Common Production Processes for Load Resistors
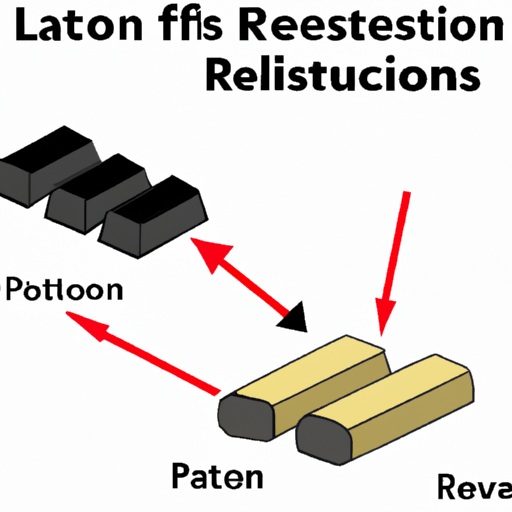
I. Introduction
Load resistors are essential components in electronic circuits, serving the critical function of managing electrical loads and ensuring the stability of various systems. These resistors dissipate energy in the form of heat, allowing circuits to operate safely and efficiently. As technology advances, the demand for high-quality load resistors has increased, necessitating a thorough understanding of their production processes. This blog post will explore the common production processes for load resistors, detailing the materials used, manufacturing techniques, and the importance of quality assurance.
II. Types of Load Resistors
Load resistors can be categorized into three main types:
A. Fixed Load Resistors
Fixed load resistors have a predetermined resistance value that does not change. They are widely used in applications where a stable load is required, such as in power supplies and voltage dividers.
B. Variable Load Resistors
Variable load resistors, also known as rheostats or potentiometers, allow users to adjust the resistance value. This flexibility makes them ideal for applications like dimmer switches and audio equipment.
C. Specialty Load Resistors
Specialty load resistors are designed for specific applications, such as high-power resistors for industrial use or precision resistors for measurement devices. These resistors often have unique characteristics tailored to their intended use.
III. Materials Used in Load Resistor Production
The performance and reliability of load resistors depend significantly on the materials used in their production.
A. Conductive Materials
1. **Carbon Composition**: Carbon resistors are made from a mixture of carbon and a binding material. They are cost-effective and suitable for low-power applications but have limitations in terms of precision and stability.
2. **Metal Film**: Metal film resistors are made by depositing a thin layer of metal onto a ceramic substrate. They offer better accuracy and stability compared to carbon resistors, making them ideal for precision applications.
3. **Wire Wound**: Wire wound resistors consist of a wire, usually made of nickel-chromium alloy, wound around a ceramic core. They can handle high power and are often used in applications requiring high precision and stability.
B. Insulating Materials
1. **Ceramic**: Ceramic materials are commonly used for their excellent thermal stability and electrical insulation properties. They are often used as substrates for metal film resistors.
2. **Epoxy**: Epoxy resins provide good insulation and protection against environmental factors. They are often used as coatings for resistors to enhance durability.
C. Heat Dissipation Materials
Effective heat dissipation is crucial for load resistors to prevent overheating. Materials such as aluminum and copper are often used in the construction of heat sinks to enhance thermal management.
IV. Common Production Processes
The production of load resistors involves several key processes, each contributing to the final product's quality and performance.
A. Design and Prototyping
1. **Electrical Specifications**: The first step in the production process is defining the electrical specifications, including resistance value, power rating, and tolerance. These specifications guide the design and material selection.
2. **Mechanical Design**: The mechanical design involves creating a blueprint for the resistor's physical structure, considering factors such as size, shape, and mounting options.
3. **Prototyping Techniques**: Prototyping allows manufacturers to test and refine their designs before full-scale production. Techniques such as 3D printing and CNC machining are commonly used to create prototypes.
B. Material Selection
1. **Criteria for Material Selection**: Selecting the right materials is critical for ensuring the resistor's performance. Factors such as electrical conductivity, thermal stability, and cost are considered during this process.
2. **Sourcing and Quality Control**: Manufacturers must source high-quality materials from reliable suppliers. Quality control measures are implemented to ensure that materials meet the required specifications.
C. Manufacturing Techniques
1. **Cutting and Shaping**:
a. **Laser Cutting**: Laser cutting is a precise method used to cut materials into specific shapes. It is often used for creating metal film resistors.
b. **CNC Machining**: Computer Numerical Control (CNC) machining allows for high precision in shaping materials, making it suitable for producing wire wound resistors.
2. **Assembly Processes**:
a. **Soldering**: Soldering is a common method for joining components in load resistors. It involves melting a filler metal to create a strong electrical connection.
b. **Welding**: Welding techniques, such as resistance welding, are used for high-power resistors to ensure robust connections.
3. **Coating and Finishing**:
a. **Surface Treatments**: Surface treatments, such as anodizing or plating, enhance the resistor's durability and resistance to corrosion.
b. **Protective Coatings**: Applying protective coatings, such as epoxy, helps shield resistors from environmental factors and mechanical stress.
