What is the Mainstream Precision Resistor Production Process?
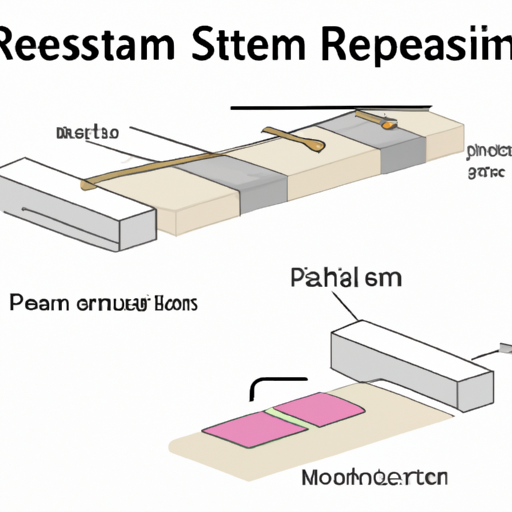
I. Introduction
Precision resistors are critical components in electronic circuits, providing accurate resistance values essential for the proper functioning of various devices. Defined as resistors with a tolerance of 1% or less, precision resistors are used in applications where accuracy and stability are paramount, such as in measurement instruments, medical devices, and aerospace technology. The production of these resistors involves a meticulous process that ensures their reliability and performance. This blog post will explore the mainstream precision resistor production process, detailing the types of resistors, raw materials, fabrication techniques, and innovations shaping the industry.
II. Types of Precision Resistors
A. Thin-Film Resistors
Thin-film resistors are made by depositing a thin layer of resistive material onto a substrate. They are known for their high accuracy, low temperature coefficient, and excellent stability. Common applications include precision measurement devices and high-frequency circuits.
B. Thick-Film Resistors
Thick-film resistors are produced by printing a paste of resistive material onto a substrate and then firing it to create a thick layer. These resistors are more robust than thin-film types and are often used in power applications, automotive electronics, and consumer devices.
C. Wire-Wound Resistors
Wire-wound resistors consist of a wire, typically made of a high-resistance alloy, wound around a core. They offer high precision and power handling capabilities, making them suitable for applications in power supplies and audio equipment.
D. Comparison of Different Types
While thin-film resistors excel in precision and stability, thick-film resistors are favored for their durability and cost-effectiveness. Wire-wound resistors, on the other hand, provide high power ratings but may not be as compact as the other types. The choice of resistor type depends on the specific requirements of the application.
III. Raw Materials Used in Precision Resistor Production
A. Conductive Materials
The choice of conductive materials is crucial in precision resistor production. Common materials include:
1. **Metal Films**: Metals like nickel, gold, and tantalum are often used in thin-film resistors due to their excellent conductivity and stability.
2. **Carbon-Based Materials**: Carbon compositions are frequently used in thick-film resistors for their cost-effectiveness and good thermal stability.
B. Substrates
The substrate provides the foundation for the resistor and influences its performance. Common substrates include:
1. **Ceramic**: Known for its thermal stability and electrical insulation properties, ceramic is widely used in both thin and thick-film resistors.
2. **Glass**: Glass substrates offer excellent insulation and are often used in high-temperature applications.
3. **Polymer**: Flexible polymer substrates are increasingly used in modern electronics, especially in applications requiring lightweight and compact designs.
C. Insulating Materials
Insulating materials are essential for preventing unwanted current flow and ensuring the reliability of precision resistors. Common insulating materials include:
1. **Epoxy Resins**: These are used for encapsulating resistors, providing protection against environmental factors.
2. **Other Dielectric Materials**: Various dielectric materials are employed to enhance the electrical insulation properties of resistors.
IV. The Production Process
A. Design and Engineering
The production of precision resistors begins with design and engineering. This phase involves defining specifications and requirements based on the intended application. Engineers use simulation and modeling tools to predict the performance of the resistor under various conditions, ensuring that the final product meets the desired standards.
B. Material Preparation
Once the design is finalized, the next step is material preparation. This involves sourcing high-quality raw materials and conducting rigorous quality control checks. Pre-processing of materials, such as cleaning and conditioning, is also performed to ensure optimal performance during fabrication.
C. Fabrication Techniques
The fabrication of precision resistors involves several techniques, each tailored to the type of resistor being produced:
1. **Thin-Film Deposition**:
- **Sputtering**: A physical vapor deposition technique where atoms are ejected from a target material and deposited onto the substrate.
- **Evaporation**: A process where the resistive material is heated until it vaporizes and then condenses onto the substrate.
2. **Thick-Film Printing**:
- **Screen Printing**: A method where a paste of resistive material is pushed through a mesh screen onto the substrate.
- **Inkjet Printing**: A more modern technique that allows for precise deposition of resistive inks onto substrates.
