Common Production Processes in Resistor Factories
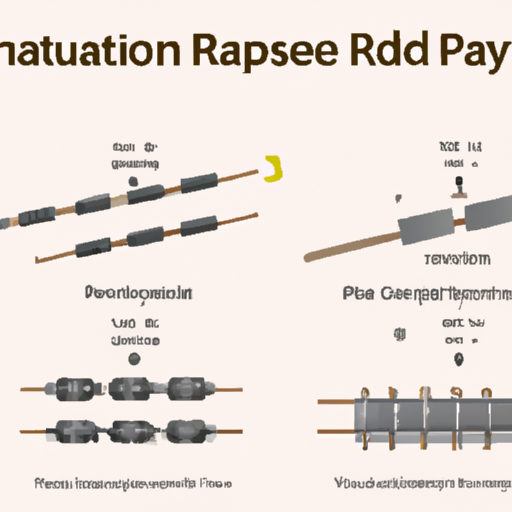
I. Introduction
Resistors are fundamental components in electronic circuits, playing a crucial role in controlling current flow and voltage levels. They are essential for the proper functioning of various electronic devices, from simple household appliances to complex industrial machinery. The manufacturing of resistors involves a series of intricate processes that ensure their reliability and performance. This article aims to explore the common production processes in resistor factories, shedding light on the methods and materials that contribute to the creation of these vital components.
II. Types of Resistors
Resistors come in various types, each designed for specific applications and performance characteristics. Understanding these types is essential for grasping the production processes involved.
A. Fixed Resistors
1. **Carbon Composition Resistors**: These resistors are made from a mixture of carbon particles and a binding material. They are known for their high energy absorption and are often used in applications where high pulse loads are expected.
2. **Metal Film Resistors**: Constructed from a thin layer of metal, these resistors offer high precision and stability. They are widely used in applications requiring accurate resistance values.
3. **Wirewound Resistors**: Made by winding a metal wire around a ceramic or fiberglass core, wirewound resistors are known for their high power ratings and are commonly used in power applications.
B. Variable Resistors
1. **Potentiometers**: These resistors allow for adjustable resistance and are often used in volume controls and tuning circuits.
2. **Rheostats**: Similar to potentiometers, rheostats are used to control current flow in a circuit, typically in higher power applications.
C. Specialty Resistors
1. **Thermistors**: These temperature-sensitive resistors are used in temperature sensing and control applications.
2. **Photoresistors**: Also known as light-dependent resistors (LDRs), these components change resistance based on light exposure, making them ideal for light-sensing applications.
III. Raw Materials Used in Resistor Production
The production of resistors requires a variety of raw materials, each contributing to the final product's performance and reliability.
A. Conductive Materials
1. **Carbon**: Used primarily in carbon composition resistors, carbon provides the necessary conductivity and resistance characteristics.
2. **Metal Oxides**: Commonly used in metal film resistors, metal oxides offer stability and precision in resistance values.
3. **Metal Wires**: Essential for wirewound resistors, metal wires (often made of nickel-chromium or copper) provide the necessary conductivity and durability.
B. Insulating Materials
1. **Ceramic Substrates**: These materials are used to provide insulation and mechanical support for resistors, particularly in wirewound designs.
2. **Epoxy Resins**: Used for coating and protecting resistors, epoxy resins offer excellent insulation properties and environmental resistance.
C. Other Components
1. **Lead Wires**: These are used to connect resistors to circuits, ensuring reliable electrical connections.
2. **Protective Coatings**: Coatings are applied to resistors to protect them from environmental factors and mechanical damage.
IV. Common Production Processes
The production of resistors involves several key processes, each critical to ensuring the quality and performance of the final product.
A. Material Preparation
1. **Sourcing and Quality Control of Raw Materials**: The first step in resistor production is sourcing high-quality raw materials. Manufacturers conduct rigorous quality control checks to ensure that materials meet specific standards.
2. **Pre-processing of Materials**: This may involve grinding carbon powder, mixing conductive materials, and preparing metal wires for further processing.