D. Testing and Quality Assurance
1. **Electrical Testing**: Each resistor undergoes electrical testing to verify its resistance value, power rating, and tolerance. This ensures that the product meets the specified electrical performance.
2. **Thermal Testing**: Thermal testing evaluates the resistor's ability to dissipate heat under load conditions. This is crucial for preventing overheating and ensuring reliability.
3. **Mechanical Testing**: Mechanical testing assesses the physical durability of the resistor, including its resistance to vibration, shock, and environmental conditions.
V. Automation in Load Resistor Production
A. Role of Automation in Efficiency
Automation plays a significant role in enhancing the efficiency of load resistor production. Automated processes reduce human error, increase production speed, and lower labor costs.
B. Use of Robotics and AI in Manufacturing
Robotics and artificial intelligence (AI) are increasingly being integrated into manufacturing processes. Robots can perform repetitive tasks with high precision, while AI can optimize production schedules and quality control.
C. Impact on Quality and Consistency
Automation contributes to improved quality and consistency in load resistor production. With precise control over manufacturing processes, manufacturers can produce resistors that meet stringent quality standards.
VI. Environmental Considerations
A. Sustainable Materials
The electronics industry is increasingly focusing on sustainability. Manufacturers are exploring the use of sustainable materials, such as biodegradable plastics and recycled metals, in load resistor production.
B. Waste Management in Production
Effective waste management practices are essential to minimize the environmental impact of production. Manufacturers are implementing recycling programs and waste reduction strategies to manage by-products.
C. Compliance with Environmental Regulations
Compliance with environmental regulations is crucial for manufacturers. Adhering to standards such as RoHS (Restriction of Hazardous Substances) ensures that products are safe for consumers and the environment.
VII. Conclusion
In summary, the production processes for load resistors involve a complex interplay of design, material selection, manufacturing techniques, and quality assurance. As technology continues to evolve, manufacturers must adapt to new trends and challenges, including automation and sustainability. Continuous improvement in production methods will be essential to meet the growing demand for high-quality load resistors in an increasingly electronic world.
VIII. References
1. Academic journals on electronics and materials science.
2. Industry reports on resistor manufacturing trends.
3. Manufacturer guidelines for load resistor production standards.
By understanding these common production processes, stakeholders in the electronics industry can appreciate the intricacies involved in creating reliable load resistors that are vital for modern electronic applications.
Common Production Processes for Load Resistors
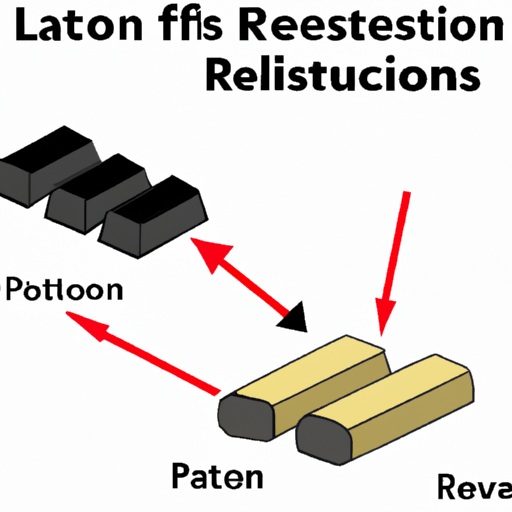
I. Introduction
Load resistors are essential components in electronic circuits, serving the critical function of managing electrical loads and ensuring the stability of various systems. These resistors dissipate energy in the form of heat, allowing circuits to operate safely and efficiently. As technology advances, the demand for high-quality load resistors has increased, necessitating a thorough understanding of their production processes. This blog post will explore the common production processes for load resistors, detailing the materials used, manufacturing techniques, and the importance of quality assurance.
II. Types of Load Resistors
Load resistors can be categorized into three main types:
A. Fixed Load Resistors
Fixed load resistors have a predetermined resistance value that does not change. They are widely used in applications where a stable load is required, such as in power supplies and voltage dividers.
B. Variable Load Resistors
Variable load resistors, also known as rheostats or potentiometers, allow users to adjust the resistance value. This flexibility makes them ideal for applications like dimmer switches and audio equipment.
C. Specialty Load Resistors
Specialty load resistors are designed for specific applications, such as high-power resistors for industrial use or precision resistors for measurement devices. These resistors often have unique characteristics tailored to their intended use.
III. Materials Used in Load Resistor Production
The performance and reliability of load resistors depend significantly on the materials used in their production.
A. Conductive Materials
1. **Carbon Composition**: Carbon resistors are made from a mixture of carbon and a binding material. They are cost-effective and suitable for low-power applications but have limitations in terms of precision and stability.
2. **Metal Film**: Metal film resistors are made by depositing a thin layer of metal onto a ceramic substrate. They offer better accuracy and stability compared to carbon resistors, making them ideal for precision applications.
