Common Production Processes for Thick Film Resistors
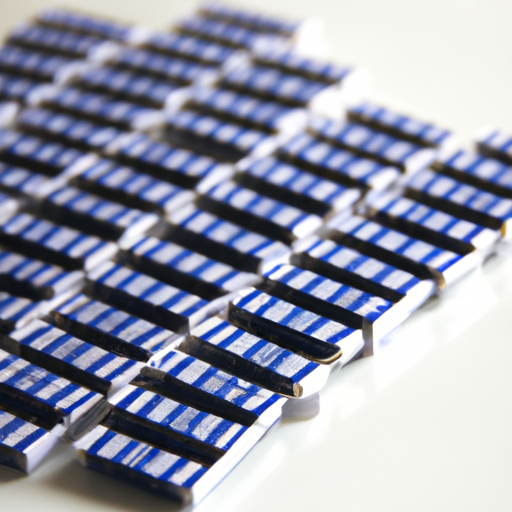
I. Introduction
Thick film resistors are essential components in modern electronic devices, playing a critical role in controlling current flow and ensuring circuit functionality. These resistors are characterized by their construction, which involves the application of a thick layer of resistive material onto a substrate. The importance of thick film resistors lies in their versatility, reliability, and ability to be produced in various configurations to meet specific application requirements. This blog post will explore the common production processes involved in creating thick film resistors, from material selection to final testing and packaging.
II. Materials Used in Thick Film Resistors
A. Conductive Materials
The performance of thick film resistors largely depends on the materials used in their construction. The primary conductive materials include metal pastes and carbon-based materials.
1. **Metal Pastes**: Silver, gold, and copper are commonly used metal pastes. Silver is favored for its excellent conductivity and stability, while gold is used in high-reliability applications due to its corrosion resistance. Copper, although less expensive, is often used in applications where cost is a significant factor.
2. **Carbon-Based Materials**: Carbon pastes are also utilized, particularly in applications requiring lower cost and higher temperature coefficients. These materials can provide a different set of electrical characteristics compared to metal pastes.
B. Dielectric Substrates
The choice of substrate is crucial for the performance of thick film resistors. Common substrate materials include alumina and glass.
1. **Common Substrate Materials**: Alumina (Al2O3) is widely used due to its excellent thermal and electrical insulation properties. Glass substrates are also popular, especially in applications requiring transparency or specific thermal characteristics.
2. **Importance of Substrate Properties**: The substrate must withstand the processing temperatures and provide a stable base for the resistive layer. Its thermal expansion coefficient should match that of the resistive material to prevent cracking during temperature fluctuations.
C. Additional Materials
In addition to conductive and dielectric materials, several other components are essential in the production of thick film resistors.
1. **Adhesives and Binders**: These materials help to adhere the resistive layer to the substrate and ensure durability during operation.
2. **Protective Coatings**: To enhance reliability, protective coatings are often applied to resistors to shield them from environmental factors such as moisture and dust.
III. Design and Preparation
A. Design Considerations
Before production begins, careful design considerations must be made to ensure the resistor meets the desired specifications.
1. **Resistance Value and Tolerance**: The design must specify the target resistance value and acceptable tolerance levels, which can vary based on application requirements.
2. **Temperature Coefficient of Resistance (TCR)**: The TCR is a critical parameter that indicates how the resistance changes with temperature. Designers must select materials that provide the desired TCR for the application.
B. Preparation of the Resistor Layout
The resistor layout is prepared using advanced design tools.
1. **CAD Software for Design**: Computer-Aided Design (CAD) software is employed to create precise layouts for the resistive tracks, ensuring accurate dimensions and configurations.
2. **Masking Techniques**: Masking techniques are used to define areas where the conductive paste will be applied, ensuring that the final product meets the design specifications.
IV. Screen Printing Process
A. Overview of Screen Printing
Screen printing is a widely used method for applying the conductive paste onto the substrate.
1. **Definition and Purpose**: This process involves pushing the conductive paste through a mesh screen onto the substrate, creating a uniform layer of resistive material.