B. Resistor Element Fabrication
1. **Carbon Composition Resistors**:
- **Mixing Carbon Powder with a Binder**: The carbon powder is mixed with a binding agent to create a paste.
- **Molding and Curing**: The paste is molded into the desired shape and cured to harden the material.
2. **Metal Film Resistors**:
- **Thin Film Deposition Techniques**: Techniques such as sputtering or evaporation are used to deposit a thin layer of metal onto a substrate.
- **Laser Trimming for Precision**: After deposition, laser trimming is employed to achieve precise resistance values.
3. **Wirewound Resistors**:
- **Winding Wire Around a Core**: A metal wire is wound around a ceramic or fiberglass core to create the resistor element.
- **Insulation and Coating Application**: The wound resistor is then insulated and coated to protect it from environmental factors.
C. Assembly Process
1. **Mounting Resistor Elements onto Substrates**: The fabricated resistor elements are mounted onto insulating substrates, which provide mechanical support and electrical insulation.
2. **Soldering and Connecting Lead Wires**: Lead wires are soldered to the resistor elements, ensuring reliable electrical connections for integration into circuits.
D. Testing and Quality Control
1. **Electrical Testing**: Each resistor undergoes electrical testing to measure resistance values and ensure they meet specifications.
2. **Environmental Testing**: Resistors are subjected to environmental tests, including temperature and humidity exposure, to assess their performance under various conditions.
3. **Visual Inspection for Defects**: A thorough visual inspection is conducted to identify any defects or inconsistencies in the resistors.
E. Packaging and Distribution
1. **Packaging Methods**: Resistors are packaged using various methods, including bulk packaging and tape-and-reel systems for automated assembly lines.
2. **Logistics and Distribution Channels**: Efficient logistics and distribution channels are established to ensure timely delivery to customers and manufacturers.
V. Automation and Technology in Resistor Manufacturing
The resistor manufacturing industry has seen significant advancements in automation and technology, enhancing production efficiency and product quality.
A. Role of Automation in Production Efficiency
Automation plays a crucial role in streamlining production processes, reducing labor costs, and minimizing human error. Automated systems can handle repetitive tasks, allowing skilled workers to focus on more complex operations.
B. Advanced Technologies in Quality Control
Technologies such as robotics and artificial intelligence (AI) are increasingly being integrated into quality control processes. These technologies enable real-time monitoring and analysis, ensuring that any defects are identified and addressed promptly.
C. Future Trends in Resistor Manufacturing Processes
As the electronics industry continues to evolve, resistor manufacturing processes are expected to become more sophisticated. Trends such as the use of advanced materials, increased automation, and sustainable practices are likely to shape the future of resistor production.
VI. Environmental Considerations
The production of resistors also raises important environmental considerations that manufacturers must address.
A. Waste Management in Resistor Production
Effective waste management practices are essential to minimize the environmental impact of resistor manufacturing. This includes recycling materials and properly disposing of hazardous waste.
B. Sustainable Practices in Sourcing Materials
Manufacturers are increasingly focusing on sustainable sourcing practices, ensuring that raw materials are obtained responsibly and ethically.
C. Compliance with Environmental Regulations
Compliance with environmental regulations is critical for resistor manufacturers. Adhering to these regulations not only helps protect the environment but also enhances the company's reputation and marketability.
VII. Conclusion
Understanding the common production processes in resistor factories is essential for appreciating the complexity and importance of these components in electronic circuits. The manufacturing processes directly impact the quality and performance of resistors, influencing their reliability in various applications. As technology advances and environmental considerations become more prominent, the future of resistor manufacturing will likely see continued innovation and improvement, ensuring that these vital components meet the demands of the ever-evolving electronics industry.
VIII. References
For further exploration of resistor manufacturing processes, consider the following resources:
1. "Resistor Technology: A Comprehensive Guide" - A detailed book covering various aspects of resistor technology and manufacturing.
2. "The Electronics Handbook" - A reference book that includes information on electronic components, including resistors.
3. Industry journals and publications that focus on advancements in electronics manufacturing and materials science.
By delving into these resources, readers can gain a deeper understanding of the intricacies involved in resistor production and the broader context of electronic component manufacturing.