3. **Wire-Wound Techniques**:
- **Winding Processes**: The wire is wound around a core in a controlled manner to achieve the desired resistance value.
- **Resistance Adjustment**: After winding, the resistance is fine-tuned through trimming or adjusting the length of the wire.
D. Assembly and Packaging
After fabrication, the resistors are assembled and packaged. This involves mounting the resistors onto substrates, followed by encapsulation to protect them from environmental factors such as moisture and dust. Proper packaging is crucial for maintaining the performance and longevity of precision resistors.
E. Testing and Quality Assurance
Quality assurance is a critical step in the production process. Each resistor undergoes rigorous testing, including:
1. **Electrical Testing**: Ensuring that the resistor meets its specified resistance value and tolerance.
2. **Environmental Testing**: Assessing the resistor's performance under various environmental conditions, such as temperature and humidity.
3. **Calibration and Certification**: Final calibration ensures that the resistors are accurate and reliable, often leading to certification for specific applications.
V. Innovations in Precision Resistor Production
A. Advances in Materials Science
Recent advancements in materials science have led to the development of new conductive and insulating materials that enhance the performance of precision resistors. These innovations allow for greater accuracy, stability, and miniaturization of resistors.
B. Automation and Industry 4.0
The integration of automation and Industry 4.0 technologies in the production process has significantly improved efficiency and consistency. Automated systems can monitor production in real-time, ensuring that quality standards are met and reducing the likelihood of human error.
C. Environmental Considerations and Sustainability
As the demand for sustainable manufacturing practices grows, the precision resistor industry is exploring eco-friendly materials and processes. This includes the use of recyclable materials and energy-efficient production techniques, contributing to a more sustainable future.
VI. Conclusion
The production of precision resistors is a complex process that requires careful consideration of materials, fabrication techniques, and quality assurance. As technology continues to advance, the precision resistor industry is poised for further innovations that will enhance performance and sustainability. Understanding the intricacies of this production process is essential for anyone involved in electronics, as precision resistors play a vital role in the advancement of technology.
VII. References
1. Academic journals on materials science and electronics.
2. Industry reports on precision resistor manufacturing trends.
3. Manufacturer specifications and guidelines for precision resistors.
In summary, the mainstream precision resistor production process is a blend of science, engineering, and innovation, ensuring that these critical components meet the ever-evolving demands of modern technology.
What is the Mainstream Precision Resistor Production Process?
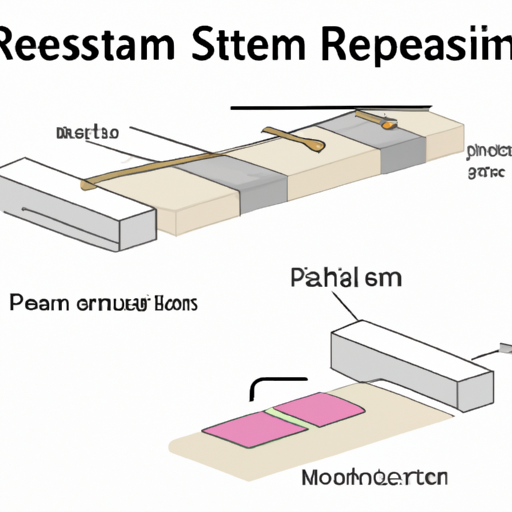
I. Introduction
Precision resistors are critical components in electronic circuits, providing accurate resistance values essential for the proper functioning of various devices. Defined as resistors with a tolerance of 1% or less, precision resistors are used in applications where accuracy and stability are paramount, such as in measurement instruments, medical devices, and aerospace technology. The production of these resistors involves a meticulous process that ensures their reliability and performance. This blog post will explore the mainstream precision resistor production process, detailing the types of resistors, raw materials, fabrication techniques, and innovations shaping the industry.
II. Types of Precision Resistors
A. Thin-Film Resistors
Thin-film resistors are made by depositing a thin layer of resistive material onto a substrate. They are known for their high accuracy, low temperature coefficient, and excellent stability. Common applications include precision measurement devices and high-frequency circuits.
B. Thick-Film Resistors
Thick-film resistors are produced by printing a paste of resistive material onto a substrate and then firing it to create a thick layer. These resistors are more robust than thin-film types and are often used in power applications, automotive electronics, and consumer devices.
C. Wire-Wound Resistors
Wire-wound resistors consist of a wire, typically made of a high-resistance alloy, wound around a core. They offer high precision and power handling capabilities, making them suitable for applications in power supplies and audio equipment.
D. Comparison of Different Types
While thin-film resistors excel in precision and stability, thick-film resistors are favored for their durability and cost-effectiveness. Wire-wound resistors, on the other hand, provide high power ratings but may not be as compact as the other types. The choice of resistor type depends on the specific requirements of the application.