2. **Equipment Used**: The primary equipment includes screens, squeegees, and a printing press, which work together to ensure consistent application.
B. Application of Conductive Paste
Achieving the desired layer thickness and uniformity is crucial during the screen printing process.
1. **Layer Thickness Control**: The thickness of the printed layer directly affects the resistance value. Careful control of the paste application is necessary to achieve the target specifications.
2. **Importance of Uniformity**: Uniformity in the application of the conductive paste is essential for consistent electrical performance across the resistor.
C. Drying and Curing
After printing, the resistive layer must be dried and cured to ensure proper adhesion and performance.
1. **Initial Drying Methods**: Initial drying can be achieved through air drying or using infrared heaters to remove solvents from the paste.
2. **Curing Processes**: Curing is typically performed in an oven at elevated temperatures, which helps to solidify the paste and enhance its electrical properties.
V. Laser Trimming
A. Purpose of Laser Trimming
Laser trimming is a critical step in achieving precise resistance values.
1. **Achieving Precise Resistance Values**: By selectively removing material from the resistive layer, manufacturers can fine-tune the resistance to meet exact specifications.
2. **Adjusting for Tolerance**: This process allows for adjustments to be made for tolerance, ensuring that the final product meets the required performance standards.
B. Laser Technology Used
The choice of laser technology is important for effective trimming.
1. **Types of Lasers**: CO2 and fiber lasers are commonly used for this purpose, each offering different advantages in terms of precision and speed.
2. **Process Parameters**: Key parameters such as laser power and speed must be carefully controlled to achieve the desired trimming results without damaging the substrate or the resistive layer.
VI. Testing and Quality Control
A. Electrical Testing
Quality control is essential to ensure that thick film resistors meet performance standards.
1. **Resistance Measurement Techniques**: Various techniques, such as four-wire measurement, are used to accurately assess the resistance of the finished product.
2. **TCR Testing**: Testing the temperature coefficient of resistance is also crucial to ensure that the resistor performs reliably across its operating temperature range.
B. Visual Inspection
Visual inspection plays a vital role in quality assurance.
1. **Checking for Defects**: Inspectors look for defects such as cracks, uneven layers, or contamination that could affect performance.
2. **Importance of Aesthetics in Applications**: In some applications, the appearance of the resistor may also be important, necessitating careful visual inspection.
C. Reliability Testing
To ensure long-term performance, reliability testing is conducted.
1. **Environmental Testing**: Resistors are subjected to various environmental conditions, including temperature and humidity, to assess their performance under real-world conditions.
2. **Long-Term Stability Assessments**: Long-term stability tests help to evaluate how the resistor will perform over time, ensuring that it meets the required lifespan.
VII. Packaging and Finalization
A. Packaging Options
Once testing is complete, the resistors must be packaged appropriately for distribution.
1. **Surface Mount vs. Through-Hole**: Thick film resistors can be packaged for surface mount technology (SMT) or through-hole applications, depending on the intended use.
2. **Protective Coatings and Encapsulation**: Additional protective coatings or encapsulation may be applied to enhance durability and protect against environmental factors.
B. Final Quality Assurance
Final quality assurance checks are performed before the resistors are shipped.
1. **Batch Testing**: Random samples from production batches are tested to ensure consistency and compliance with specifications.
2. **Compliance with Industry Standards**: Adherence to industry standards and guidelines is crucial for ensuring product reliability and safety.
VIII. Conclusion
In summary, the production processes for thick film resistors involve a series of carefully controlled steps, from material selection and design to testing and packaging. Each stage is critical to ensuring that the final product meets the required specifications and performs reliably in electronic applications. As technology continues to evolve, the demand for high-quality thick film resistors will only increase, driving innovations in production techniques and materials.
IX. References
For further exploration of thick film resistors and their production processes, consider the following resources:
- Books on electronic components and materials science
- Industry standards from organizations such as the International Electrotechnical Commission (IEC)
- Technical papers and articles from electronics journals and conferences
By understanding the intricacies of thick film resistor production, manufacturers can continue to meet the growing demands of the electronics industry while ensuring high-quality, reliable components.
