltage
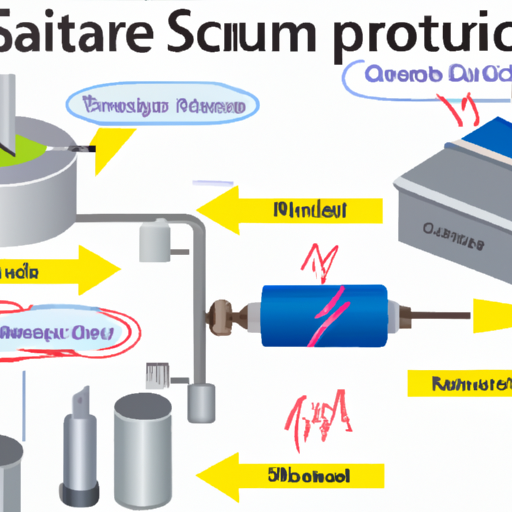
I. Introduction
Capacitors are fundamental components in electronic circuits, serving as energy storage devices that can release energy quickly when needed. They play a crucial role in various applications, from smoothing out voltage fluctuations in power supplies to enabling signal processing in communication devices. Understanding capacitor voltage is essential, as it determines the maximum voltage a capacitor can handle before failure. This article aims to explore the production process of mainstream capacitors, shedding light on the materials, techniques, and quality control measures involved in their manufacturing.
II. Types of Capacitors
Capacitors come in various types, each suited for specific applications based on their characteristics. The most common types include:
1. **Ceramic Capacitors**: Known for their small size and high stability, ceramic capacitors are widely used in high-frequency applications.
2. **Electrolytic Capacitors**: These capacitors offer high capacitance values and are often used in power supply circuits.
3. **Film Capacitors**: Made from plastic films, these capacitors are known for their reliability and low loss, making them suitable for audio and RF applications.
4. **Tantalum Capacitors**: With a high capacitance-to-volume ratio, tantalum capacitors are used in compact electronic devices.
This article will focus on the production processes of these mainstream capacitors, which are integral to modern electronics.
III. Raw Materials Used in Capacitor Production
The production of capacitors begins with the selection of raw materials, which significantly influence their performance and reliability.
A. Dielectric Materials
Dielectrics are insulating materials that store electrical energy in a capacitor. The choice of dielectric material affects the capacitor's capacitance, voltage rating, and temperature stability. Common types of dielectrics include:
Ceramic: Used in ceramic capacitors, offering high dielectric strength and stability.
Polymer: Found in film capacitors, providing excellent performance in various conditions.
Electrolytic: Used in electrolytic capacitors, where a liquid electrolyte serves as the dielectric.
B. Conductive Materials
Conductive materials are essential for the electrodes of capacitors. The most commonly used metals include:
Aluminum: Widely used in electrolytic capacitors due to its good conductivity and cost-effectiveness.
Tantalum: Known for its high capacitance and reliability, used in tantalum capacitors.
Copper: Often used in film capacitors for its excellent conductivity.
C. Other Materials
In addition to dielectrics and conductors, other materials play a role in capacitor production:
Insulating Materials: Used to prevent electrical leakage and ensure safety.
Packaging Materials: Essential for protecting capacitors during storage and transportation.
IV. The Production Process of Capacitors
The production of capacitors involves several key steps, from design to assembly.
A. Design and Engineering
The production process begins with design and engineering, where initial considerations include the capacitor's intended application, required specifications, and performance characteristics. Engineers use simulation and modeling tools to predict how the capacitor will perform under various conditions, ensuring that the final product meets the necessary standards.
B. Material Preparation
Once the design is finalized, the next step is material preparation. This involves sourcing high-quality raw materials and conducting quality control checks to ensure they meet specifications. Pre-processing may include powdering and mixing materials to achieve the desired properties.
C. Fabrication Techniques
The fabrication of capacitors varies depending on the type being produced:
1. **Ceramic Capacitors**:
- **Powder Pressing and Sintering**: Ceramic powders are pressed into shape and then sintered at high temperatures to form a solid dielectric.
- **Electrode Application**: Conductive layers are applied to the ceramic body, typically using screen printing or sputtering techniques.