III. Raw Materials Used in Precision Resistor Production
A. Conductive Materials
The choice of conductive materials is crucial in precision resistor production. Common materials include:
1. **Metal Films**: Metals like nickel, gold, and tantalum are often used in thin-film resistors due to their excellent conductivity and stability.
2. **Carbon-Based Materials**: Carbon compositions are frequently used in thick-film resistors for their cost-effectiveness and good thermal stability.
B. Substrates
The substrate provides the foundation for the resistor and influences its performance. Common substrates include:
1. **Ceramic**: Known for its thermal stability and electrical insulation properties, ceramic is widely used in both thin and thick-film resistors.
2. **Glass**: Glass substrates offer excellent insulation and are often used in high-temperature applications.
3. **Polymer**: Flexible polymer substrates are increasingly used in modern electronics, especially in applications requiring lightweight and compact designs.
C. Insulating Materials
Insulating materials are essential for preventing unwanted current flow and ensuring the reliability of precision resistors. Common insulating materials include:
1. **Epoxy Resins**: These are used for encapsulating resistors, providing protection against environmental factors.
2. **Other Dielectric Materials**: Various dielectric materials are employed to enhance the electrical insulation properties of resistors.
IV. The Production Process
A. Design and Engineering
The production of precision resistors begins with design and engineering. This phase involves defining specifications and requirements based on the intended application. Engineers use simulation and modeling tools to predict the performance of the resistor under various conditions, ensuring that the final product meets the desired standards.
B. Material Preparation
Once the design is finalized, the next step is material preparation. This involves sourcing high-quality raw materials and conducting rigorous quality control checks. Pre-processing of materials, such as cleaning and conditioning, is also performed to ensure optimal performance during fabrication.
C. Fabrication Techniques
The fabrication of precision resistors involves several techniques, each tailored to the type of resistor being produced:
1. **Thin-Film Deposition**:
- **Sputtering**: A physical vapor deposition technique where atoms are ejected from a target material and deposited onto the substrate.
- **Evaporation**: A process where the resistive material is heated until it vaporizes and then condenses onto the substrate.
2. **Thick-Film Printing**:
- **Screen Printing**: A method where a paste of resistive material is pushed through a mesh screen onto the substrate.
- **Inkjet Printing**: A more modern technique that allows for precise deposition of resistive inks onto substrates.
3. **Wire-Wound Techniques**:
- **Winding Processes**: The wire is wound around a core in a controlled manner to achieve the desired resistance value.
- **Resistance Adjustment**: After winding, the resistance is fine-tuned through trimming or adjusting the length of the wire.
D. Assembly and Packaging
After fabrication, the resistors are assembled and packaged. This involves mounting the resistors onto substrates, followed by encapsulation to protect them from environmental factors such as moisture and dust. Proper packaging is crucial for maintaining the performance and longevity of precision resistors.
E. Testing and Quality Assurance
Quality assurance is a critical step in the production process. Each resistor undergoes rigorous testing, including:
1. **Electrical Testing**: Ensuring that the resistor meets its specified resistance value and tolerance.
2. **Environmental Testing**: Assessing the resistor's performance under various environmental conditions, such as temperature and humidity.
3. **Calibration and Certification**: Final calibration ensures that the resistors are accurate and reliable, often leading to certification for specific applications.
V. Innovations in Precision Resistor Production
A. Advances in Materials Science
Recent advancements in materials science have led to the development of new conductive and insulating materials that enhance the performance of precision resistors. These innovations allow for greater accuracy, stability, and miniaturization of resistors.
B. Automation and Industry 4.0
The integration of automation and Industry 4.0 technologies in the production process has significantly improved efficiency and consistency. Automated systems can monitor production in real-time, ensuring that quality standards are met and reducing the likelihood of human error.
C. Environmental Considerations and Sustainability
As the demand for sustainable manufacturing practices grows, the precision resistor industry is exploring eco-friendly materials and processes. This includes the use of recyclable materials and energy-efficient production techniques, contributing to a more sustainable future.
VI. Conclusion
The production of precision resistors is a complex process that requires careful consideration of materials, fabrication techniques, and quality assurance. As technology continues to advance, the precision resistor industry is poised for further innovations that will enhance performance and sustainability. Understanding the intricacies of this production process is essential for anyone involved in electronics, as precision resistors play a vital role in the advancement of technology.
VII. References
1. Academic journals on materials science and electronics.
2. Industry reports on precision resistor manufacturing trends.
3. Manufacturer specifications and guidelines for precision resistors.
In summary, the mainstream precision resistor production process is a blend of science, engineering, and innovation, ensuring that these critical components meet the ever-evolving demands of modern technology.