Common Production Processes for Thick Film Resistors
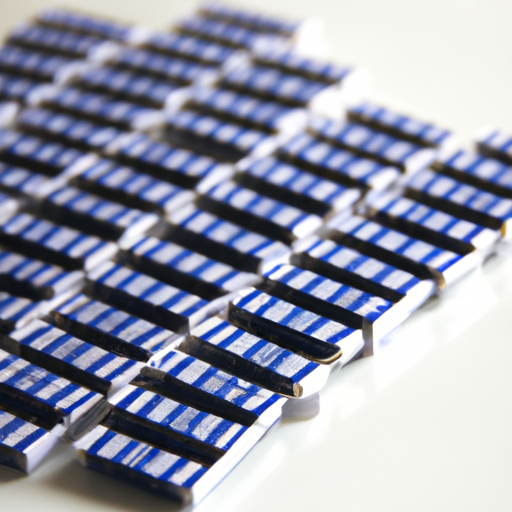
I. Introduction
Thick film resistors are essential components in modern electronic devices, playing a critical role in controlling current flow and ensuring circuit functionality. These resistors are characterized by their construction, which involves the application of a thick layer of resistive material onto a substrate. The importance of thick film resistors lies in their versatility, reliability, and ability to be produced in various configurations to meet specific application requirements. This blog post will explore the common production processes involved in creating thick film resistors, from material selection to final testing and packaging.
II. Materials Used in Thick Film Resistors
A. Conductive Materials
The performance of thick film resistors largely depends on the materials used in their construction. The primary conductive materials include metal pastes and carbon-based materials.
1. **Metal Pastes**: Silver, gold, and copper are commonly used metal pastes. Silver is favored for its excellent conductivity and stability, while gold is used in high-reliability applications due to its corrosion resistance. Copper, although less expensive, is often used in applications where cost is a significant factor.
2. **Carbon-Based Materials**: Carbon pastes are also utilized, particularly in applications requiring lower cost and higher temperature coefficients. These materials can provide a different set of electrical characteristics compared to metal pastes.
B. Dielectric Substrates
The choice of substrate is crucial for the performance of thick film resistors. Common substrate materials include alumina and glass.
1. **Common Substrate Materials**: Alumina (Al2O3) is widely used due to its excellent thermal and electrical insulation properties. Glass substrates are also popular, especially in applications requiring transparency or specific thermal characteristics.
2. **Importance of Substrate Properties**: The substrate must withstand the processing temperatures and provide a stable base for the resistive layer. Its thermal expansion coefficient should match that of the resistive material to prevent cracking during temperature fluctuations.
C. Additional Materials
In addition to conductive and dielectric materials, several other components are essential in the production of thick film resistors.
1. **Adhesives and Binders**: These materials help to adhere the resistive layer to the substrate and ensure durability during operation.
2. **Protective Coatings**: To enhance reliability, protective coatings are often applied to resistors to shield them from environmental factors such as moisture and dust.
III. Design and Preparation
A. Design Considerations
Before production begins, careful design considerations must be made to ensure the resistor meets the desired specifications.
1. **Resistance Value and Tolerance**: The design must specify the target resistance value and acceptable tolerance levels, which can vary based on application requirements.
2. **Temperature Coefficient of Resistance (TCR)**: The TCR is a critical parameter that indicates how the resistance changes with temperature. Designers must select materials that provide the desired TCR for the application.
B. Preparation of the Resistor Layout
The resistor layout is prepared using advanced design tools.
1. **CAD Software for Design**: Computer-Aided Design (CAD) software is employed to create precise layouts for the resistive tracks, ensuring accurate dimensions and configurations.
2. **Masking Techniques**: Masking techniques are used to define areas where the conductive paste will be applied, ensuring that the final product meets the design specifications.
IV. Screen Printing Process
A. Overview of Screen Printing
Screen printing is a widely used method for applying the conductive paste onto the substrate.
1. **Definition and Purpose**: This process involves pushing the conductive paste through a mesh screen onto the substrate, creating a uniform layer of resistive material.