Common Production Processes in Resistor Factories
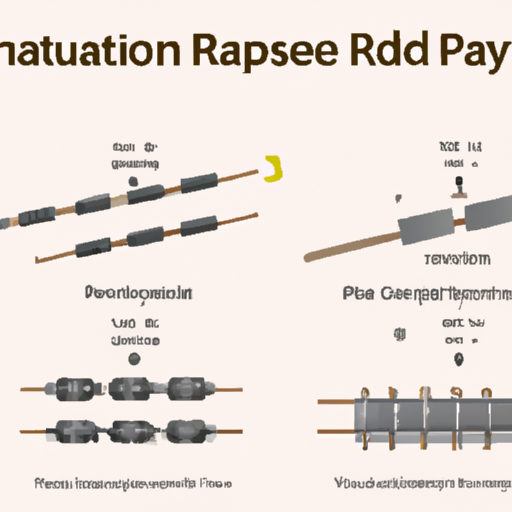
I. Introduction
Resistors are fundamental components in electronic circuits, playing a crucial role in controlling current flow and voltage levels. They are essential for the proper functioning of various electronic devices, from simple household appliances to complex industrial machinery. The manufacturing of resistors involves a series of intricate processes that ensure their reliability and performance. This article aims to explore the common production processes in resistor factories, shedding light on the methods and materials that contribute to the creation of these vital components.
II. Types of Resistors
Resistors come in various types, each designed for specific applications and performance characteristics. Understanding these types is essential for grasping the production processes involved.
A. Fixed Resistors
1. **Carbon Composition Resistors**: These resistors are made from a mixture of carbon particles and a binding material. They are known for their high energy absorption and are often used in applications where high pulse loads are expected.
2. **Metal Film Resistors**: Constructed from a thin layer of metal, these resistors offer high precision and stability. They are widely used in applications requiring accurate resistance values.
3. **Wirewound Resistors**: Made by winding a metal wire around a ceramic or fiberglass core, wirewound resistors are known for their high power ratings and are commonly used in power applications.
B. Variable Resistors
1. **Potentiometers**: These resistors allow for adjustable resistance and are often used in volume controls and tuning circuits.
2. **Rheostats**: Similar to potentiometers, rheostats are used to control current flow in a circuit, typically in higher power applications.
C. Specialty Resistors
1. **Thermistors**: These temperature-sensitive resistors are used in temperature sensing and control applications.
2. **Photoresistors**: Also known as light-dependent resistors (LDRs), these components change resistance based on light exposure, making them ideal for light-sensing applications.
III. Raw Materials Used in Resistor Production
The production of resistors requires a variety of raw materials, each contributing to the final product's performance and reliability.
A. Conductive Materials
1. **Carbon**: Used primarily in carbon composition resistors, carbon provides the necessary conductivity and resistance characteristics.
2. **Metal Oxides**: Commonly used in metal film resistors, metal oxides offer stability and precision in resistance values.
3. **Metal Wires**: Essential for wirewound resistors, metal wires (often made of nickel-chromium or copper) provide the necessary conductivity and durability.
B. Insulating Materials
1. **Ceramic Substrates**: These materials are used to provide insulation and mechanical support for resistors, particularly in wirewound designs.
2. **Epoxy Resins**: Used for coating and protecting resistors, epoxy resins offer excellent insulation properties and environmental resistance.
C. Other Components
1. **Lead Wires**: These are used to connect resistors to circuits, ensuring reliable electrical connections.
2. **Protective Coatings**: Coatings are applied to resistors to protect them from environmental factors and mechanical damage.
IV. Common Production Processes
The production of resistors involves several key processes, each critical to ensuring the quality and performance of the final product.
A. Material Preparation
1. **Sourcing and Quality Control of Raw Materials**: The first step in resistor production is sourcing high-quality raw materials. Manufacturers conduct rigorous quality control checks to ensure that materials meet specific standards.
2. **Pre-processing of Materials**: This may involve grinding carbon powder, mixing conductive materials, and preparing metal wires for further processing.