3. **Wire Wound**: Wire wound resistors consist of a wire, usually made of nickel-chromium alloy, wound around a ceramic core. They can handle high power and are often used in applications requiring high precision and stability.
B. Insulating Materials
1. **Ceramic**: Ceramic materials are commonly used for their excellent thermal stability and electrical insulation properties. They are often used as substrates for metal film resistors.
2. **Epoxy**: Epoxy resins provide good insulation and protection against environmental factors. They are often used as coatings for resistors to enhance durability.
C. Heat Dissipation Materials
Effective heat dissipation is crucial for load resistors to prevent overheating. Materials such as aluminum and copper are often used in the construction of heat sinks to enhance thermal management.
IV. Common Production Processes
The production of load resistors involves several key processes, each contributing to the final product's quality and performance.
A. Design and Prototyping
1. **Electrical Specifications**: The first step in the production process is defining the electrical specifications, including resistance value, power rating, and tolerance. These specifications guide the design and material selection.
2. **Mechanical Design**: The mechanical design involves creating a blueprint for the resistor's physical structure, considering factors such as size, shape, and mounting options.
3. **Prototyping Techniques**: Prototyping allows manufacturers to test and refine their designs before full-scale production. Techniques such as 3D printing and CNC machining are commonly used to create prototypes.
B. Material Selection
1. **Criteria for Material Selection**: Selecting the right materials is critical for ensuring the resistor's performance. Factors such as electrical conductivity, thermal stability, and cost are considered during this process.
2. **Sourcing and Quality Control**: Manufacturers must source high-quality materials from reliable suppliers. Quality control measures are implemented to ensure that materials meet the required specifications.
C. Manufacturing Techniques
1. **Cutting and Shaping**:
a. **Laser Cutting**: Laser cutting is a precise method used to cut materials into specific shapes. It is often used for creating metal film resistors.
b. **CNC Machining**: Computer Numerical Control (CNC) machining allows for high precision in shaping materials, making it suitable for producing wire wound resistors.
2. **Assembly Processes**:
a. **Soldering**: Soldering is a common method for joining components in load resistors. It involves melting a filler metal to create a strong electrical connection.
b. **Welding**: Welding techniques, such as resistance welding, are used for high-power resistors to ensure robust connections.
3. **Coating and Finishing**:
a. **Surface Treatments**: Surface treatments, such as anodizing or plating, enhance the resistor's durability and resistance to corrosion.
b. **Protective Coatings**: Applying protective coatings, such as epoxy, helps shield resistors from environmental factors and mechanical stress.
D. Testing and Quality Assurance
1. **Electrical Testing**: Each resistor undergoes electrical testing to verify its resistance value, power rating, and tolerance. This ensures that the product meets the specified electrical performance.
2. **Thermal Testing**: Thermal testing evaluates the resistor's ability to dissipate heat under load conditions. This is crucial for preventing overheating and ensuring reliability.
3. **Mechanical Testing**: Mechanical testing assesses the physical durability of the resistor, including its resistance to vibration, shock, and environmental conditions.
V. Automation in Load Resistor Production
A. Role of Automation in Efficiency
Automation plays a significant role in enhancing the efficiency of load resistor production. Automated processes reduce human error, increase production speed, and lower labor costs.
B. Use of Robotics and AI in Manufacturing
Robotics and artificial intelligence (AI) are increasingly being integrated into manufacturing processes. Robots can perform repetitive tasks with high precision, while AI can optimize production schedules and quality control.
C. Impact on Quality and Consistency
Automation contributes to improved quality and consistency in load resistor production. With precise control over manufacturing processes, manufacturers can produce resistors that meet stringent quality standards.
VI. Environmental Considerations
A. Sustainable Materials
The electronics industry is increasingly focusing on sustainability. Manufacturers are exploring the use of sustainable materials, such as biodegradable plastics and recycled metals, in load resistor production.
B. Waste Management in Production
Effective waste management practices are essential to minimize the environmental impact of production. Manufacturers are implementing recycling programs and waste reduction strategies to manage by-products.
C. Compliance with Environmental Regulations
Compliance with environmental regulations is crucial for manufacturers. Adhering to standards such as RoHS (Restriction of Hazardous Substances) ensures that products are safe for consumers and the environment.
VII. Conclusion
In summary, the production processes for load resistors involve a complex interplay of design, material selection, manufacturing techniques, and quality assurance. As technology continues to evolve, manufacturers must adapt to new trends and challenges, including automation and sustainability. Continuous improvement in production methods will be essential to meet the growing demand for high-quality load resistors in an increasingly electronic world.
VIII. References
1. Academic journals on electronics and materials science.
2. Industry reports on resistor manufacturing trends.
3. Manufacturer guidelines for load resistor production standards.
By understanding these common production processes, stakeholders in the electronics industry can appreciate the intricacies involved in creating reliable load resistors that are vital for modern electronic applications.