2. **Equipment Used**: The primary equipment includes screens, squeegees, and a printing press, which work together to ensure consistent application.
B. Application of Conductive Paste
Achieving the desired layer thickness and uniformity is crucial during the screen printing process.
1. **Layer Thickness Control**: The thickness of the printed layer directly affects the resistance value. Careful control of the paste application is necessary to achieve the target specifications.
2. **Importance of Uniformity**: Uniformity in the application of the conductive paste is essential for consistent electrical performance across the resistor.
C. Drying and Curing
After printing, the resistive layer must be dried and cured to ensure proper adhesion and performance.
1. **Initial Drying Methods**: Initial drying can be achieved through air drying or using infrared heaters to remove solvents from the paste.
2. **Curing Processes**: Curing is typically performed in an oven at elevated temperatures, which helps to solidify the paste and enhance its electrical properties.
V. Laser Trimming
A. Purpose of Laser Trimming
Laser trimming is a critical step in achieving precise resistance values.
1. **Achieving Precise Resistance Values**: By selectively removing material from the resistive layer, manufacturers can fine-tune the resistance to meet exact specifications.
2. **Adjusting for Tolerance**: This process allows for adjustments to be made for tolerance, ensuring that the final product meets the required performance standards.
B. Laser Technology Used
The choice of laser technology is important for effective trimming.
1. **Types of Lasers**: CO2 and fiber lasers are commonly used for this purpose, each offering different advantages in terms of precision and speed.
2. **Process Parameters**: Key parameters such as laser power and speed must be carefully controlled to achieve the desired trimming results without damaging the substrate or the resistive layer.
VI. Testing and Quality Control
A. Electrical Testing
Quality control is essential to ensure that thick film resistors meet performance standards.
1. **Resistance Measurement Techniques**: Various techniques, such as four-wire measurement, are used to accurately assess the resistance of the finished product.
2. **TCR Testing**: Testing the temperature coefficient of resistance is also crucial to ensure that the resistor performs reliably across its operating temperature range.
B. Visual Inspection
Visual inspection plays a vital role in quality assurance.
1. **Checking for Defects**: Inspectors look for defects such as cracks, uneven layers, or contamination that could affect performance.
2. **Importance of Aesthetics in Applications**: In some applications, the appearance of the resistor may also be important, necessitating careful visual inspection.
C. Reliability Testing
To ensure long-term performance, reliability testing is conducted.
1. **Environmental Testing**: Resistors are subjected to various environmental conditions, including temperature and humidity, to assess their performance under real-world conditions.
2. **Long-Term Stability Assessments**: Long-term stability tests help to evaluate how the resistor will perform over time, ensuring that it meets the required lifespan.
VII. Packaging and Finalization
A. Packaging Options
Once testing is complete, the resistors must be packaged appropriately for distribution.
1. **Surface Mount vs. Through-Hole**: Thick film resistors can be packaged for surface mount technology (SMT) or through-hole applications, depending on the intended use.
2. **Protective Coatings and Encapsulation**: Additional protective coatings or encapsulation may be applied to enhance durability and protect against environmental factors.
B. Final Quality Assurance
Final quality assurance checks are performed before the resistors are shipped.
1. **Batch Testing**: Random samples from production batches are tested to ensure consistency and compliance with specifications.
2. **Compliance with Industry Standards**: Adherence to industry standards and guidelines is crucial for ensuring product reliability and safety.
VIII. Conclusion
In summary, the production processes for thick film resistors involve a series of carefully controlled steps, from material selection and design to testing and packaging. Each stage is critical to ensuring that the final product meets the required specifications and performs reliably in electronic applications. As technology continues to evolve, the demand for high-quality thick film resistors will only increase, driving innovations in production techniques and materials.
IX. References
For further exploration of thick film resistors and their production processes, consider the following resources:
- Books on electronic components and materials science
- Industry standards from organizations such as the International Electrotechnical Commission (IEC)
- Technical papers and articles from electronics journals and conferences
By understanding the intricacies of thick film resistor production, manufacturers can continue to meet the growing demands of the electronics industry while ensuring high-quality, reliable components.