2. **Electrolytic Capacitors**:
- **Anodization Process**: Aluminum foils are anodized to create a thin oxide layer that acts as the dielectric.
- **Electrolyte Filling**: The capacitor is filled with an electrolyte solution, which enhances its capacitance.
3. **Film Capacitors**:
- **Film Extrusion and Metallization**: Plastic films are extruded and then metallized to form the electrodes.
- **Winding and Cutting**: The metallized film is wound into a cylindrical shape and cut to the desired size.
4. **Tantalum Capacitors**:
- **Tantalum Powder Preparation**: Tantalum powder is prepared and compacted to form the capacitor's anode.
- **Sintering and Electrode Formation**: The compacted powder is sintered, and a dielectric layer is formed through anodization.
D. Assembly and Packaging
After fabrication, the components are assembled into finished capacitors. This process includes:
Component Assembly: The dielectric and electrodes are combined, and any additional components are added.
Quality Assurance and Testing: Each capacitor undergoes rigorous testing to ensure it meets performance specifications.
Packaging for Distribution: Finally, capacitors are packaged to protect them during transportation and storage.
V. Quality Control and Testing
Quality control is a critical aspect of capacitor production, ensuring that each component meets the required standards for performance and reliability.
A. Importance of Quality Control
Quality control helps prevent defects that could lead to capacitor failure in electronic circuits. Manufacturers implement strict quality assurance protocols throughout the production process.
B. Testing Methods
Various testing methods are employed to evaluate capacitor performance:
1. **Electrical Testing**: This includes measuring capacitance, equivalent series resistance (ESR), and voltage rating to ensure the capacitor functions as intended.
2. **Environmental Testing**: Capacitors are subjected to temperature and humidity tests to assess their performance under different conditions.
3. **Reliability Testing**: Long-term reliability is evaluated through lifetime testing and failure rate analysis, ensuring that capacitors can withstand the rigors of their intended applications.
VI. Environmental Considerations
As the electronics industry evolves, so do the environmental considerations surrounding capacitor production.
A. Sustainability in Capacitor Production
Manufacturers are increasingly focusing on sustainable practices, such as reducing waste and energy consumption during production. This includes optimizing processes and sourcing materials responsibly.
B. Recycling and Disposal of Capacitors
Proper recycling and disposal of capacitors are essential to minimize environmental impact. Many manufacturers are developing programs to recycle old capacitors and recover valuable materials.
C. Regulations and Standards Affecting Production
Regulatory bodies impose standards on capacitor production to ensure safety and environmental compliance. Manufacturers must adhere to these regulations to maintain their market position.
VII. Future Trends in Capacitor Technology
The capacitor industry is poised for significant advancements as technology continues to evolve.
A. Innovations in Materials and Design
Research is ongoing to develop new materials that enhance capacitor performance, such as high-k dielectrics and advanced conductive materials. These innovations aim to improve energy density and reduce size.
B. The Impact of Emerging Technologies
Emerging technologies, such as electric vehicles and renewable energy systems, are driving demand for advanced capacitors. These applications require capacitors with higher energy storage capabilities and improved reliability.
C. Predictions for the Future of Capacitor Production
As the demand for electronic devices grows, the capacitor industry will likely see increased automation and efficiency in production processes. This will enable manufacturers to meet the rising demand while maintaining high-quality standards.
VIII. Conclusion
The production process of mainstream capacitors is a complex and multifaceted endeavor that involves careful consideration of materials, design, and quality control. Capacitors are vital components in modern electronics, enabling a wide range of applications from power supplies to communication devices. As technology continues to advance, the capacitor industry will evolve, embracing new materials and production techniques to meet the demands of the future.
IX. References
For further reading on capacitor technology and production processes, consider exploring the following resources:
1. "Capacitor Technology: A Comprehensive Guide" - Journal of Electronic Materials
2. "Advancements in Capacitor Design and Manufacturing" - IEEE Transactions on Industrial Electronics
3. "Sustainable Practices in Electronics Manufacturing" - Environmental Science & Technology
This blog post provides an in-depth look at the production process of mainstream capacitors, highlighting the importance of these components in the ever-evolving landscape of electronics.