B. Resistor Element Fabrication
1. **Carbon Composition Resistors**:
- **Mixing Carbon Powder with a Binder**: The carbon powder is mixed with a binding agent to create a paste.
- **Molding and Curing**: The paste is molded into the desired shape and cured to harden the material.
2. **Metal Film Resistors**:
- **Thin Film Deposition Techniques**: Techniques such as sputtering or evaporation are used to deposit a thin layer of metal onto a substrate.
- **Laser Trimming for Precision**: After deposition, laser trimming is employed to achieve precise resistance values.
3. **Wirewound Resistors**:
- **Winding Wire Around a Core**: A metal wire is wound around a ceramic or fiberglass core to create the resistor element.
- **Insulation and Coating Application**: The wound resistor is then insulated and coated to protect it from environmental factors.
C. Assembly Process
1. **Mounting Resistor Elements onto Substrates**: The fabricated resistor elements are mounted onto insulating substrates, which provide mechanical support and electrical insulation.
2. **Soldering and Connecting Lead Wires**: Lead wires are soldered to the resistor elements, ensuring reliable electrical connections for integration into circuits.
D. Testing and Quality Control
1. **Electrical Testing**: Each resistor undergoes electrical testing to measure resistance values and ensure they meet specifications.
2. **Environmental Testing**: Resistors are subjected to environmental tests, including temperature and humidity exposure, to assess their performance under various conditions.
3. **Visual Inspection for Defects**: A thorough visual inspection is conducted to identify any defects or inconsistencies in the resistors.
E. Packaging and Distribution
1. **Packaging Methods**: Resistors are packaged using various methods, including bulk packaging and tape-and-reel systems for automated assembly lines.
2. **Logistics and Distribution Channels**: Efficient logistics and distribution channels are established to ensure timely delivery to customers and manufacturers.
V. Automation and Technology in Resistor Manufacturing
The resistor manufacturing industry has seen significant advancements in automation and technology, enhancing production efficiency and product quality.
A. Role of Automation in Production Efficiency
Automation plays a crucial role in streamlining production processes, reducing labor costs, and minimizing human error. Automated systems can handle repetitive tasks, allowing skilled workers to focus on more complex operations.
B. Advanced Technologies in Quality Control
Technologies such as robotics and artificial intelligence (AI) are increasingly being integrated into quality control processes. These technologies enable real-time monitoring and analysis, ensuring that any defects are identified and addressed promptly.
C. Future Trends in Resistor Manufacturing Processes
As the electronics industry continues to evolve, resistor manufacturing processes are expected to become more sophisticated. Trends such as the use of advanced materials, increased automation, and sustainable practices are likely to shape the future of resistor production.
VI. Environmental Considerations
The production of resistors also raises important environmental considerations that manufacturers must address.
A. Waste Management in Resistor Production
Effective waste management practices are essential to minimize the environmental impact of resistor manufacturing. This includes recycling materials and properly disposing of hazardous waste.
B. Sustainable Practices in Sourcing Materials
Manufacturers are increasingly focusing on sustainable sourcing practices, ensuring that raw materials are obtained responsibly and ethically.
C. Compliance with Environmental Regulations
Compliance with environmental regulations is critical for resistor manufacturers. Adhering to these regulations not only helps protect the environment but also enhances the company's reputation and marketability.
VII. Conclusion
Understanding the common production processes in resistor factories is essential for appreciating the complexity and importance of these components in electronic circuits. The manufacturing processes directly impact the quality and performance of resistors, influencing their reliability in various applications. As technology advances and environmental considerations become more prominent, the future of resistor manufacturing will likely see continued innovation and improvement, ensuring that these vital components meet the demands of the ever-evolving electronics industry.
VIII. References
For further exploration of resistor manufacturing processes, consider the following resources:
1. "Resistor Technology: A Comprehensive Guide" - A detailed book covering various aspects of resistor technology and manufacturing.
2. "The Electronics Handbook" - A reference book that includes information on electronic components, including resistors.
3. Industry journals and publications that focus on advancements in electronics manufacturing and materials science.
By delving into these resources, readers can gain a deeper understanding of the intricacies involved in resistor production and the broader context of electronic component manufacturing.